Page 1 of 2
Can I weld to spring steel?
Posted: Wed Jul 30, 2008 6:11 pm
by GRPABT1
Hey guys/girls, I did a search and came up with 2737 useless threads so here goes.
I am nearly finished installing a 3/4 elliptic setup in my zook and all I have to do left is drill a hole and place a bolt through the elliptic springs to locate them. I attempted this today and even bought a new drill, some extra bits and cutting oil. After going through alot of bits and much swearing I am left very sore and still don't have a hole big enough to fit the desired bolt through the springs.
So I was wondering if I could just weld the spring in place? It will be on the very end of the elliptic spring away from the shackle end and won't be flexed near the weld. Basically it is just to stop the spring sliding back and forth so a couple of beads on the spring would do the trick. So will it be ok to weld it?
The green bits are about where I will be welding.
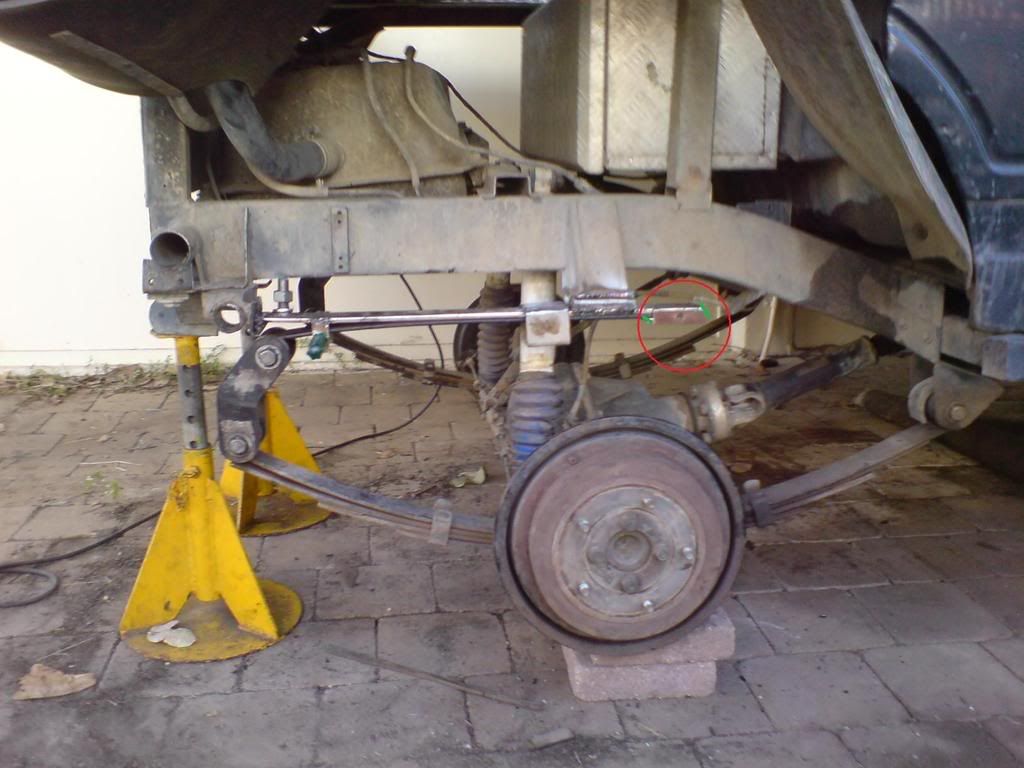
Posted: Wed Jul 30, 2008 6:19 pm
by ZookNC
mate, if you get your hands on some cobalt hardened drill bits, you'll drill through your springs no worries. Just get the size you need, they're usually sold by the unit. Not cheap but VERY MUCH worth it.
Cheers,
Posted: Wed Jul 30, 2008 6:21 pm
by GRPABT1
I have colbalt drill bits. I need another 1mm wider on the side you can see in the pic and about 4mm on the other side. Seriously I think it would be doable with a drill press but I'm just getting extremely frustrated and going nowhere fast atm.
Posted: Wed Jul 30, 2008 6:34 pm
by sambo
get a masonry bit and regrind the tip. I once drilled through a case hardened part of a diff centre doing this.
Posted: Wed Jul 30, 2008 6:59 pm
by GRPABT1
Umm sorry if this sounds offensive but are you bloody serious?! That just sounds very odd. How is a masonary bit any better than a cobalt HSS bit? Especially after my booty fab grind job on the tip?
Posted: Wed Jul 30, 2008 7:32 pm
by ssfabricator
are you running the drill flat out?
i drill a lot of stainless i know its not as hard as spring steel but if you run the drill flat out you fark the bit in no time
press as hard as you can and short bursts on the trigger
Posted: Wed Jul 30, 2008 7:34 pm
by GRPABT1
Yeah that's what I'm doing and it has got me thus far, I am also drilling through stainless and its the easy bit.
