Page 1 of 1
opinions on this weld please
Posted: Tue Jun 05, 2007 3:45 pm
by Madmac
im getting ready to do my body chop and have been practising welding some thin stuff with the MIG, its only a little 160amp job and at the moment im using a disposable cylinder (argon/co2 mix) .6mm wire. im planning to rent a full size cylinder and buy a decnt regulator when i do the cut and shut. below is a pic of a butt weld ive just done on some .8mm sheet. what do you folks think, what can i do to improve it etc. it seems to have penetrated right through and i cant break it apart. im new to welding thin stuff.
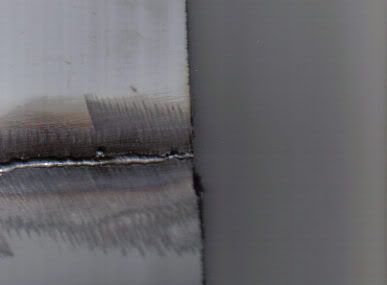
Posted: Tue Jun 05, 2007 5:24 pm
by DNA Off Road
Not too bad – they key here is practice, practice and practice. Your welding speed has varied a bit over the length of the weld. Try and maintain a constant speed [moving the torch that is not wire feed speed] to keep the weld pool the same size and shape. I’d be aiming to replicate the first few mm you can see in your image.
Cheers
Posted: Tue Jun 05, 2007 5:51 pm
by Shadow
i think they tend to overlap as opposed to butt weld dont they?
looks good to me, but i have not had much success welding thin stuff, but ive only got a stick :S
Posted: Tue Jun 05, 2007 6:24 pm
by Madmac
Shadow wrote:i think they tend to overlap as opposed to butt weld dont they?
looks good to me, but i have not had much success welding thin stuff, but ive only got a stick :S
yeah im going to overlap when i do the body chop, ill be practising some overlap type welds too
Posted: Tue Jun 05, 2007 6:55 pm
by CWBYUP
What sort of welder are you using ?
Only reason I ask is that the little mig i use is a pain in arse to use as it dosent have enough settings.
The UniMig 240 that i had a trial on the other day seem to to be alot more user friendly as it has more adjustment which are in smaller increments.
If that makes sense.
Nick
Posted: Tue Jun 05, 2007 9:07 pm
by CWBYUP
Also if you are going to lip the join are you going to step them ?
You should be able to get a spot holer / stepper ( air operated ) for about $200- for a good one.
It will give you a lot better finished product and easier to weld.
Cheers Nick
Posted: Tue Jun 05, 2007 9:19 pm
by Nelso
A tip a panel beater told me once was to lightly tap the welded area with a ball-peen hammer while it's still hot, to push it in level with the rest of the panel to make it easier to finish off when painting. You could practice doing this while you are at the welding practice.
Posted: Tue Jun 05, 2007 9:44 pm
by cooter
if the panel gets too hot it will warp so you might have to do short stitches (2inch long welds) and move to the other end of the panel
Posted: Tue Jun 05, 2007 9:54 pm
by Braudy
One trick I've learnt with welding the thinner stuff is to be patient and weld a small section at a time to avoid warping. Ie : weld a bit , go do something else then come back to it. Better off taking longer at this stage than trying to fix warped panels later. Which sucks.
Posted: Tue Jun 05, 2007 10:31 pm
by Shadow
Nelso wrote:A tip a panel beater told me once was to lightly tap the welded area with a ball-peen hammer while it's still hot, to push it in level with the rest of the panel to make it easier to finish off when painting. You could practice doing this while you are at the welding practice.
yeh
or you could not be lazy and just grind the weld flat :S
Posted: Tue Jun 05, 2007 11:28 pm
by Madmac
CWBYUP wrote:Also if you are going to lip the join are you going to step them ?
You should be able to get a spot holer / stepper ( air operated ) for about $200- for a good one.
It will give you a lot better finished product and easier to weld.
Cheers Nick
ive just been to a club meeting, apparently one of our members owns the tool you are refering to, hopefully i can borrow it.
Posted: Tue Jun 05, 2007 11:29 pm
by Madmac
CWBYUP wrote:What sort of welder are you using ?
Only reason I ask is that the little mig i use is a pain in arse to use as it dosent have enough settings.
The UniMig 240 that i had a trial on the other day seem to to be alot more user friendly as it has more adjustment which are in smaller increments.
If that makes sense.
Nick
yeah that makes sense, the mig i have is a toolex 160amp, it only has 3 toggle switches to adjust the settings
Posted: Tue Jun 05, 2007 11:30 pm
by Madmac
thanks for all the tips folks
Posted: Tue Jun 05, 2007 11:43 pm
by OISTA
Also with the thin stuff, clamp a bit of 5mm ally bar behind the weld line. It acts as a heat sink and helps stop blowing holes. Make sure it is ally but , otherwise it may be a tad hard to get off

Posted: Tue Jun 05, 2007 11:49 pm
by Madmac
OISTA wrote:Also with the thin stuff, clamp a bit of 5mm ally bar behind the weld line. It acts as a heat sink and helps stop blowing holes. Make sure it is ally but , otherwise it may be a tad hard to get off

ive heard you can use copper for this purpose too, but i havent tried it. might be worth looking into it though. thanks for reply.
Posted: Wed Jun 06, 2007 12:53 am
by SBC400
i have found that copper tends to work a bit better but it can be hard to get hold of large chunks of copper so most of the time i just use ally i have had no probs filling in holes with a oxy and filler wire this way have'nt tried joining to panels together with oxy but but with the mig i just practised as much as i could then did it bit by bit allowing the area to cool compeletly before starting again
Posted: Wed Jun 06, 2007 10:02 am
by benhl
cooter wrote:if the panel gets too hot it will warp so you might have to do short stitches (2inch long welds) and move to the other end of the panel
The bloke (not I) who welded my tub bob did exactly this and utilised the ally bar in behind technique. He also had moi on hand with a sopping wet rag to douse each 2" weld immediately to avoide warping the panels. We were butt joining with 2" stiches and in some parts, due to the poor alignement of the cut had to bridge 4-5mm gaps (again the ally bar came in very handy here to lay a bead across). He did use a TIG and did an excellent job. Took a while but looks the good in the end.
He also does custom body work for Auto Salon cars so knew his sh1t well. He was able to shape panels wiht a combination of weld, grinding and water and ended up joining many little triangular cut pieces to form dished out shapes in behind the wheel arches!