Page 1 of 2
Intake manifolds - diesel vs petrol
Posted: Fri Oct 30, 2009 7:07 am
by me3@neuralfibre.com
Interesting discussion on LCOOL over intake manifold design raised a thought.
Are diesels more sensitive to intake manifold design than petrols.
To my thinking the answer must be YES.
In (most) diesels the manifold is operating at WOT conditions all the time. Whilst peak RPM may be lower, limited max airflow, the average airflow would be much higher.
Now for the important bit.
With a petrol (carby or single point EFI) - the air is "pre mixed". An imbalance of flow to each cylinder will reduce the amount of fill, but essentially (if well atomised) - the mixture will remain constant regardless of fill. I have heard of some cars where the end, front or rear cylinders show evidence of micture variation from others, but never seen a discussion on it.
BUT - in a diesel, variation in fill will result in different mass air charges in each cylinder. As each cylinder gets the same fuel charge, at high fuel loadings, this would mean a (possibly significant) variation in EGT between cylinders. An EGT sensor reading the "average" of them all might say things are fine, whilst some are much higher, and others lower.
So in a petrol, differences in manifold flow may limit absolute power output. In a diesel - it could kill your engine, with all your gauges saying life is fine.
Is my thining correct?
I know some piston aircraft run EGT probes on each cylinder and adjust mixture (often manually) accordingly.
Multipoint petrol motors may suffer the same issue, but from what I understand they often exceed 25% duty cycle on the injectors, which implies crazy mixtures and flows in those particular manifolds. (injecting into a closed valve does what?)
Petrol direct injection - I guess it's hard to get right for a reason.
Paul
Posted: Fri Oct 30, 2009 7:38 am
by -Scott-
Not sure I can help with answers, but I can ask some questions.
Diesels are an excess air engine, and power/speed is controlled by the amount of fuel injected. At anything other than "WOT" (i.e. max fuel being injected) there should be more than enough air to burn all the fuel: are EGTs that likely to be an issue?
You're presuming that the difference in cylinder fill is significant. How much "vacuum" is created at the intake port due to flow restrictions in the manifold? Keep in mind that we're not necessarily talking a constant, steady flow - at 3000 rpm, each intake valve is opening and closing 25 times per second, and all sorts of pressure waves are bouncing backwards and forwards along the intake runners. Will each cylinder really receive a significantly different fill?
I'm not sure the comparison with aircraft engines is completely valid either. They operate at high altitudes with (effectively) extra vacuum, so cylinder fill behaviour at WOT will be subject to more variables than an engine operating within a few hundred metres of sea level. Were these engines with the individual controls NA or supercharged?
Finally, your comments re: injecting behind a closed port. Again, when the valve is opening and closing 25 (or 50, at 6000rpm) times per second it's not like the fuel spray has much time to "de-atomise" before the valve opens and it starts to more. AFAIK, it's not unusual for EFI engines to run injectors at 80%+ duty cycles for max power
Posted: Fri Oct 30, 2009 3:19 pm
by toy77
I have no idea about diesels at all....
But petrol motors...
Injecting to a closed valve is fine, and also has benefits including valve cooling and better vapouristion from hitting the hot valve. as long as it is not pooling in the manifold/head etc and going in as a liquid blob (poorly atomised) it is fine.
The situation you describe where one cylinder gets more or less air is common. Factory engineers spend alot of time trying to get this right. People can have issues modifying plenums themselves without understanding the implications.
Often these problems dont show up at factory power levels. but increase the turbo size, and airflow - then the difference between the cylinder tunes becomes greater. Lean hard on that engine and you may have issues. A good option after modifying an inlet is abrassive power porting. The flow through each runner is measured, then the lowest flowing runner is ported by forcing abrasive particles through it. This means it is ported where it is actually needed not just where it looks like it might.
Once the flows are reasonable balanced tuning from a single point (oxygen sensor) is ok.
As for individual cylinder tuning, that is a great set up. optimise each cylinder and account for any variations.... remember though that if an airplane motor stops it is generally a bigger problem than a car engine.
But yes you would get a better result from individual sensors - provided you can tune individually etc etc.... but it gets to a point where if the other systems are set up properly, you will gain very little at a great cost and inconvienience.
Cheers
Stew
Posted: Fri Oct 30, 2009 6:50 pm
by brad-chevlux
At WOT on an engine running on the edge, differences in cylinder fill can become a problem.
I've seen a hand full of old EA to AU falcon 6cyl engine go lean on the middle two cyls and kill the engine.