Anyway does anyone have an answer to my question of welding?
Posted: Wed Jul 30, 2008 7:35 pm
by ausyota
GRPABT1 wrote:Umm sorry if this sounds offensive but are you bloody serious?! That just sounds very odd. How is a masonary bit any better than a cobalt HSS bit? Especially after my booty fab grind job on the tip?
Yeah masonry bits are tungsten carbide tipped.
Posted: Wed Jul 30, 2008 7:48 pm
by GRPABT1
Is that all masonary bits? Including the one that came with my makita power drill? Also I only have a 4inch angle grinder so it would be pretty hard to grind it properly
Posted: Wed Jul 30, 2008 7:58 pm
by Eddy
yep!
won't pass roadworthy unless you're ticketed etc.
see if you can get some Strata 507 rods, best there is for welding springs IMHO
Posted: Wed Jul 30, 2008 8:04 pm
by droopypete
Eddy wrote:yep!
won't pass roadworthy unless you're ticketed etc.
He could get Chuck Norris to weld it and it still wouldn't pass a roadworthy.
Peter.
Posted: Wed Jul 30, 2008 8:04 pm
by Eddy
To drill into spring, drop the drill speed to 300 rpm max.
Grab oxy, and quickly cook a red hot spotwhere you wanna drill, quench in cold water and off ya go. use plenty of CRC or similar to lube and cool the bit.
good luck
Posted: Wed Jul 30, 2008 8:05 pm
by badger
if you were drilling flat out you have no chance now as you have heat hardened the hole.
either drill new holes like 25mm away or weld it .................... 3/4 eliptic is illegal anyways so who cares if it illegal
welding that bit of the spring wont cause any issues to the spring as its supported after that and shouldnt cause any more issues to the chassis than a new shackle mount but is definatly very very illegal and could well render the chaissis written off if transport wanted to be I'm gayer than aids!
Posted: Wed Jul 30, 2008 8:33 pm
by Slunnie
GRPABT1 wrote:Yeah that's what I'm doing and it has got me thus far, I am also drilling through stainless and its the easy bit.
Anyway does anyone have an answer to my question of welding?
If you weld the spring, the spring will crack. The spring is also heat treated, so if you heat the spring.... it will lose its temper and crack.
Posted: Wed Jul 30, 2008 8:39 pm
by GRPABT1
It won't be welded on the chassis, there is a plate welded to the bump stop bracket and shackle bracket so I havn't fawked the chassis. I will break out the welder tomorrow I think.
Thanks guys.
Posted: Wed Jul 30, 2008 8:40 pm
by GRPABT1
Slunnie wrote:GRPABT1 wrote:Yeah that's what I'm doing and it has got me thus far, I am also drilling through stainless and its the easy bit.
Anyway does anyone have an answer to my question of welding?
If you weld the spring, the spring will crack. The spring is also heat treated, so if you heat the spring.... it will lose its temper and crack.
If you read my original post and looked at the thread the part where it'll be welded will be supported and not flexing. Do you still think it will crack?
Posted: Wed Jul 30, 2008 8:45 pm
by badger
no it wont crack. the only reason it would crack is if the spring was to spring (move) where the weld is ................... it cant because of the u bolts
Posted: Wed Jul 30, 2008 8:46 pm
by MART
Yes it will still crack , more to the point it will probably snap of, I have used those gold tungsten coated drill bits to drill holes in springs , but you only get two holes per drill bit , either take it to a engineers shop or buy a cobalt drill. You will have created a hard spot in the spring , what size where you after anyway , Cheers Paul.
Posted: Wed Jul 30, 2008 8:57 pm
by GRPABT1
I used cobalt bits. I'm after an 8mm hole to fit a M8 bolt through to locate the pring. I have one hole to 7mm so I might just take the thread off a bolt and use it like a pin and weld a nut on the end. The other side is only about 4mm, what size bolt minimum would be good enough just to stop the forward and backward sliding movement? Bear in mind the spring WILL NOT FLEX WHERE THE HOLE IS and it is supported on all sides where the hole is tightly preventing any other range of movement.
Posted: Wed Jul 30, 2008 8:58 pm
by harlequin
spring steel is med to high carbon heat treated if you heat and quench it will harden changing the grain structure to martensite - extremely hard and brittle you can weld it with the correct rod maybe weldall or the other mentioned above you will need to preheat the area to be welded and maintain a post heat there are welding procedures to do this but rudimentary would be preheat to 200- 300 degrees C weld then reheat maintain heat for a period of time using thermal blankets wrapped around the area you need to obtain a gradual cooling rate this is a rough method you should really know the parent material composition precise preheat/ post heat temps and times to get a proper job grab a stick and whack some spoggy shit on er
Posted: Wed Jul 30, 2008 8:59 pm
by Slunnie
GRPABT1 wrote:Slunnie wrote:GRPABT1 wrote:Yeah that's what I'm doing and it has got me thus far, I am also drilling through stainless and its the easy bit.
