Page 3 of 20
Posted: Mon Jul 07, 2008 9:56 pm
by MightyMouse
Nice job Matt.
Out of curiosity is there a reason why your splitting the water flow so evenly ?
As I understand it, the efficiency of a heat exchanger is greater with smaller differences in temperature between the charge and coolant. If the coolest water was fed to the engine side cores ( where the charge has been already partly cooled ) and then to the outside where the charge is hottest the relative charge/coolant temperature difference would be smaller and therefore more efficient overall.
Possible I've got it screwed up - but I don't think so......
Posted: Mon Jul 07, 2008 10:04 pm
by Shadow
MightyMouse wrote:Nice job Matt.
Out of curiosity is there a reason why your splitting the water flow so evenly ?
As I understand it, the efficiency of a heat exchanger is greater with smaller differences in temperature between the charge and coolant. If the coolest water was fed to the engine side cores ( where the charge has been already partly cooled ) and then to the outside where the charge is hottest the relative charge/coolant temperature difference would be smaller and therefore more efficient overall.
Possible I've got it screwed up - but I don't think so......
the rise in temp of the water across the core length is going to be insignificant at the flow rate of 20lt/min
Posted: Mon Jul 07, 2008 10:07 pm
by -Scott-
I had expected a double flow path - cool water through the downstream cores, then send the warm water through the upstream cores. Water flow too inefficient?
Posted: Mon Jul 07, 2008 10:12 pm
by matt.mcinnes
MightyMouse wrote:Nice job Matt.
Out of curiosity is there a reason why your splitting the water flow so evenly ?
As I understand it, the efficiency of a heat exchanger is greater with smaller differences in temperature between the charge and coolant. If the coolest water was fed to the engine side cores ( where the charge has been already partly cooled ) and then to the outside where the charge is hottest the relative charge/coolant temperature difference would be smaller and therefore more efficient overall.
Possible I've got it screwed up - but I don't think so......
I thought it was the other way around and that the bigger the difference in temp the better the heat exchange rate.
The other point is their are no engine side cores, the charged air is divided equally into 4. A quater passing through each core, as is the water. This keeps everything equal.
Posted: Mon Jul 07, 2008 10:32 pm
by matt.mcinnes
Each of these tiny cores drops +50c out of my charged air in my 2F-ETI, I need a minimum of 3 for volume 4 been ideal.
Calculate the surface area of an 80mm throtle body, then calculate the surface area of the slots in the tubes (one side only). The cores are approx 50/50 Air/Ali so therefor half the surface area of the slots
How many slots/cores do you need to equal your intake.
Posted: Mon Jul 07, 2008 10:55 pm
by ISUZUROVER
matt.mcinnes wrote:The cores are designed with a flow path over the fins for maximum efficiency. Laminova have designed an extruded housing for these, or as in some application such as BMW M3 supercharger kit, they are built into the inlet manifold as an integral part.
Scaffold tube just happens to be a perfect size for our application the 15mm slot as mentioned above is recommended on the Laminova site, I think the have done some extensive testing to come to this so I went with it
The one thing we have done that I have not seen any where else apart from a custom one in a Lotus Elise application is to run the water in parallel, although the Elise was only running 3 cores. The gains running in parallel as far as I can see are huge as each core runs at maximum efficiency, the down side is the amount of water each core requires 20Lt per min minimum. So the pump has to be much larger.
Looks great, but I can't see why you need the tubes over each core. If you mount the cores so that the fins sit between each other slightly (as if you have the fingers of each hand locked together slightly - hope that makes sense?) - then the air/fin contact time will be the same, and the pressure drop should be slightly lower.
The only concern I have with the Laminova system (on a diesel) is what would happen if on e of the cores springs a leak!!! What is the wall thickness of the main tube???
Posted: Mon Jul 07, 2008 11:19 pm
by matt.mcinnes
You will not brake one of these. Even Laminova describe them as bullet proof and I would have to agree.