I doubt very much that TD42 and 1HZ manifolds flow all that well to cyls 1 and 6. when your pyro is reading 750 and cyls 1 and 6 are not filling aswell as 3 and 4, the temp on 1 and 6 could well be above 800.
You might find a gain if you spend alot of time designing and building manifolds, but unless you find the challenge enjoyable, it probably wouldn't be worth the effort.
Posted: Fri Oct 30, 2009 7:18 pm
by Wambat
i am finding this tread intresting, and wish to follow it, so i need to ask what is "WOT"? i assume worst operating temperature???
Posted: Fri Oct 30, 2009 7:22 pm
by toy77
Wide Open Throttle

Posted: Fri Oct 30, 2009 8:42 pm
by 80's_delirious
toy77 wrote:Wide Open Throttle

which can contribute to Worst Operating Temperature

Posted: Fri Oct 30, 2009 9:18 pm
by brad-chevlux
while we are on the topic, has anyone noticed that the runner lengths on the TD42 and 1HZ are more suited to and engine that revs twice as high.
It's probably a packaging and cost constraint but is hardly ideal for the rev range of a diesel engine.
The duel length runner manifold on the Ford 6cyls has a length of just over 24 inches on the long side, and it uses this length from idle to 3800rpm at which point it changes to a length of about 8 inches from 3800rpm to 5700rpm. (these lengths do not include port length)
Posted: Fri Oct 30, 2009 9:23 pm
by Kitika
I doubt the length of the runner on a diesel would have impact on the rev range as the fuel is mixed in the cylinder not in the manifold so it won't affect the power/revband.
Posted: Fri Oct 30, 2009 9:52 pm
by brad-chevlux
Kitika wrote:I doubt the length of the runner on a diesel would have impact on the rev range as the fuel is mixed in the cylinder not in the manifold so it won't affect the power/revband.
where the fuel is injected has nothing to do with it.
do a google on Helmholtz resonance and how it's applied to intake tuning.
Posted: Fri Oct 30, 2009 10:21 pm
by Kitika
So do you apply that theory to the whole intake tubing as there is no throttle that separates the manifold to the airbox + tubing etc?
Posted: Sat Oct 31, 2009 12:26 am
by zagan
All I could see is the Diesel manifold being much larger as the diesel motor runs at 80:1.
meaning there's 80 times more air to 1 shot of diesel fuel.
So if your not pushing in enough air you don't get the power you need, RPM won't really mean much as diesel are only have low RPMs due to the the much longer strokes on them.
A petrol motor is after a AFR of 15 (15:1) too low or too high and it won't run properly.
Petrol motors need the air/fuel to be mix before hand so pumping in petrol and mixing just before the valve would be normal and is pretty much a requirement on motorcycles, where they have 2 sets of injectors due to the motor cycling so fast that 1 set of injectors can't send in enough fuel for the air/fuel to mix quick enough, so a second set only comes on once your over 12,000RPMs for example.
Posted: Sat Oct 31, 2009 6:26 am
by bj on roids
flow the intake and run a phenolic spacer
Posted: Sat Oct 31, 2009 7:54 am
by brad-chevlux
zagan wrote: diesel are only have low RPMs due to the the much longer strokes on them.
A petrol motor is after a AFR of 15 (15:1) too low or too high and it won't run properly.
that is my whole point. they are low reving, yet have runner lengths that suit engines of 7000rpm you could increase torque alot by having a manifold with runner lengths in the range 20 to 30 inches instead of the facotry 6inches or so.
Posted: Sat Oct 31, 2009 9:02 am
by 85lux
it is not just flow that is important,in my mind, the harmonics of a manifold are more important.
lets switch to exhausts for a moment. it is commonly accepted that simply bolting on an oversized version of a factory "log" manifold that now with its increased size and flow will not always work as well as a correctly sized and WELL DESIGNED header. this is because it is a game of harmonics. with the flow in an automotive manifold being anything but steady, having valves opened and slammed shut on a body of gas rapidly trying to get into or out of a cylinder, causes pressure waves to bounce up and down along the manifold. this results in pressure variation at different points in the manifold. to make it even more tricky, it all changes with different load/rpm/ throttle position. what works at 2100rpm may leave a horrible flat spot due to cyl 2 and 3 leaning out at 2150rpm, however it may recover at 2200rpm. a simple test is to measure the temperature with an IR thermometer of your primary runners of the exhaust manifold while at load on a dyno. if they are the same, then your engine is in harmony. if they differ, then it suggests that your inlet manifold/exhaust manifold/cylinder head/cooling system or a host of other components are not treating all cylinders the same. this is partly why oem manifolds are often" odd looking" with cavities and lumps all over the place for seemingly only artistic value. they are there for a reason, and that reason is harmonics.
