Notice: We request that you don't just set up a new account at this time if you are a previous user.
If you used to be one of our moderators, please feel free to reach out to Chris via the facebook Outerlimits4x4 group and he will get you set back up with access should he need you.
If you used to be one of our moderators, please feel free to reach out to Chris via the facebook Outerlimits4x4 group and he will get you set back up with access should he need you.
Recovery:If you cannot access your old email address and don't remember your password, please click here to log a change of email address so you can do a password reset.
The Welding Thread
Moderators: toaddog, TWISTY, V8Patrol, Moderators
Re: The Welding Thread
That's good news Milo.
Everything you told me on the phone pointed to a gas issue, it's good you sorted it out and it will give you confidence your machine is fine.
In the meantime, below is an Ebay link to one of those Binzel gas flow testers I was telling you about.
I would highly recommend you get one even it's just to save you wasted gas.
http://www.ebay.com.au/itm/Gas-Air-Flow ... 5d39b2446b
They are also available from BOC according to their website.
https://www.boc.com.au/webapp/wcs/store ... p1910003-p
I'll check the gas flow at the torch every couple of days as you tend to get gauge creep where as the volume of gas in the bottle goes down the flow of gas through the torch actually increases.
As I said to you the sweet spot for my machine is 7.5 litres per minute at the torch.
Regards Andrew.
Everything you told me on the phone pointed to a gas issue, it's good you sorted it out and it will give you confidence your machine is fine.
In the meantime, below is an Ebay link to one of those Binzel gas flow testers I was telling you about.
I would highly recommend you get one even it's just to save you wasted gas.
http://www.ebay.com.au/itm/Gas-Air-Flow ... 5d39b2446b
They are also available from BOC according to their website.
https://www.boc.com.au/webapp/wcs/store ... p1910003-p
I'll check the gas flow at the torch every couple of days as you tend to get gauge creep where as the volume of gas in the bottle goes down the flow of gas through the torch actually increases.
As I said to you the sweet spot for my machine is 7.5 litres per minute at the torch.
Regards Andrew.
We are Tig welders, gravity doesn't worry us.
[img]http://www.studmonkeyracing.com/forums/smilies/weld.gif[/img]
[img]http://www.studmonkeyracing.com/forums/smilies/weld.gif[/img]
Re: The Welding Thread
My argon reg has a flow metre on it as like the one in your linkawill4x4 wrote:That's good news Milo.
Everything you told me on the phone pointed to a gas issue, it's good you sorted it out and it will give you confidence your machine is fine.
In the meantime, below is an Ebay link to one of those Binzel gas flow testers I was telling you about.
I would highly recommend you get one even it's just to save you wasted gas.
http://www.ebay.com.au/itm/Gas-Air-Flow ... 5d39b2446b
They are also available from BOC according to their website.
https://www.boc.com.au/webapp/wcs/store ... p1910003-p
I'll check the gas flow at the torch every couple of days as you tend to get gauge creep where as the volume of gas in the bottle goes down the flow of gas through the torch actually increases.
As I said to you the sweet spot for my machine is 7.5 litres per minute at the torch.
Regards Andrew.
Is that doing the same job?
03 HDJ100R GXL / 94 FJ45-80
Re: The Welding Thread
It does the job up to a point.Shadow wrote: My argon reg has a flow metre on it as like the one in your link
Is that doing the same job?
Different torches, be the Mig or Tig will flow differently as some are more restrictive than others on the way they flow gas.
My bobbin at the regulator will be showing around 15 litres per minute while at the torch it's actually 7.5 litres per minute.
I find that at about 6 litres per min I start to get signs of gas flow impurities so I stay at 7.5 to be on the safe side.
Any more than that then I'm just wasting gas except in special circumstances that may require especially long stickouts for the Tungsten, or for oxygen sensitive materials like Titanium.
Regards Andrew.
We are Tig welders, gravity doesn't worry us.
[img]http://www.studmonkeyracing.com/forums/smilies/weld.gif[/img]
[img]http://www.studmonkeyracing.com/forums/smilies/weld.gif[/img]
Re: The Welding Thread
Are you using the same flow meter to measure in the two different spots, or two different flow meters? That style of flow meter is calibrated for the density of a specific gas; the meter in the first link doesn't state the gas for which it is calibrated, so it may not read your gas accurately i.e. the number may not be correct.awill4x4 wrote:My bobbin at the regulator will be showing around 15 litres per minute while at the torch it's actually 7.5 litres per minute.
However, it should measure precisely i.e. the same number every time. If you're interested in maintaining the same flow all the time, then it should do that well.
Re: The Welding Thread
-Scott- wrote:Are you using the same flow meter to measure in the two different spots, or two different flow meters? That style of flow meter is calibrated for the density of a specific gas; the meter in the first link doesn't state the gas for which it is calibrated, so it may not read your gas accurately i.e. the number may not be correct.awill4x4 wrote:My bobbin at the regulator will be showing around 15 litres per minute while at the torch it's actually 7.5 litres per minute.
However, it should measure precisely i.e. the same number every time. If you're interested in maintaining the same flow all the time, then it should do that well.
different meter, same type.
one is fixed to the argon regulator
the other is one you jam on the end of the torch
in my mind, if the one on the reg says 15l/min, and the one on the roch says 7l/min, then your leaking 8l/min along the line somwhere?
or 1 opf the meters or both, is shit
03 HDJ100R GXL / 94 FJ45-80
Re: The Welding Thread
Yep. Either that, or the gas is contracting significantly along the line, but I severely doubt that's the case.Shadow wrote:in my mind, if the one on the reg says 15l/min, and the one on the roch says 7l/min, then your leaking 8l/min along the line somwhere?
Or, if the Rotameter on the torch isn't calibrated for Argon, the numbers are simply not accurate.
http://en.wikipedia.org/wiki/Rotameter" onclick="window.open(this.href);return false;
Re: The Welding Thread
Have either of you ever seen just how restrictive the gas line is in a water cooled Tig torch?
I haven't found one regulator at the bottle that shows an accurate gas rate of flow at the end of an 8 meter water cooled Tig torch.
Measuring at the torch is the only accurate way of getting the right amount of gas to do the job.
Regards Andrew.
ps: I've got 2 of these torch gas flow testers and both read the same, my mate has got one also and his reads identical.
I haven't found one regulator at the bottle that shows an accurate gas rate of flow at the end of an 8 meter water cooled Tig torch.
Measuring at the torch is the only accurate way of getting the right amount of gas to do the job.
Regards Andrew.
ps: I've got 2 of these torch gas flow testers and both read the same, my mate has got one also and his reads identical.
We are Tig welders, gravity doesn't worry us.
[img]http://www.studmonkeyracing.com/forums/smilies/weld.gif[/img]
[img]http://www.studmonkeyracing.com/forums/smilies/weld.gif[/img]
Re: The Welding Thread
Bit quiet around these parts
Back at trade school this week and they let me outta the cage and into the bays so I could have a crack at aluminium TIG welding. Took me a few goes to get it but I passed in the end
This is the only photo I got
Welder is a Cigweld Transtig 200

