Page 2 of 4
Posted: Wed Aug 06, 2008 3:52 pm
by jet-6
Ive seen some rough unsafe jobs, but that is right up there!!!!!
Posted: Wed Aug 06, 2008 3:53 pm
by phippsy
I liked the thread title the best "Bodgy Winch Install" at least he didn't lie...
Posted: Wed Aug 06, 2008 4:21 pm
by Guy
chimpboy wrote:Here is someone else's diagram:
That is how I've always understood it to work. The equal/opposite reaction concern you had is covered there as you can see.
oops ..In my head I didnt have the other end of the rope\winch attatched to the vehicle ..

Posted: Wed Aug 06, 2008 5:18 pm
by sierrajim
I wonder if all of these opinions are going to be condensed and written up as someone elses thoughts

Posted: Wed Aug 06, 2008 5:27 pm
by me3@neuralfibre.com
bru21 wrote:now that the template is made, a steel one should happen quickly
After it fails it'll become steel.
Like I said - tested the mount - hasn't broken yet, not even close.
I DO DOUBT the fairlead attachment, BUT, the failure modes for the fairlead mounting failing are not significant for me.
Further - as stated - for the fairlead to fail it would need to be a sideways pull. My bullbar mounts (fatory toyota) have VERY THIN sideways stiffeners, they would fail first.
Worst case the rivets will just pull through on one side, big deal.
FYI - aluminium is 2/3 the strength of steel, but 1/3 the weight. Therefore is has to be 50% thicker than steel to bear the same load, and it will weight 1/2 as much.
Paul
Posted: Wed Aug 06, 2008 5:31 pm
by Evil 73
Posted: Wed Aug 06, 2008 5:32 pm
by macca81
me3@neuralfibre.com wrote:
FYI - aluminium is 2/3 the strength of steel, but 1/3 the weight. Therefore is has to be 50% thicker than steel to bear the same load, and it will weight 1/2 as much.
Paul
nope, it has to be 33% thicker to bear the same load, and as a result will be 66% of the weight
Posted: Wed Aug 06, 2008 5:38 pm
by me3@neuralfibre.com
Evil 73 wrote:me3@neuralfibre.com wrote:I tried to make it fail.
Mount showed no permanent deformation
Care to guess at the strength of the feet on the winch (they are alloy)
But yes, it's an experiment.
Paul
Theses are generally in compression, they are not being pulled against in pretty much all the mounting ive seen over the years, they would defianteley snap if pulled in the other direction. As far as i see it have a look at the way the manufactures ARB,TJM etc mount the winches to the bars they are all in compression which then only leaves the bar itself to fail.
Ben
I thought the mount direction was commonly differnet for US vs Aus. They mount theirs flat, we mount the feet forward.
How is a hi-mount mounted?
Paul
Posted: Wed Aug 06, 2008 5:55 pm
by chimpboy
If we're comparing aluminium to steel, it's probably worth noting that aluminium's fatigue performance is less than 50% that of steel.
http://www.ussautomotive.com/auto/steel ... cfacts.htm
Obviously this is a pro-steel site so make of it what you will.
Posted: Wed Aug 06, 2008 6:13 pm
by Evil 73
Alloy bars are for trucks
http://tbn0.google.com/images?q=tbn:F9r ... inyone.com.
Or maybe you should get yourself one of these, i think it might suit your purpose.
http://www.beaututes.com/gallery/waterm ... 883&size=1
Posted: Wed Aug 06, 2008 6:25 pm
by shakes
me3@neuralfibre.com wrote:bru21 wrote:now that the template is made, a steel one should happen quickly
After it fails it'll become steel.
Like I said - tested the mount - hasn't broken yet, not even close.
Paul
AFTER! Man, after this thread and the "my diff was making noise but I thought it was normal" thread, your on the verge of driving through gravity.
alluminium doesnt fail like steel which will stretch and creak and groan and carry on and generally give a fair warning, it will fatigue and will fail in a major way with very minimal warning signs. I really hope it's only your car and ego that get hurt.
All for a weight saving of 30-40kg's max and $200 of fuel over 39,835km's?
Posted: Wed Aug 06, 2008 6:34 pm
by hulsty
I think you need to improve your basic design abit mate, it could be made to work with aluminium, would be very chunky with minimal weight saving over steel but it could be done.
One thing, i've circled in the picture where it will fail, those corners, even though slightly rounded are a GREAT spot for a stress riser to form from fatigue and begin cracking. As has been pointed out cyclic loads arent going to go the aluminium any favours.
The way the winch will twist in operation will push down on the bottom face of the PFC where i've circled, and the only bit of strength it had to resist this is now gone, all the strength to resist this moment was in the flange. For a start if you insist on cutting out the flange some stiffening ribs must be placed along the bottom to build up the lost strength.