Posted: Sat Oct 31, 2009 10:14 am
by brad-chevlux
85lux wrote:it is not just flow that is important,in my mind, the harmonics of a manifold are more important.
lets switch to exhausts for a moment. it is commonly accepted that simply bolting on an oversized version of a factory "log" manifold that now with its increased size and flow will not always work as well as a correctly sized and WELL DESIGNED header. this is because it is a game of harmonics. with the flow in an automotive manifold being anything but steady, having valves opened and slammed shut on a body of gas rapidly trying to get into or out of a cylinder, causes pressure waves to bounce up and down along the manifold. this results in pressure variation at different points in the manifold. to make it even more tricky, it all changes with different load/rpm/ throttle position. what works at 2100rpm may leave a horrible flat spot due to cyl 2 and 3 leaning out at 2150rpm, however it may recover at 2200rpm. a simple test is to measure the temperature with an IR thermometer of your primary runners of the exhaust manifold while at load on a dyno. if they are the same, then your engine is in harmony. if they differ, then it suggests that your inlet manifold/exhaust manifold/cylinder head/cooling system or a host of other components are not treating all cylinders the same. this is partly why oem manifolds are often" odd looking" with cavities and lumps all over the place for seemingly only artistic value. they are there for a reason, and that reason is harmonics.
what you are talking about is Helmholtz resonance.
Kitika wrote:So do you apply that theory to the whole intake tubing as there is no throttle that separates the manifold to the airbox + tubing etc?
the length is from the back of the valve to next major change in size, in our case this change is the plenum.
The plenum has it own frequency and can be tuned to either help the runners at there peak or to help the runners at a point where they have little effect, OR both having the first order helping at lower RPM and the second and third (if the engine revs high enough) helping at higher RPM.
You can also have multiple changes in pipe size to create the effect at multiple RPM points, this is how stepped headers came about.
Though the effect from each step progressively gets weaker.
Posted: Sat Oct 31, 2009 10:35 am
by DanielS
I think there is some merit in this.
Of the big boosted TD42 I have heard fail (not many) it has always been as a result of 1 or 6 getting hot. Saying that I have seen them all crack between the liners.
So a bigger intake manifold would help balance out all the cyclinders - well I feel it would.
My2c
Daniels
Posted: Sat Oct 31, 2009 10:50 am
by brad-chevlux
just add a little more in to this.
Diesel engines effectively run at their peak air flow all the time.
so the effect would be greater then on a manifold injected petrol engine.
say you do %80 of your diving at 100km/h in 5th gear. for the sake of this post we'll say the engine is 2800RPM, If your intake runner length is short at around 6inches this would give the highest resonance effect at around 7000rpm or so. So lets say you change the length so that it is most effective at 2800rpm. the effect would be greater cylinder filling at your cruise RPM, making the engine more efficient.
Posted: Sun Nov 01, 2009 2:47 pm
by UNLUCKY
so....
who has changed there intake manifold on there diesel engine, what did you do, and what was the result?
i changed my turbo 4.2 intake to a 'wave' design, i feel the egt in all cylinders evened out, felt like the torque increased two fold, and way more responsive.
Posted: Sun Nov 01, 2009 6:51 pm
by 80's_delirious
UNLUCKY wrote:so....
who has changed there intake manifold on there diesel engine, what did you do, and what was the result?
i changed my turbo 4.2 intake to a 'wave' design, i feel the egt in all cylinders evened out, felt like the torque increased two fold, and way more responsive.
A pic is worth a thousand words

Id be very interested to see one
Posted: Sun Nov 01, 2009 8:29 pm
by KiwiBacon
brad-chevlux wrote:while we are on the topic, has anyone noticed that the runner lengths on the TD42 and 1HZ are more suited to and engine that revs twice as high.
I'm pretty sure both these engines share inlet manifolds with their turbocharged cousins. In a turbocharged engine the constantly changing manifold air temp makes resonance tuning a waste of time.
So the non turbo engines got the turbo manifolds as a cost saving measure?
Another thought on intake runner lengths. Don't the end cylinders have much longer runners (although bent) than the middle cylinders? I'd like to know what the effect of this was.