This stuff was easier than the 1.2mm zinc sheet i was TIG'ing before. Probably because it is heavier gauge and a little easier to work with. This was my first attempt at an outside corner run. Real happy with how it came out and Im keen to have another crack tomorrow. Ill see if I can right down some numbers aswell for those interested.
Cheers
Chook

Back at trade school this week and they let me outta the cage and into the bays so I could have a crack at aluminium TIG welding. Took me a few goes to get it but I passed in the end

This is the only photo I got
Welder is a Cigweld Transtig 200

This stuff was easier than the 1.2mm zinc sheet i was TIG'ing before. Probably because it is heavier gauge and a little easier to work with. This was my first attempt at an outside corner run. Real happy with how it came out and Im keen to have another crack tomorrow. Ill see if I can right down some numbers aswell for those interested.
Cheers
Chook
love_mud wrote: my hose is small .. but it's comfortable and full of life.
Re: The Welding Thread
Excellent work Chook.
It's great to see people having a go at Tig welding.
Regards Andrew.
It's great to see people having a go at Tig welding.
Regards Andrew.
We are Tig welders, gravity doesn't worry us.
[img]http://www.studmonkeyracing.com/forums/smilies/weld.gif[/img]
[img]http://www.studmonkeyracing.com/forums/smilies/weld.gif[/img]
Re: The Welding Thread
Sierra spring perches on Vitara based floater axle.
Milled 100x5x3mm RHS using the work welder: WIA Weldmatic 350

Milled 100x5x3mm RHS using the work welder: WIA Weldmatic 350

Last edited by SierraDan on Tue Mar 05, 2013 5:34 pm, edited 1 time in total.
Re: The Welding Thread




Just thought i would put a few of mine up to be critiqued. Done useing my Kempi MLS2300 3.2 thoriated tungsten and 1.6 filler, first 2 passes at 120A and cap at 95A. I think its alright for a fitter, self taught so be gentle.
I started life with nothing, and I still have most of it!
Re: The Welding Thread
Thought I had posted all my stuff in here but turns out that was the TOTT thread
Was slow one day at work so my workshop manager came out and said "Chook, you're gonna build me a trailer"
No worries, being a second year welder/fabricator I thought this would be pretty sweet, haven't had many start through to finish style projects before.
So It started with a basic frame, 50x50x3 RHS. 2200 long by 1220 wide (7x4?)

I also added 16mmID tube to the inside of the rear crossmember for cables to pass through. Brake/light cables will run through the draw bar.
Made a deliberate effort to make sure that if I was the one building it, then sure as hell I'd be happy with how it turned out in every aspect. Good chance to get into the bosses good books aswell

Draw bar stuck out by 1500mm from the front rail. Measured the front of the drawbar to the axle centreline, dead square (a vital measurement that will be scrutinized when the trailer gets hauled over the pits at Regency)
Draw bar is 75x50x3 RHS

Sheetmetal on top is 2mm thick. Strength wasn't the major factor here, this trailer will hold 2 quad bikes, toolbox and spare-wheel.
Because sheets come in at 2400 long, had to whip out the plasma and remove 203mm from the end. This made the sheet 3mm short, meaning I could weld around the outside then smooth it off enough and make a nice radius around the corners while still being plenty strong enough.
Clamping into place before it gets tacked down.

Here you can see where the sheet as warped slightly around the crossmembers. Not an issue, flat surface not required. Either couldve used thicker sheet or way more braces to keep it level but that would throw the weight goal out the window.

6mm plate on the front of the drawbar to mount the hitch and possibly jockey wheel mount. Welded around every edge. Was about as hot As I could go before I ran the risk of burning through the thinner RHS.

Added 2 braces to the draw bar where the toolbox and spare wheel will sit. 50x50x3 RHS. The piece running backwards to the front chassis member has a fish-plate on the back end which sits on the rear face of the cross-member, and is then welded around all 4 edges. Hope that makes sense
Gave it a lick of paint as it was going to sit outside for a few weeks over the Christmas period.

After christmas I spent a whole day wire wheeling the axles and rims, cleaning booger welded spring perches off the axle, and discovering why the hubs refused to turn. Mud inside hubs makes for a terrible grease substitute
Forgot to take photos of the axle and springs mounted. Apparently welding to the axles is highly illegal! Buggered If I knew. Got all excited because I had some nice perches drawn up that I was going to make but the plan went up shit creek
Axles and springs in and tow hitch bolted on.
Fast forward a few weeks and it's time to set up the sides and front/rear tailgates.
2mm sides that were bent up by another machine shop. They sit 310mm high. Received 3 pieces at 2400 long. This meant I had to cut down 2 of the sides to 2200, and the third one down to 1220. This unfortunately meant I was stuck with an offcut 40mm too short
Dea
l with that later.
Put a 50x50x2 RHS brace along the bottom edge, and 2 50x50x5 angle iron pieces on the end. A 25x25x2 vertical brace in the middle aswell.