The tubes force the air around the core without them you can not control the air flow over the circumferance of the core. If you removed the tubes you would be unable to conrol where the air would enter and exit the core, it would take the easiest and shortest route.
Posted: Mon Jul 07, 2008 11:28 pm
by ISUZUROVER
I know they look reasonably thick where it counts - but thicker alloy heads have corroded through during their life.
I understand your point about forcing the airflow, but I still think there is a better way...
Posted: Mon Jul 07, 2008 11:35 pm
by matt.mcinnes
ISUZUROVER wrote:I know they look reasonably thick where it counts - but thicker alloy heads have corroded through during their life.
I understand your point about forcing the airflow, but I still think there is a better way...
I have to disagree Laminova have designed these cores to be contained in this very manor to get the best out of them.
The cores are easy to remove service/check for corrosion and re install.
Posted: Tue Jul 08, 2008 12:35 am
by ISUZUROVER
matt.mcinnes wrote:ISUZUROVER wrote:I know they look reasonably thick where it counts - but thicker alloy heads have corroded through during their life.
I understand your point about forcing the airflow, but I still think there is a better way...
I have to disagree Laminova have designed these cores to be contained in this very manor to get the best out of them.
The cores are easy to remove service/check for corrosion and re install.
Fair enough. How can the cores be removed??? How do they located in the housing so as to be leak-proof?
Posted: Tue Jul 08, 2008 5:59 am
by KiwiBacon
ISUZUROVER wrote:I know they look reasonably thick where it counts - but thicker alloy heads have corroded through during their life.
I understand your point about forcing the airflow, but I still think there is a better way...
Have you got any CFD software?
Posted: Tue Jul 08, 2008 6:18 am
by Shadow
ISUZUROVER wrote:matt.mcinnes wrote:ISUZUROVER wrote:I know they look reasonably thick where it counts - but thicker alloy heads have corroded through during their life.
I understand your point about forcing the airflow, but I still think there is a better way...
I have to disagree Laminova have designed these cores to be contained in this very manor to get the best out of them.
The cores are easy to remove service/check for corrosion and re install.
Fair enough. How can the cores be removed??? How do they located in the housing so as to be leak-proof?
in the PDF it gives some ideas of mounting methods, i think its up to the person designing the box for the cores to ensure they are adequately mechanically fixed and removable etc.
The leak proof is taken care of using rubber o-ring at both ends.
I thinkt he mechanical
Posted: Tue Jul 08, 2008 8:25 am
by matt.mcinnes
ISUZUROVER wrote:matt.mcinnes wrote:ISUZUROVER wrote:I know they look reasonably thick where it counts - but thicker alloy heads have corroded through during their life.
I understand your point about forcing the airflow, but I still think there is a better way...
I have to disagree Laminova have designed these cores to be contained in this very manor to get the best out of them.
The cores are easy to remove service/check for corrosion and re install.
Fair enough. How can the cores be removed??? How do they located in the housing so as to be leak-proof?
To remove the cores all you need do is drain the coolant and unscrew the end caps and slide them out, it's that easy.
They are sealed in the housing as stated above using an O-Ring, but even if one of these was to fail the water would have to pass between a gap of 0.05mm to leak into the actual housing, if you machine your tolerances well. Also I believe O-Rings rarely have a catastrophic failure if fitted correctly. I think you have more chance of your cylinder head gasket failing.
Vibration is the biggest killer so we have mounted mine on 4 rubber mounts, this will be applied to all our intercoolers.