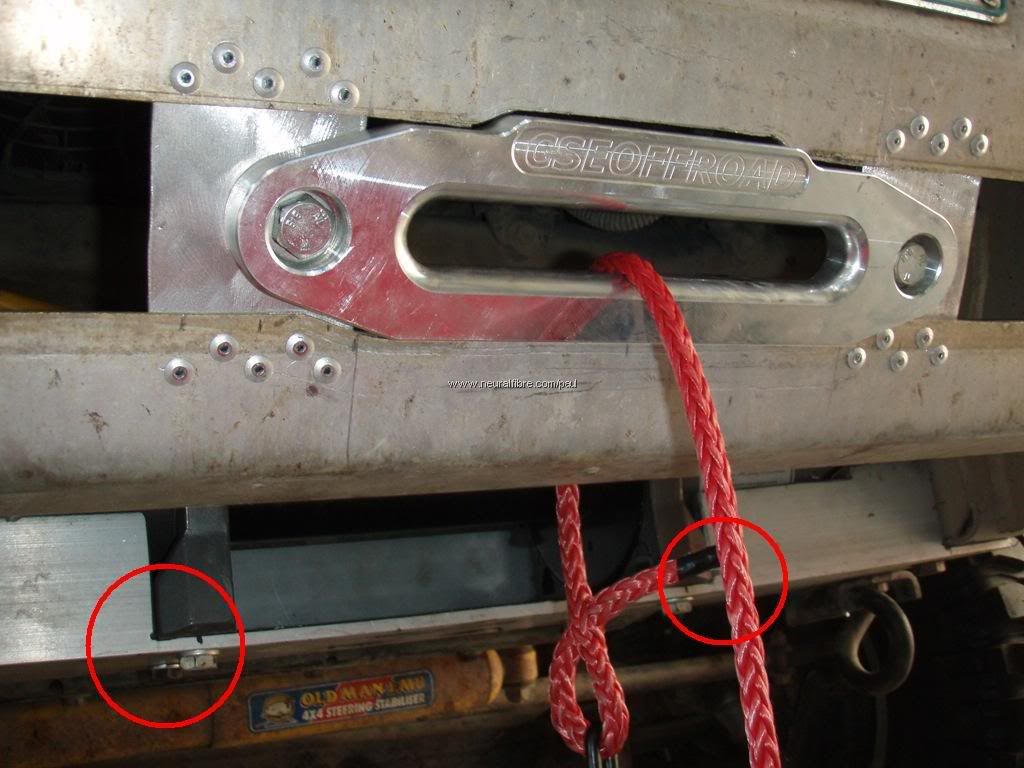
Posted: Wed Aug 06, 2008 6:42 pm
by hulsty
Just another thing, if you used a high strength hardened alumnium this will make your fatigue and cracking issues worse as it is not as tough, more brittle. I had a hardened aluminum accelerator cable mount fatigue and crack like this, it was 4mm thick and only had to fight against some light springs on the throttle body.
Posted: Wed Aug 06, 2008 6:46 pm
by chimpboy
Thing is, regardless of exact calculations you just can't look at that mount and not know in your gut that it isn't going to work. To me this is just from having seen a lot of different machines work and survive or work and break, over the years. As I said the rivets don't worry me as much as the "cradle", it just doesn't look like it can handle its likely future.
Posted: Wed Aug 06, 2008 7:34 pm
by me3@neuralfibre.com
http://neuralfibre.com/paul/4wd/winch-m ... aking-rope
Let the games continue.
Anyone in BNE care to suggest any other reasonable test - I'll see what I can do.
Paul
Posted: Thu Aug 07, 2008 8:54 am
by WICKED
Posted: Thu Aug 07, 2008 9:15 am
by sierrajim
Didn't Mr Dynamica hang his car from a crane?

Posted: Thu Aug 07, 2008 9:46 am
by smithie
sierrajim wrote:Didn't Mr Dynamica hang his car from a crane?

DO IT!! - just stand well clear!
Posted: Thu Aug 07, 2008 9:50 am
by giantracing
yeah great ............. its all fun until someone get hurts.
Posted: Thu Aug 07, 2008 9:52 am
by benhl
me3@neuralfibre.com wrote:
It if breaks, it breaks
If you're winching you're already in a world of sh1t - what you you think is going to happen when it goes BANG!
Posted: Thu Aug 07, 2008 10:03 am
by Gwagensteve
I don't think it will go bang, I think it will fall apart over time. I'm not aware of an alloy bar maker than hangs a winch off the bar - they all use some kind of steel cradle, and I vote it's due to the fatigue properties of aluminium.
I'd say if you can see visible flexing of the cradle under high load, it's not going to last.
Giving it a few hard pulls is going to be NOTHING like the fatigue caused by 2 years of normal driving.
Steve.
Posted: Thu Aug 07, 2008 10:09 am
by bazzle
It twisted but went back to shape..
Be aware that when it twists drum on winch goes out of alignment and could damage drive mech and braces, resulting in winch failure (just when danger is ats its max.
Make a mount from steel same size min.