All welded up. The sheetmetal stayed fine but the RHS bowed a little. Across 1200mm there was a 6mm bow in the middle. The 300 ton press straightened it out no worries.

All cleaned up and now to start the 2nd one. The second was was more work because I had to cut a 40mm wide strip from one of the bent side offcuts and weld it onto the piece 1180 long in order to make up the required length. Pain in the ass but some massaging from the hammer and a few blocks of wood and she came up fine.

Once that was done, we mounted the front and rear panels to the side panels which were already squared up and tacked on. The front is mounted solid but the rear has 3 big arse hinges welded on which also makes it easily removeable. No photos of hinges but Ill snap some tomorrow. Front and rear panels done, now time to tack on the rolled guards and some 50x50x2 braces to the guards from the front and rear of the chassis. This give the guards some fighting chance should they ever take a beating.

4mm Plate on either side of the front and rear panels are for lights and some small tube running front to rear as a tie down rail. I will wait until the lights etc are all mounted before I cut a nice looking profile into the plates.

Front brace was approx 890mm long and the rear was approx 520. I put an extra brace back to the chassis on the long side to minimize any deflection.

After everything was tacked in place, I pulled on my leather sleeves and spent 3 hrs behind me helmet
Guards were stitched on, all RHS was welded all the way round in position.

Inside of guard

The front and side panels were stitched 50mm, skipped 150, and repeat all around, both on inside and out

Best shot I have of tailgate and hinges, you get the idea

So that's where Im up to at the moment. Still need to:
Mount rear lights
Weld in tie down rails with braces to the top of the guards
Make up removeable pin style locks for the rear tailgate. Got a good idea for that one.
Mount jockey wheel
Mount toolbox, will require some small tabs on front draw bar so it can be bolted down.
Drill hole near front of drawbar for cables to pass through.
And then paint the whole bang lot.
It's not on par with Ben Napier's Ultra 4 build (which I have read religiously on Pirate
) but for a second year apprentice I'm pretty wrapped with it. The whole idea is that if anybody every says "Shit, that came up pretty good" I can stand there with a dirty big grin on me face
Apologies for the long read but this seemed more appropriate than the TOTT thread
Cheers guys
Chook

Was slow one day at work so my workshop manager came out and said "Chook, you're gonna build me a trailer"
No worries, being a second year welder/fabricator I thought this would be pretty sweet, haven't had many start through to finish style projects before.
So It started with a basic frame, 50x50x3 RHS. 2200 long by 1220 wide (7x4?)

I also added 16mmID tube to the inside of the rear crossmember for cables to pass through. Brake/light cables will run through the draw bar.
Made a deliberate effort to make sure that if I was the one building it, then sure as hell I'd be happy with how it turned out in every aspect. Good chance to get into the bosses good books aswell


Draw bar stuck out by 1500mm from the front rail. Measured the front of the drawbar to the axle centreline, dead square (a vital measurement that will be scrutinized when the trailer gets hauled over the pits at Regency)
Draw bar is 75x50x3 RHS

Sheetmetal on top is 2mm thick. Strength wasn't the major factor here, this trailer will hold 2 quad bikes, toolbox and spare-wheel.
Because sheets come in at 2400 long, had to whip out the plasma and remove 203mm from the end. This made the sheet 3mm short, meaning I could weld around the outside then smooth it off enough and make a nice radius around the corners while still being plenty strong enough.
Clamping into place before it gets tacked down.

Here you can see where the sheet as warped slightly around the crossmembers. Not an issue, flat surface not required. Either couldve used thicker sheet or way more braces to keep it level but that would throw the weight goal out the window.

6mm plate on the front of the drawbar to mount the hitch and possibly jockey wheel mount. Welded around every edge. Was about as hot As I could go before I ran the risk of burning through the thinner RHS.

Added 2 braces to the draw bar where the toolbox and spare wheel will sit. 50x50x3 RHS. The piece running backwards to the front chassis member has a fish-plate on the back end which sits on the rear face of the cross-member, and is then welded around all 4 edges. Hope that makes sense

Gave it a lick of paint as it was going to sit outside for a few weeks over the Christmas period.

After christmas I spent a whole day wire wheeling the axles and rims, cleaning booger welded spring perches off the axle, and discovering why the hubs refused to turn. Mud inside hubs makes for a terrible grease substitute

Forgot to take photos of the axle and springs mounted. Apparently welding to the axles is highly illegal! Buggered If I knew. Got all excited because I had some nice perches drawn up that I was going to make but the plan went up shit creek

Axles and springs in and tow hitch bolted on.
Fast forward a few weeks and it's time to set up the sides and front/rear tailgates.
2mm sides that were bent up by another machine shop. They sit 310mm high. Received 3 pieces at 2400 long. This meant I had to cut down 2 of the sides to 2200, and the third one down to 1220. This unfortunately meant I was stuck with an offcut 40mm too short

l with that later.
Put a 50x50x2 RHS brace along the bottom edge, and 2 50x50x5 angle iron pieces on the end. A 25x25x2 vertical brace in the middle aswell.

All welded up. The sheetmetal stayed fine but the RHS bowed a little. Across 1200mm there was a 6mm bow in the middle. The 300 ton press straightened it out no worries.

All cleaned up and now to start the 2nd one. The second was was more work because I had to cut a 40mm wide strip from one of the bent side offcuts and weld it onto the piece 1180 long in order to make up the required length. Pain in the ass but some massaging from the hammer and a few blocks of wood and she came up fine.