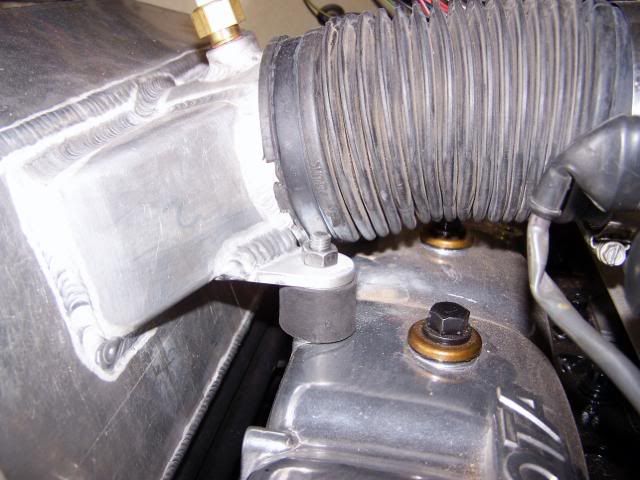
Posted: Tue Jul 08, 2008 10:34 am
by matt.mcinnes
bogged wrote:Is there an ideal size V engine size? or "one size fits all"??
so if you made largeer tubes, would it work better?
Here you go Bogged a link to the various sizes.
http://www.laminova-online.se/Front/Pag ... spx?cid=78
We are using the 392mm cores
Prices are available too on this web site, but don't fall over when it comes up +$200US each
Ebay you can find them for as little as $100US for 4 plus shipping but at the moment all of these have been bought up

Posted: Tue Jul 08, 2008 10:43 am
by 1MadEngineer
This is a graph from the SCADA data log system whilst we were doing heat lab testing at ACART/ford.
The test involved doing back to back dyno runs at 40 degree ambient air temp.
I am surprised at the cost of the laminova cores, i thought they were a little cheaper. The CAC main cores we used for this project are quite simple to make (if you have the brains and patience) we costed the main core unit at ~$600 then add end tanks to suit each specific application.
Posted: Tue Jul 08, 2008 11:16 am
by matt.mcinnes
Curious to know how your intake temp can drop below 40C ambient?
As show in your graph
This should remain constant in the hot box?
Posted: Tue Jul 08, 2008 11:23 am
by KiwiBacon
matt.mcinnes wrote:Curious to know how your intake temp can drop below 40C ambient?
You could do it with a throttle mostly shut.
Of course if you're running a throttle mostly shut you don't need boost or an intercooler.
Posted: Tue Jul 08, 2008 11:24 am
by 1MadEngineer
matt.mcinnes wrote:Curious to know how your intake temp can drop below 40C ambient?
ambient air flow is measured inside the air box (as well as externally) but typically as the air flow increases 'heat' is asorbed into the air stream - natural convection!
Posted: Tue Jul 08, 2008 11:39 am
by matt.mcinnes
1MadEngineer wrote:matt.mcinnes wrote:Curious to know how your intake temp can drop below 40C ambient?
ambient air flow is measured inside the air box (as well as externally) but typically as the air flow increases 'heat' is asorbed into the air stream - natural convection!
If the test is done 40C ambient and the vehicle is up to normal operating temp I don't see where you can exchange the heat. I certainly can't drop air temp under my bonnet below ambient without external help.
The graph shows around a +10C drop.
Posted: Tue Jul 08, 2008 12:03 pm
by 1MadEngineer
matt.mcinnes wrote:1MadEngineer wrote:matt.mcinnes wrote:Curious to know how your intake temp can drop below 40C ambient?
ambient air flow is measured inside the air box (as well as externally) but typically as the air flow increases 'heat' is asorbed into the air stream - natural convection!
If the test is done 40C ambient and the vehicle is up to normal operating temp I don't see where you can exchange the heat. I certainly can't drop air temp under my bonnet below ambient without external help.
The graph shows around a +10C drop.
tests are done inside the ACART hot cell (basically a dyno lab that can heat/cool from -5deg to 55deg ambient).
http://www.acart.com.au/emissions.html
Climatic Petrol EmissionsTest Cell 3
Temperature range between -30°C and +55°C
AVL Zoellner 48" 300kW Four Wheel Drive Dynamometer (as above)
Horiba EURO IV-capable emissions benches and CVS
there is some tricky engineering involved to get the radiators to be so effecient!

Posted: Tue Jul 08, 2008 12:08 pm
by matt.mcinnes
Still does not explain how you get so far below ambient you are stating on the intake sensor.