I've heard the VW SDI engines (non turbo) have very different inlet manifolds to the equivalent TDi engines. Another instance is comparing Isuzu's NA marine engines (4BD1X) to the industrial version. The marine has long intake runners which extend up and over the rocker cover. The industrial gets the compact manifold.
Posted: Sun Nov 01, 2009 8:50 pm
by UNLUCKY
[quote="80's_delirious
A pic is worth a thousand words

Id be very interested to see one[/quote]
read away....
ps, i'm a boilermaker not a tig welder....
this was the thread they were posted in. -
http://www.outerlimits4x4.com/ftopic122 ... highlight=
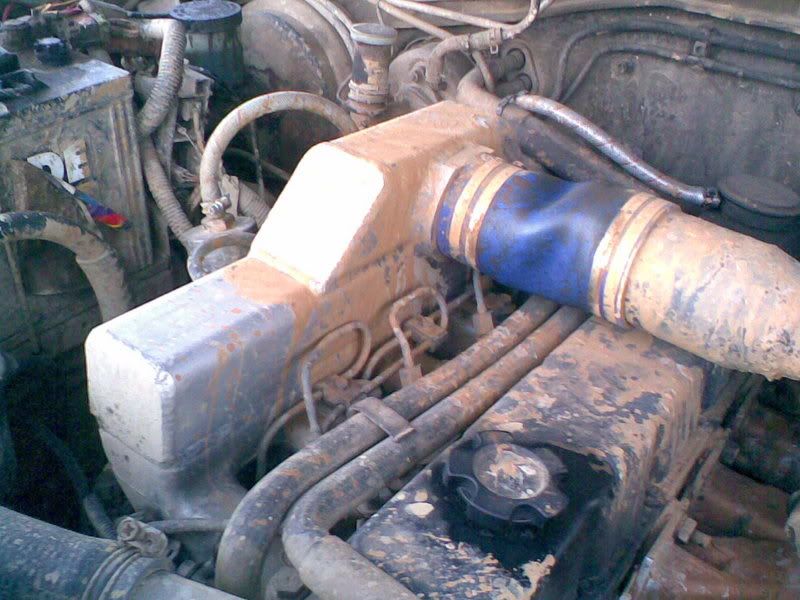
Posted: Sun Nov 01, 2009 9:12 pm
by -Scott-
I'm no expert, but I would expect NA inlet manifolds would have different flow characteristics to forced induction. As I think about this, I'm not sure it would be as applicable to a diesel engine.
Posted: Sun Nov 01, 2009 9:20 pm
by brad-chevlux
KiwiBacon wrote:brad-chevlux wrote:while we are on the topic, has anyone noticed that the runner lengths on the TD42 and 1HZ are more suited to and engine that revs twice as high.
In a turbocharged engine the constantly changing manifold air temp makes resonance tuning a waste of time.
That is a common misconception.
The temp of the air will not effect the fact that every time the valve closes it sends a pressure wave back up the runner and that every time the high pressure wave leaves the runner the low pressure left behind creates a high pressure wave back down the runner towards the intake valve.
Its just that the effect of this is small compared to that of adding 10psi of boost.
It's also note worthy that that first order wave is not as strong as the second order wave, the ideal is that the first order wave hit the back of a closed intake valve and is sent back up the runner to repeat the process and the second order wave is the one that gets the open intake valve, preferably at peak lift.
KiwiBacon wrote:
Another thought on intake runner lengths. Don't the end cylinders have much longer runners (although bent) than the middle cylinders? I'd like to know what the effect of this was.
All of the runners on my TD42 manifold are the same length.
using different length runner for each cylinder would have the effect of each cylinder getting slightly more or less air at any given RPM. When i first started researching this stuff i came across a racer that did this on purpose to help smooth out his engine 'peaky' power curve, each cylinder 'peaked' at a different RPM, thus providing a broader torque curve.
Posted: Sun Nov 01, 2009 9:24 pm
by brad-chevlux
-Scott- wrote:I'm no expert, but I would expect NA inlet manifolds would have different flow characteristics to forced induction. As I think about this, I'm not sure it would be as applicable to a diesel engine.
it's only pressure that changes. No different to driving at sea level compared to driving at 5000ft above.
It's more applicable to diesel engine as they run a full air flow all of the time.
I have done some working on it, and although the benefit is there, it may not be practical as to get the second order wave to happen at a low enough RPM we'd be looking at runner lengths in the range 900mm to 1200mm
But even an increase to 600mm or so would show an increase in cylinder fill with the RPM range that these engines have.
And both could benefit from larger plenums.