Once that was done, we mounted the front and rear panels to the side panels which were already squared up and tacked on. The front is mounted solid but the rear has 3 big arse hinges welded on which also makes it easily removeable. No photos of hinges but Ill snap some tomorrow. Front and rear panels done, now time to tack on the rolled guards and some 50x50x2 braces to the guards from the front and rear of the chassis. This give the guards some fighting chance should they ever take a beating.

4mm Plate on either side of the front and rear panels are for lights and some small tube running front to rear as a tie down rail. I will wait until the lights etc are all mounted before I cut a nice looking profile into the plates.

Front brace was approx 890mm long and the rear was approx 520. I put an extra brace back to the chassis on the long side to minimize any deflection.

After everything was tacked in place, I pulled on my leather sleeves and spent 3 hrs behind me helmet

Guards were stitched on, all RHS was welded all the way round in position.

Inside of guard

The front and side panels were stitched 50mm, skipped 150, and repeat all around, both on inside and out

Best shot I have of tailgate and hinges, you get the idea


So that's where Im up to at the moment. Still need to:
Mount rear lights
Weld in tie down rails with braces to the top of the guards
Make up removeable pin style locks for the rear tailgate. Got a good idea for that one.
Mount jockey wheel
Mount toolbox, will require some small tabs on front draw bar so it can be bolted down.
Drill hole near front of drawbar for cables to pass through.
And then paint the whole bang lot.
It's not on par with Ben Napier's Ultra 4 build (which I have read religiously on Pirate