Lets have some photos of the cores and set up se we can better understand.
Posted: Tue Jul 08, 2008 12:19 pm
by Guy
matt.mcinnes wrote:Still does not explain how you get so far below ambient you are stating on the intake sensor.
Lets have some photos of the cores and set up se we can better understand.
The only thing I can think of is the air expanding a little as it passes out of the intake ducting. Doubt it would be 10 degree difference though.
Posted: Tue Jul 08, 2008 12:26 pm
by matt.mcinnes
Studying the graph to me it look like Ambient is mid-low 20's under the bonnet high 30's.
Getting on the power draws the cooler air through from outside the bonnet faster having less time to heat under the bonnet showing in a temp drop as you get on the power. The rest makes sense from there to me.
Posted: Tue Jul 08, 2008 12:26 pm
by KiwiBacon
1MadEngineer wrote:
tests are done inside the ACART hot cell (basically a dyno lab that can heat/cool from -5deg to 55deg ambient).
http://www.acart.com.au/emissions.html
Climatic Petrol EmissionsTest Cell 3
Temperature range between -30°C and +55°C
AVL Zoellner 48" 300kW Four Wheel Drive Dynamometer (as above)
Horiba EURO IV-capable emissions benches and CVS
there is some tricky engineering involved to get the radiators to be so effecient!

Still nothing to explain the possible violation of the 3rd law.
Is the engine intake at ambient or below?
Are you using refrigeration anywhere in this system?
Is the test cell incapable of heating air as fast as the engine is drawing it in?
Posted: Tue Jul 08, 2008 12:55 pm
by ISUZUROVER
KiwiBacon wrote:ISUZUROVER wrote:I know they look reasonably thick where it counts - but thicker alloy heads have corroded through during their life.
I understand your point about forcing the airflow, but I still think there is a better way...
Have you got any CFD software?
Yep - Fuent. I don't suppose you want to draw up some geometries in CAD so I can import them into Gambit (Fluent meshing/drawing system).
Matt - looks very nicely made. I wasn't concerned about 0-rings leaking - more the cores corroding/eroding over a long term. However being able to remove and check them every so often means that is probably very unlikely.
Posted: Tue Jul 08, 2008 1:40 pm
by KiwiBacon
ISUZUROVER wrote:
Yep - Fuent. I don't suppose you want to draw up some geometries in CAD so I can import them into Gambit (Fluent meshing/drawing system).
Not right now (too many clients pushing work at me) but maybe one day.
Posted: Tue Jul 08, 2008 2:27 pm
by ISUZUROVER
KiwiBacon wrote:ISUZUROVER wrote:
Yep - Fuent. I don't suppose you want to draw up some geometries in CAD so I can import them into Gambit (Fluent meshing/drawing system).
Not right now (too many clients pushing work at me) but maybe one day.
No worries - that is the exact same reason I don't do more CFD modelling...
Posted: Tue Jul 08, 2008 2:50 pm
by matt.mcinnes
Just a little more reading.
I supplied the tubes for this ongoing project which I'm watching with interest. It seems our Ozzie scaffold tube is unique even in Holland
http://www.locostbuilders.co.uk/viewthr ... 255&page=1
Posted: Tue Jul 08, 2008 8:40 pm
by -Scott-
love_mud wrote:matt.mcinnes wrote:Still does not explain how you get so far below ambient you are stating on the intake sensor.
Lets have some photos of the cores and set up se we can better understand.
The only thing I can think of is the air expanding a little as it passes out of the intake ducting. Doubt it would be 10 degree difference though.
Don't forget that your temperature variation is in Kelvin - it's 10 degrees in 300 or so, not 10 degrees in 30 or 40.
Posted: Tue Jul 08, 2008 9:06 pm
by matt.mcinnes
If any one wants to down load the Wolf V500 software which is free you can run the data log files from our testing of the intercooler. Some are quite large at 700sec.
http://www.wolfems.com/index.php/compon ... Itemid,48/
PM me if you want the files emailing out.