Bazzle
Posted: Thu Aug 07, 2008 10:15 am
by me3@neuralfibre.com
Gwagensteve wrote:I don't think it will go bang, I think it will fall apart over time. I'm not aware of an alloy bar maker than hangs a winch off the bar - they all use some kind of steel cradle, and I vote it's due to the fatigue properties of aluminium.
I'd say if you can see visible flexing of the cradle under high load, it's not going to last.
Giving it a few hard pulls is going to be NOTHING like the fatigue caused by 2 years of normal driving.
Steve.
Hmm, - that's interesting.
Load from winching - lets say 4000kg @ 50 repetitions for it's life (prob not that many). 4000 kg produces stress, but no strain (permanent) deformation.
Winch + Rope + Cradle weighs say 25KG. Assume 3G acceleration worst case in any direction = 75KG
75KG at say 100,000 cycles. vs 4000KG @ 50 cycles.
I reckon it'll not bother it.
Chassis twisting is normal offroad, but not onroad. That will twist it up a bit.
There is no harmonic / spring vibration in the system. It is mounted at both ends, so shaking is unliekly to be an issue.
We'll have to see, but I would be that "driving" stress won't be significant.
FYI: It's done 12,000km, 4 offroad trips and 4 real recoveries so far, none particularly hard (rocks / hills as opposed to bogged to the chassis).
Re. the twisting - everything flexes, that's normal. Ever looked at a chassis under load? Or a bullbar when winching (watch the panel gaps)?
Paul
Posted: Thu Aug 07, 2008 10:24 am
by Gwagensteve
No, I'm sorry, I think you're misunderstanding the different properties of steel Vs aluminium.
There's a very small window between elastic and plastic deformation in aluminium compared to steel.
Additionally, a high number of cycles at low load can propogate fatigue in aluminium. That's just he nature of aluminium. It would be interesting to FEA your mount- those sharp corners on the cutouts are massive, massive stress raisers. Iwouldn't design a mount like that in steel, let alone in a high strength aluminium alloy.
steve.
Posted: Thu Aug 07, 2008 12:04 pm
by Guy
I would have thought that you woudl be better off making a mount for the winch off the chassis.. you could sit it further back and only have the fairlead on the bullbar. what does an standard winch mount weigh ? or if you wanted to go really light want does a PTO weigh compared to an electric ?
Posted: Thu Aug 07, 2008 12:37 pm
by Evil 73
Me3,
Are you responsable for this too??????
Maybe have a little read of this before the next attempt..........
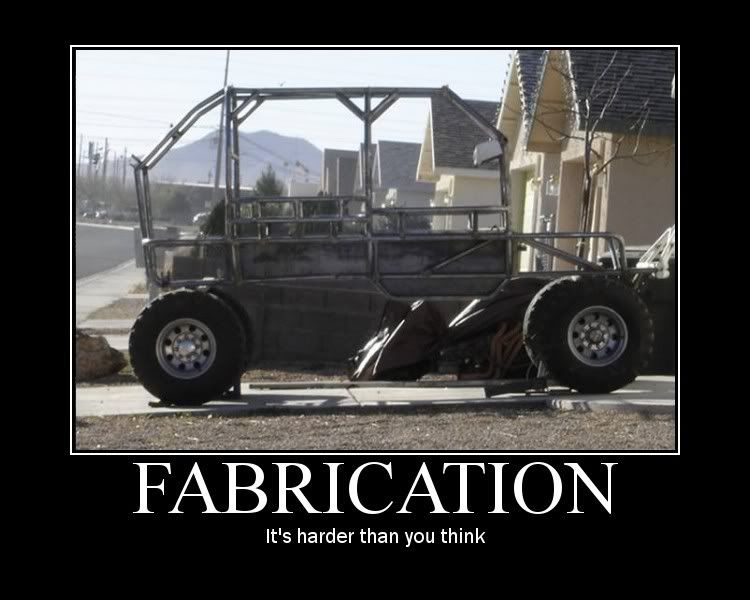
Posted: Thu Aug 07, 2008 12:54 pm
by me3@neuralfibre.com
love_mud wrote:I would have thought that you woudl be better off making a mount for the winch off the chassis.. you could sit it further back and only have the fairlead on the bullbar. what does an standard winch mount weigh ? or if you wanted to go really light want does a PTO weigh compared to an electric ?
It is directly on the chassis w/ the fairlead on the bullbar.
Paul
Posted: Thu Aug 07, 2008 3:51 pm
by hulsty
whats the breaking force of the rope your using ?
Posted: Thu Aug 07, 2008 3:55 pm
by me3@neuralfibre.com
hulsty wrote:whats the breaking force of the rope your using ?
13,700lb - links to manufacturers and assemblers are in articles.
Paul
Posted: Thu Aug 07, 2008 4:04 pm
by hulsty
No wonder it broke then!! According to whats set out in the Australian standards for fibre ropes used in arduous conditions the SWL for your rope is only 690kg!!