Apologies for the long read but this seemed more appropriate than the TOTT thread
Cheers guys
Chook
love_mud wrote: my hose is small .. but it's comfortable and full of life.
Re: The Welding Thread
looks good mate, nice and strong
Re: The Welding Thread
Some boogers on my floater.
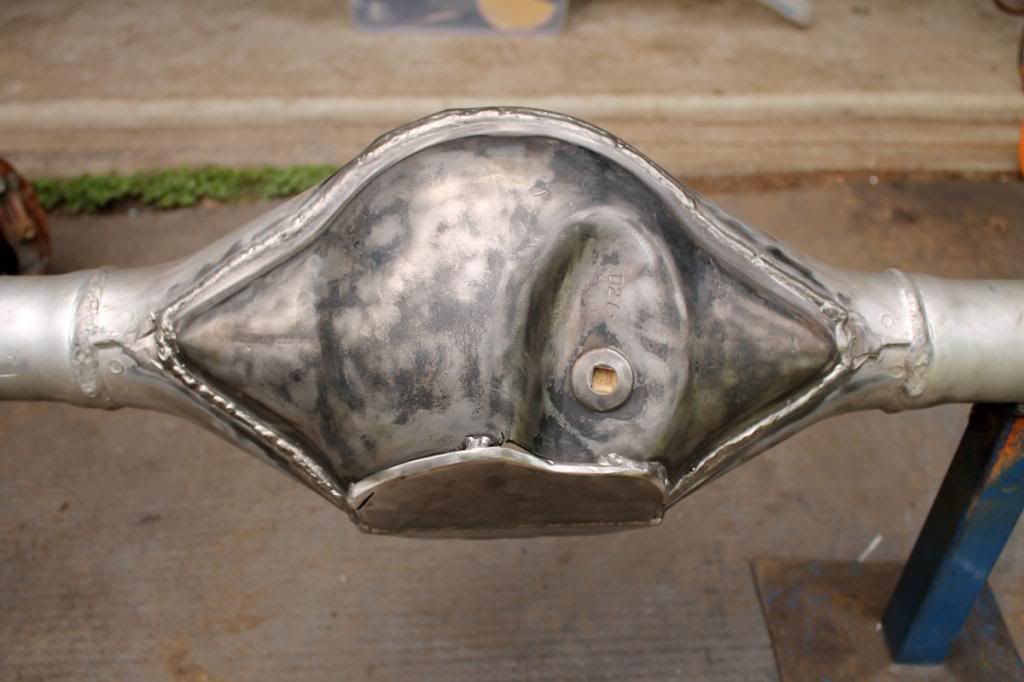
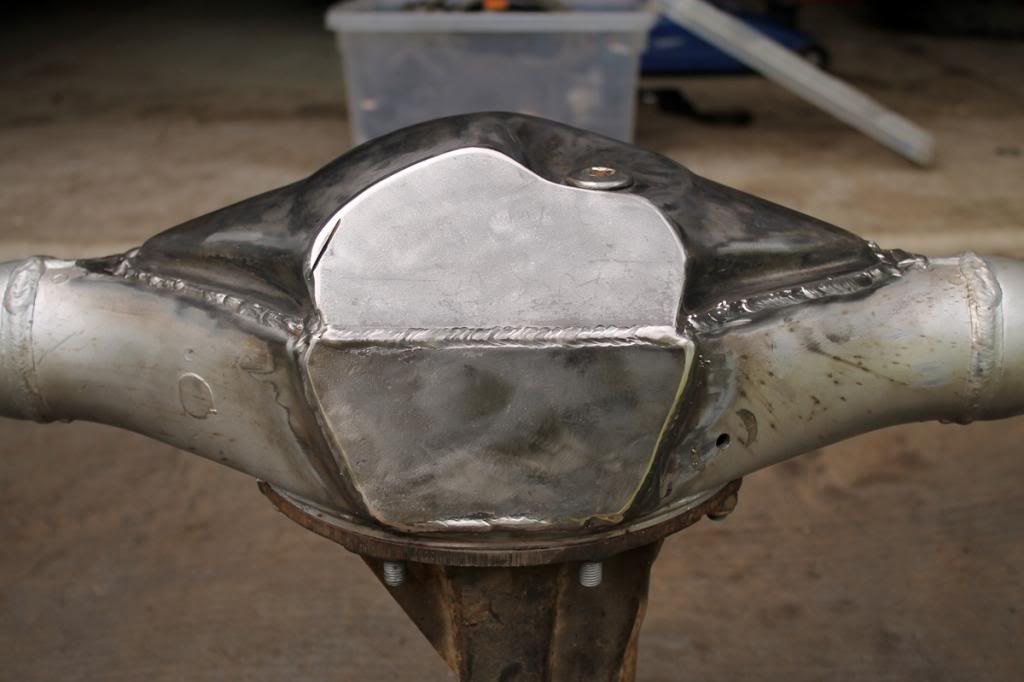
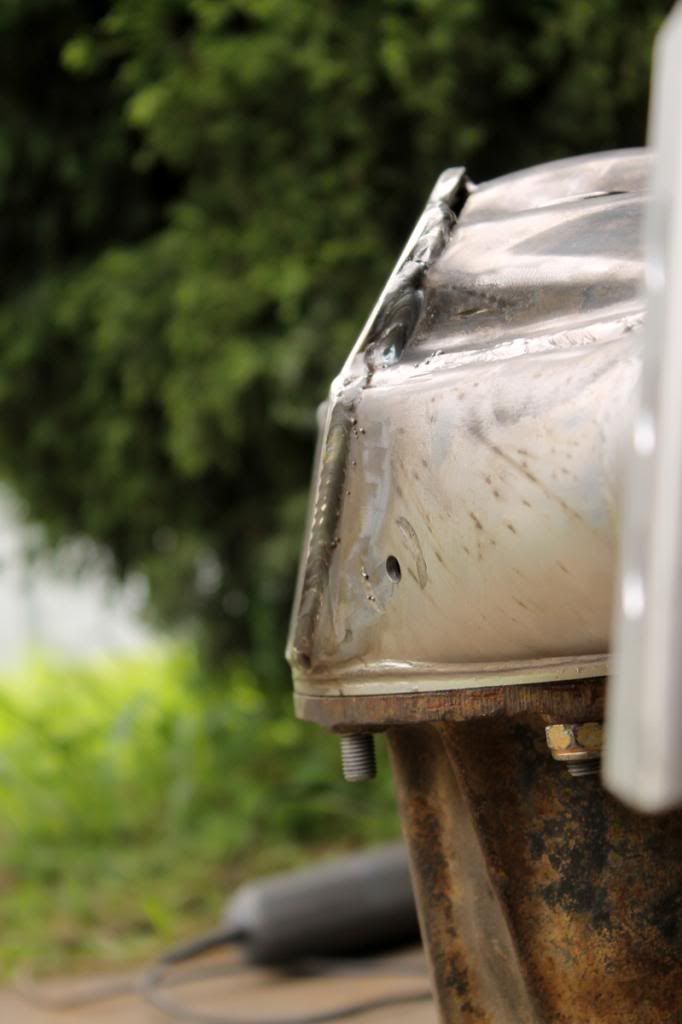
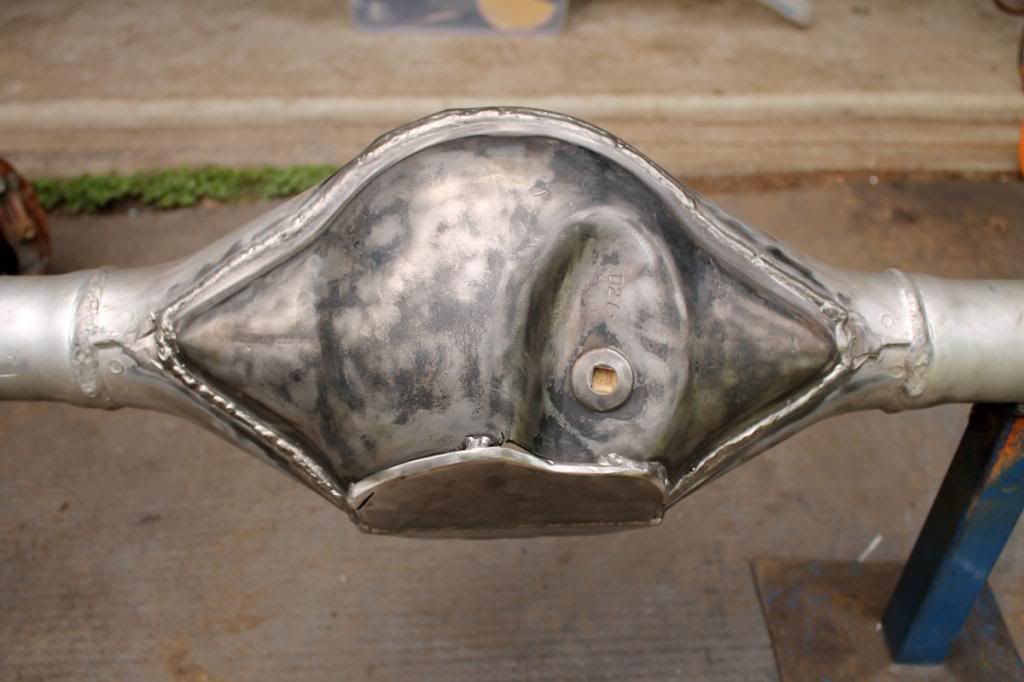
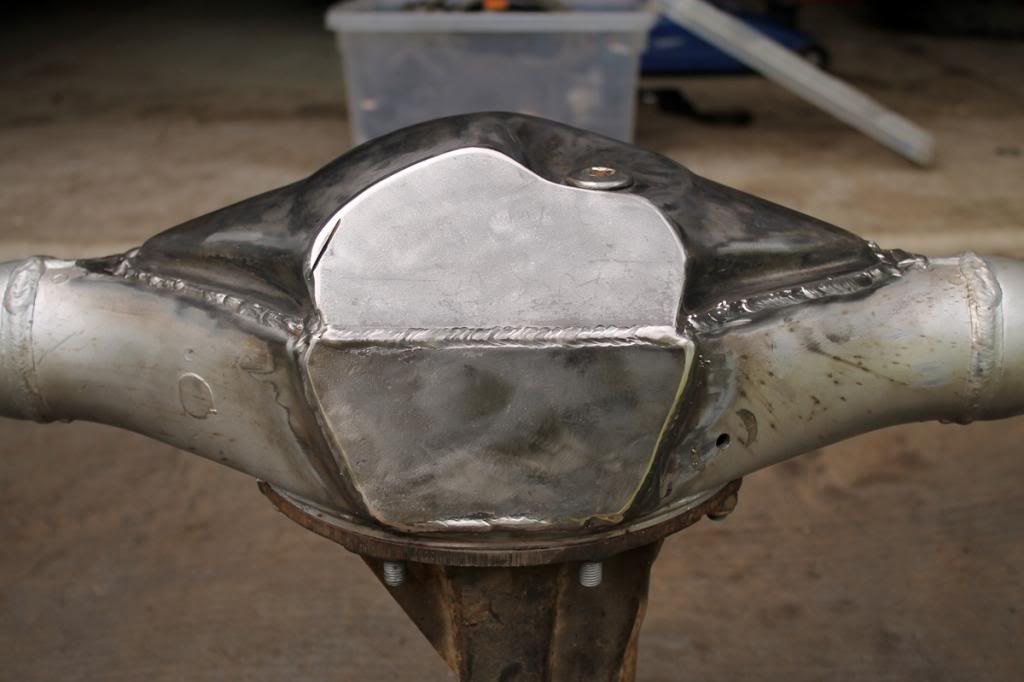
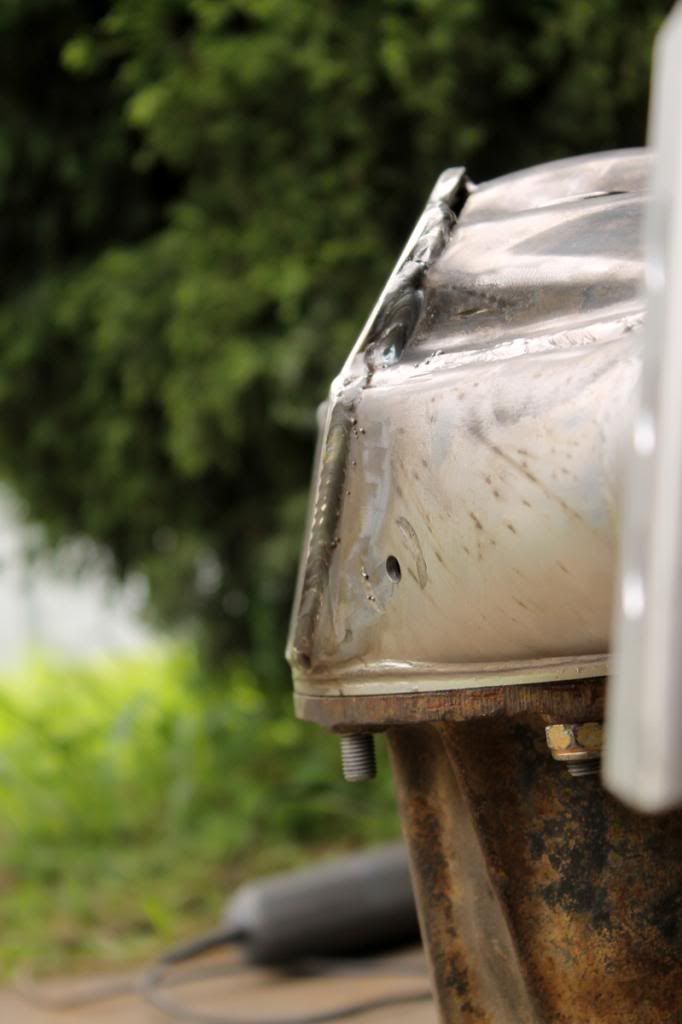
Re: The Welding Thread
Ok looking for advice on some acdc tig welders. What to get and what not to get. Looking at spending around $1500. Would love to get a Kemppi but can't justify the cost. So currently looking at the following.
http://www.ebay.com.au/itm/Cigweld-Weld ... uhb=1#shId" onclick="window.open(this.href);return false;
http://www.ebay.com.au/itm/UNITIG-ACDC- ... e01&_uhb=1" onclick="window.open(this.href);return false;
What do you think or is there something else I should be looking at.
http://www.ebay.com.au/itm/Cigweld-Weld ... uhb=1#shId" onclick="window.open(this.href);return false;
http://www.ebay.com.au/itm/UNITIG-ACDC- ... e01&_uhb=1" onclick="window.open(this.href);return false;
What do you think or is there something else I should be looking at.
home brew cooling in progress
Posts: 3725
Joined: Wed Jun 30, 2004 1:45 pm
Joined: Wed Jun 30, 2004 1:45 pm
Location: Blue Mountains, or on a rig somewhere in bumf*ck idaho
Re: The Welding Thread
I think that little cigweld is great value considering the features on it. I won't touch unitig/unimig stuff at all after using my mate's MIG. They use proprietary parts that are a prick to get.
M
M
http://www.populationparty.org.au/
Re: The Welding Thread
I bought this, this afternoon under recommendation from people who would have an idea.
Hopefullly it does the job!