Posted: Mon Nov 02, 2009 5:22 am
by KiwiBacon
Brad Chevlux wrote:Kiwibacon wrote:In a turbocharged engine the constantly changing manifold air temp makes resonance tuning a waste of time.
That is a common misconception.
The temp of the air will not effect the fact that every time the valve closes it sends a pressure wave back up the runner and that every time the high pressure wave leaves the runner the low pressure left behind creates a high pressure wave back down the runner towards the intake valve.
Its just that the effect of this is small compared to that of adding 10psi of boost.
You've missed the most vital part of that. The change in temperature.
The change in temperature changes the sonic velocity (i.e. the speed of those pulses) which makes attempting to tune their behaviour a futile exercise.
The end cylinders on a manifold can have part of the plenum acting like a runner (depending of course on the geometry of everything). Increasing the effective length of that runner in some cases.
Posted: Mon Nov 02, 2009 9:59 am
by me3@neuralfibre.com
Obviously the resonance frequency matters (see 2 stroke petrol) BUT
I was thinkign of simple differential flow, and EGT's variance.
What in a petrol would lose you some power, in a diesel could kill the motor.
I would like to know which is more significant, flow restrictions, or resonance patterns.
I suspect the resonance would be the same boosted or not, but the points and benefits would change.
Boosted doubles the pressure diff between cylinder and manifold, so 10% from resonance is less critical (to my thinking)
Then again - 10% of doubled mass is still significant.
It would be interesting to measure EGT variance with OEM vs custom "adhoc" manifolds.
I know the 1HZ manifold has some "tricks" up it's sleeve for what looks to be a very small, simple log design.
Paul
Posted: Mon Nov 02, 2009 5:50 pm
by brad-chevlux
KiwiBacon wrote:Brad Chevlux wrote:Kiwibacon wrote:In a turbocharged engine the constantly changing manifold air temp makes resonance tuning a waste of time.
That is a common misconception.
The temp of the air will not effect the fact that every time the valve closes it sends a pressure wave back up the runner and that every time the high pressure wave leaves the runner the low pressure left behind creates a high pressure wave back down the runner towards the intake valve.
Its just that the effect of this is small compared to that of adding 10psi of boost.
You've missed the most vital part of that. The change in temperature.
The change in temperature changes the sonic velocity (i.e. the speed of those pulses) which makes attempting to tune their behaviour a futile exercise.
at cruise the boost level and temps are low. the thing with diesel engines is they don't limit air flow to control engine speed. So this tuning can be used to improve efficiency at cruise. It doesn't always have to be about peak power.
You'll also find a number of threads on this site showing some boosted/intercooled engines with charge temps under 60degrees. I have personly tested a few N/A engines and found IA temps above 80degrees.
KiwiBacon wrote:
The end cylinders on a manifold can have part of the plenum acting like a runner (depending of course on the geometry of everything). Increasing the effective length of that runner in some cases.
A well designed manifold wouldn't suffer that problem.
Posted: Mon Nov 02, 2009 6:36 pm
by KiwiBacon
brad-chevlux wrote:
at cruise the boost level and temps are low. the thing with diesel engines is they don't limit air flow to control engine speed. So this tuning can be used to improve efficiency at cruise. It doesn't always have to be about peak power.
At cruise my 4wd runs about 9psi. Give it a headwind and it's 12psi.
Have a play with this calculator and see the difference it makes:
http://www.sengpielaudio.com/calculator-speedsound.htm
Posted: Mon Nov 02, 2009 7:42 pm
by brad-chevlux
KiwiBacon wrote:brad-chevlux wrote:
at cruise the boost level and temps are low. the thing with diesel engines is they don't limit air flow to control engine speed. So this tuning can be used to improve efficiency at cruise. It doesn't always have to be about peak power.
At cruise my 4wd runs about 9psi. Give it a headwind and it's 12psi.
Have a play with this calculator and see the difference it makes:
http://www.sengpielaudio.com/calculator-speedsound.htm
Mine makes 3psi at 100km/h and 1psi at 70km/h
I'm not doubting it makes a difference, all i'm saying is you can't blanket every turbo engine.
With effective intercooling the temp changes is minimal.
Even with huge changes in temp a well designed manifold on a TD42 or 1HZ will out perform the compromise that is the stock item.
All anyone that is interested in doing it needs to do is log charge temp for a while and use that info in the design of the manifold. They may even choose not to worry about runner length and focus plenum design and runner placement to attempt to get perfect distribution between all runners.