Anyway does anyone have an answer to my question of welding?
If you weld the spring, the spring will crack. The spring is also heat treated, so if you heat the spring.... it will lose its temper and crack.
If you read my original post and looked at the thread the part where it'll be welded will be supported and not flexing. Do you still think it will crack?
I have no doubt it will crack.
If the spring is going to have any value (ie it will flex) then it will be levering against the welds, which will happen when you are getting drop travel beyond what the main spring pack provides, or if there is already load on it, which is what it looks like then already the forces are in there. Even if you run a clamp into the first spring guide, there will be flexing back at the welds though the deformation in the support which you have put in. It doesn't take an appreciable amount of movement to crack things, and chassis cracks are a great example of that. I highly doubt an engineer would approve a welded spring for the same reason.
weld
Posted: Wed Jul 30, 2008 9:01 pm
by MUD80D
Try using a die grinder they have worked for me in the past
just take it slow with a small bit
Posted: Wed Jul 30, 2008 9:02 pm
by GRPABT1
harlequin wrote:spring steel is med to high carbon heat treated if you heat and quench it will harden changing the grain structure to martensite - extremely hard and brittle you can weld it with the correct rod maybe weldall or the other mentioned above you will need to preheat the area to be welded and maintain a post heat there are welding procedures to do this but rudimentary would be preheat to 200- 300 degrees C weld then reheat maintain heat for a period of time using thermal blankets wrapped around the area you need to obtain a gradual cooling rate this is a rough method you should really know the parent material composition precise preheat/ post heat temps and times to get a proper job grab a stick and whack some spoggy shit on er
Yeah I read about the carbon and those methods after a quick google search. I don't have an oxy so I might just try and try and try to drill a bigger hole with the springs actually out of the vehicle and fit the biggest bolt I can drill a hole for.
Re: weld
Posted: Wed Jul 30, 2008 9:07 pm
by GRPABT1
MUD80D wrote:Try using a die grinder they have worked for me in the past
just take it slow with a small bit
Yeah I thought of that today, cept I don't own one. Would I be pissing in the wind with a round metal file?
Posted: Wed Jul 30, 2008 9:27 pm
by Slunnie
harlequin wrote:spring steel is med to high carbon heat treated if you heat and quench it will harden changing the grain structure to martensite - extremely hard and brittle you can weld it with the correct rod maybe weldall or the other mentioned above you will need to preheat the area to be welded and maintain a post heat there are welding procedures to do this but rudimentary would be preheat to 200- 300 degrees C weld then reheat maintain heat for a period of time using thermal blankets wrapped around the area you need to obtain a gradual cooling rate this is a rough method you should really know the parent material composition precise preheat/ post heat temps and times to get a proper job grab a stick and whack some spoggy shit on er
Im not sure this makes sense.
As soon as the welder hits the martensite, it will normalise during cooling. I'm not sure a spring requires preheating to weld, and 200-300 degrees wont remove the martensitic structure. If you cool slowly as suggested and normalise, then you've really wasted your time with doing all of the above anyway and the whole spring still needs to have the proper heat treatment done on it.
If you really want to get into fire and all of that stuff, then stick the end of it over the BBQ and heat it until its properly red hot. Then then turn the heat down and then later off. This normalises (softens) the metal. Drill it, and then take it to the local spring works for heat treatment.
Edit, actually I'm not sure that a bbq flame has enough mumbo to heat a spring red hot.
Posted: Wed Jul 30, 2008 9:58 pm
by Gwagensteve
GRPABT1 -
don't try it it ill fail.
Drill if you have to, but if you make a sandwich mount with 4 bolts you can use a small bolt through the centre hole just to locate the spring. That's all I've done.
I vote about now it would have been easier to move the spring pads on the axle and put the 3/4 flat on the chassis.
Steve.
Posted: Wed Jul 30, 2008 10:14 pm
by GRPABT1
Don't go there steve

The problem is the centre hole for the spring is underneath the bump stop bracket
I'll pull the bastard springs out and buy some new bits tomorrow and give it a go that way. I am too close to having it finished to give up now.
Posted: Wed Jul 30, 2008 10:14 pm
by want33s

This is some funny shit...
Posted: Wed Jul 30, 2008 10:17 pm
by GRPABT1
want33s wrote:
This is some funny shit...
You won't be laughing when you see my fully sick flex uleh!

Posted: Wed Jul 30, 2008 10:36 pm
by harlequin
spring steel is med to high carbon heat treated if you heat and quench it will harden changing the grain structure to martensite was referring to eddy post the spring in its natural state wont be martensitic unless heated above its transition temp approx 760 degrees C then rapidly quenched it is the rate of cooling that will determine the grain structure shove it in ice water and it will crack