Hopefullly it does the job!

Posts: 689
Joined: Sat Oct 09, 2010 5:12 pm
Joined: Sat Oct 09, 2010 5:12 pm
Location: SMUGGLING COOOOOKIES ACROSS THE MEXICAN BORDER
Re: The Welding Thread
chook you should start your own thread
that way when you post up all your photos.. in the future they'll be in the one topic than all over the forum..
and we can see the progress..
and years later you can show your kids when that happens.
that way they're all in the one spot
and you don't have to wonder where all your posts went on your builds.
and you can use them for future job interviews.
as you just log in and jump to your thread and give the employer something to visualise than just a resume
that will be a huge plus, than just a resume.. it would make it interactive.. of sorts..
very professional, and only help in your future career prospects
makes you one step ahead of every other trady.. around
I should do it too..
but I like my work, keep it a little private on my jobs that I do.
just saying

that way when you post up all your photos.. in the future they'll be in the one topic than all over the forum..
and we can see the progress..
and years later you can show your kids when that happens.

that way they're all in the one spot
and you don't have to wonder where all your posts went on your builds.
and you can use them for future job interviews.
as you just log in and jump to your thread and give the employer something to visualise than just a resume

that will be a huge plus, than just a resume.. it would make it interactive.. of sorts..
very professional, and only help in your future career prospects

makes you one step ahead of every other trady.. around
I should do it too..

but I like my work, keep it a little private on my jobs that I do.
just saying

AUSTRALIA
WORTH LOOKING AT WORTH LOOKING AFTER
WORTH LOOKING AT WORTH LOOKING AFTER
Re: The Welding Thread
It really is a GREAT machine that 1.SierraDan wrote:I bought this, this afternoon under recommendation from people who would have an idea.
Hopefullly it does the job!
Re: The Welding Thread
what did that set you back Dan? If you don't mind me asking.
Re: The Welding Thread
I know it's not really 'welding' but what's a good plasma cutter out there?
Re: The Welding Thread
Hypertherm
Re: The Welding Thread
$895 at Gasweldsht50 wrote:what did that set you back Dan? If you don't mind me asking.
Re: The Welding Thread
How'd I do?
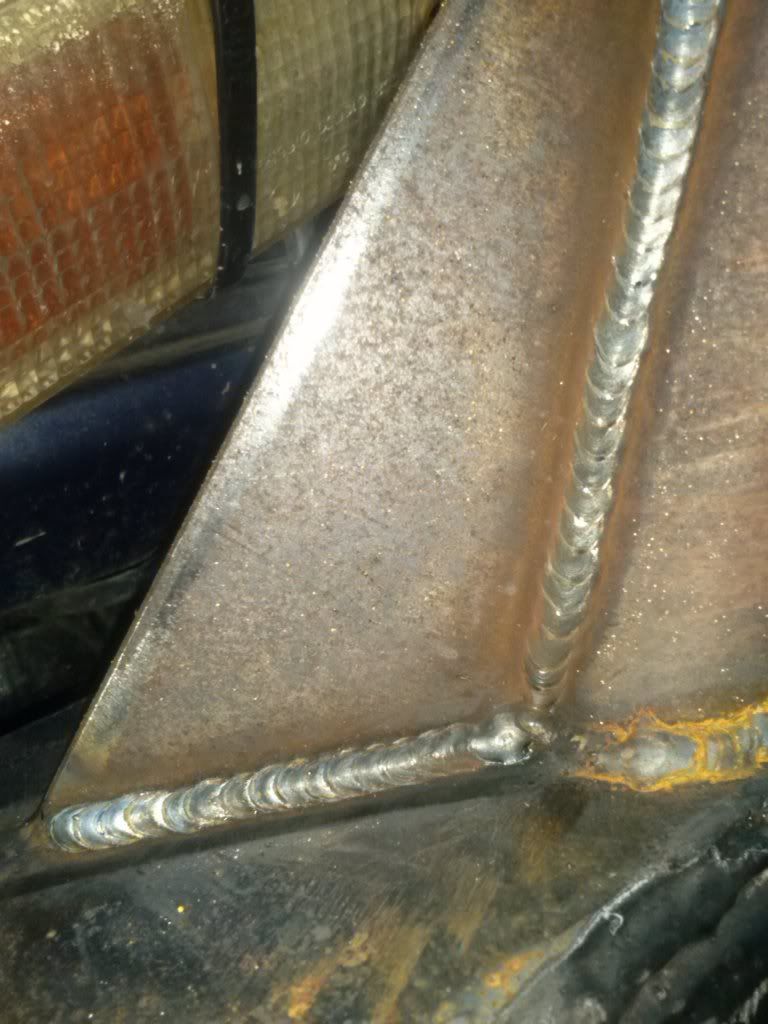
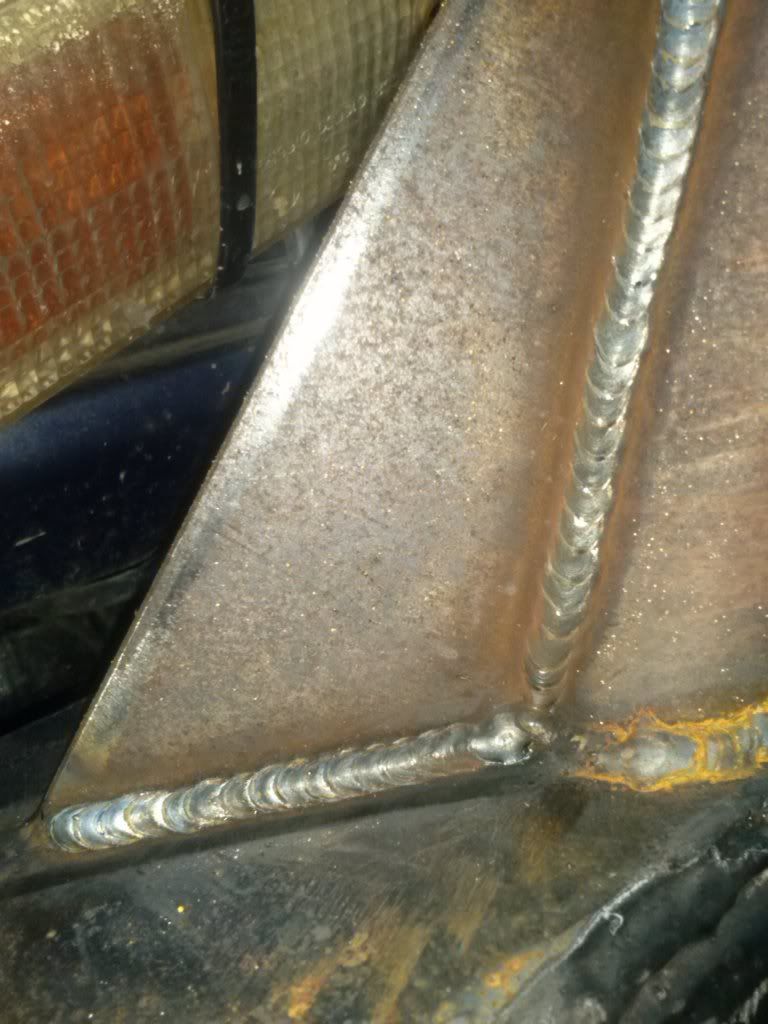
Posts: 689
Joined: Sat Oct 09, 2010 5:12 pm
Joined: Sat Oct 09, 2010 5:12 pm
Location: SMUGGLING COOOOOKIES ACROSS THE MEXICAN BORDER
Re: The Welding Thread
bottom pick needed a touch more wire, doing that will add a bit of reinforcement to the weld.
you don't want a concave look, the effective throat thickness is massively reduced and gives you no reinforcement on the weld.
looks a little under filled and some undercut.
top pick looks ok, but generally a flick technique isn't used in the trade.
only with gal to burn off the zinc and kind of preps the area for weld.. as you weld.
a general smooth motion is better than a flick technique.
you don't want a concave look, the effective throat thickness is massively reduced and gives you no reinforcement on the weld.
looks a little under filled and some undercut.
top pick looks ok, but generally a flick technique isn't used in the trade.
only with gal to burn off the zinc and kind of preps the area for weld.. as you weld.
a general smooth motion is better than a flick technique.
AUSTRALIA
WORTH LOOKING AT WORTH LOOKING AFTER
WORTH LOOKING AT WORTH LOOKING AFTER
Posts: 689
Joined: Sat Oct 09, 2010 5:12 pm
Joined: Sat Oct 09, 2010 5:12 pm
Location: SMUGGLING COOOOOKIES ACROSS THE MEXICAN BORDER
Re: The Welding Thread
damn double posts 
PUSH WITH A MIG
PULL WITH A STICK
the control for the wire, A knob, dial is the AMPS
the controls, usually switches are your VOLTS
too many volts will give you a line in the middle of your weld.
when this happens you need to turn the welder down VOLTS.

PUSH WITH A MIG
PULL WITH A STICK
the control for the wire, A knob, dial is the AMPS
the controls, usually switches are your VOLTS
too many volts will give you a line in the middle of your weld.
when this happens you need to turn the welder down VOLTS.
Last edited by CRUZAAMAD on Sat Aug 03, 2013 6:34 pm, edited 2 times in total.
AUSTRALIA
WORTH LOOKING AT WORTH LOOKING AFTER
WORTH LOOKING AT WORTH LOOKING AFTER
Re: The Welding Thread
Yeah it does need a bit more wire after having a look haha thanks.
I push, i think
Right to left with the torch with the angle pointing more to the left.
My Lincoln has very basic variable controls. I know which is which. Its just knowing when and where to change one or the other i'm getting a grip on slowly.
I've been taught the basics by a pretty talented welder and am generally happy with the flick.
I push, i think
Right to left with the torch with the angle pointing more to the left.
My Lincoln has very basic variable controls. I know which is which. Its just knowing when and where to change one or the other i'm getting a grip on slowly.
I've been taught the basics by a pretty talented welder and am generally happy with the flick.
Posts: 689
Joined: Sat Oct 09, 2010 5:12 pm
Joined: Sat Oct 09, 2010 5:12 pm
Location: SMUGGLING COOOOOKIES ACROSS THE MEXICAN BORDER
Re: The Welding Thread
don't weave.
do straight runs.
one down the centre, then next is to the left side of centre weld and same to right again.
weaving reduces penetration, wont give you the punch required and sprays the HAZ heat affected zone all over the show, meaning it will be a shallow penetration.
bit like sex, keep it in the same spot and she gets all wet.....punch it in deep
that's her sweet spot.
welding is the same. get the metal all nice and hot is the deal.
downhand, weaving Is a no no.
it looked like you pulled it.
you got remember a weld is like a river, no point having steep banks, you've got to help the weld pool out..
the bottom should be a U,.... or V is okay, but with a V you have issues if its too sharp and the welder cant punch into it, and once that happens, it will flow on to the rest of the weld.
do straight runs.
one down the centre, then next is to the left side of centre weld and same to right again.
weaving reduces penetration, wont give you the punch required and sprays the HAZ heat affected zone all over the show, meaning it will be a shallow penetration.
bit like sex, keep it in the same spot and she gets all wet.....punch it in deep


welding is the same. get the metal all nice and hot is the deal.
downhand, weaving Is a no no.
it looked like you pulled it.
you got remember a weld is like a river, no point having steep banks, you've got to help the weld pool out..
the bottom should be a U,.... or V is okay, but with a V you have issues if its too sharp and the welder cant punch into it, and once that happens, it will flow on to the rest of the weld.
AUSTRALIA
WORTH LOOKING AT WORTH LOOKING AFTER
WORTH LOOKING AT WORTH LOOKING AFTER
Re: The Welding Thread
Sorry, i had trouble learning much from that haha..
I understood, get it hot and it looked like i pulled.
I understood, get it hot and it looked like i pulled.
Who is online
Users browsing this forum: No registered users and 1 guest