Mechanical Diesel Engine Tuning - No Chips!
Posted: Sat Dec 17, 2011 6:16 pm
After much demand, I have decided to write an article on how to tune the good old TD42 and any other compensated/non compensated diesel injector pump. I will only be covering rotary style pumps in this article, Inline is very different!
And please remember, this is a basic guide only. I will not be going into alot of depth regarding how pumps or injectors work. Just the basics so people can understand what I am talking about.
Please DO NOT!!!!! Use this guide without the proper tools and equipment to tune your vehicle correctly and more importantly SAFELY! Take it to your local Diesel specialist, question how they go about things then choose weather or not to use them.
Diesel Injector Pump - Supplies pressure to the injectors at the correct time, to allow them to fire when needed.
It does this through the compression of the fuel inside by using interference fit components that shrink in size as the pump rotates, forcing fuel through certain passages which increases the pressure the fuel is under.
Injector Pressure - Injectors have what is called a 'Crack Pressure'
This is the pressure that the fuel forces the needle/pintle off its seat, and allows fuel to flow through the tip of the injector.
As the pump continues through its revolution, the provided pressure decreases and the injector will return to a closed state.
The important parts of the injectors are.
Body - Nozzle - Pintle - Spring - Shim
The pressure each injector will fire at depends on one thing alone. How much tension the spring provides on the pintle which is seated against the nozzle.
We can reduce or increase this tension by adjusting the size of the shim that is underneath the spring. Thicker shims mean more tension, thinner shims mean less tension.
If we lower the pressure they open at we effectively advance the timing of the injector firing sequence, if we increase it we effectively retard the timing of the injector firing sequence.
Different cars are built around different injector opening pressures. It is important to have these checked/reset every 90-100K kms due to the spring loosing tension over a period of time.
How Timing Works on a Non Electric Pump -
As the pump ramps the pressure up to Crack pressure, the injector will fire. If the pump is rotated one way, this pressure will build up earlier in the stroke, meaning Crack pressure will be achieved earlier than normal resulting in fast or 'advanced timing'
If we rotate the pump the other way, the crack pressure will build up later in the stoke, resulting in the injector firing later or 'more retarded'
So it is very important to remember, there is more than one timing adjustment on this style of engine.
Pump Timing Adjustment
Injector Pressure Timing Adjustment.
Both must be set to compliment each other. You can have thicker shims in the injector to increase injection pressure which is good!
But you must advance the pump up to ensure it is being injected at the correct time.
Boost Compensators -
With turbocharged engines we have vastly different amounts of airflow on boost to what we have off boost. A 'Compensator' is designed to modify the pump in a 3D fashion dependant on this extra flow/pressure the turbo provides.
It does this through a pressure intake port in the top of it, which pushes an internal diaphragm containing the fuel pin down into the pump. This increases the amount of fuel delivered depending on the boost pressure pushing down on it.
Types of Adjustment -
These types of pumps have a few adjustments.
1) Fuel Screw / Main Metering Screw (overall adjustment)
2) Compensator No Boost Screw (off boost fueling)
3) Compensator Pin Spring Tension (Turbo Spool fueling)
4) Compensator Pin Shims / Max travel shim (Max boost fueling)
5) Compensator Pin Rotation (for eccentric pins only) (overall on boost fueling)
Now, I apologise for my lack of diagram making skills you will see below. But it is the best I could do. So if anybody feels like making nice and spiffy diagrams for me, I would welcome it so I dont look like such a dork with what I have made
FUEL SCREW
This adjusts your overall fueling in any pump.
More or less and by an equal amount through the pumps delivery range.
If you add here, you gain more at idle all the way through to maximum rpm.
This is the only adjustment on a non compensated pump. You will see below the downfalls to this on a turbocharged engine.
The main drawbacks to using just the fuel screw on a turbo engine is it doesnt take into account the extra pressure or flow of turbo adjustments or upgrades.
Upgrading you turbo and or intercooler, will normally mean more airflow. But not through the whole rpm range.
Some will provide bucket loads of boost and flow down low, others provide alot more higher in the rev range.
Its for this reason alone, the fuel screw should be kept as is until more overall fueling is required. Then the compensator should be readjusted to suit this extra flow.
Standard Non Compensated Pump Fueling on a naturally aspirated diesel
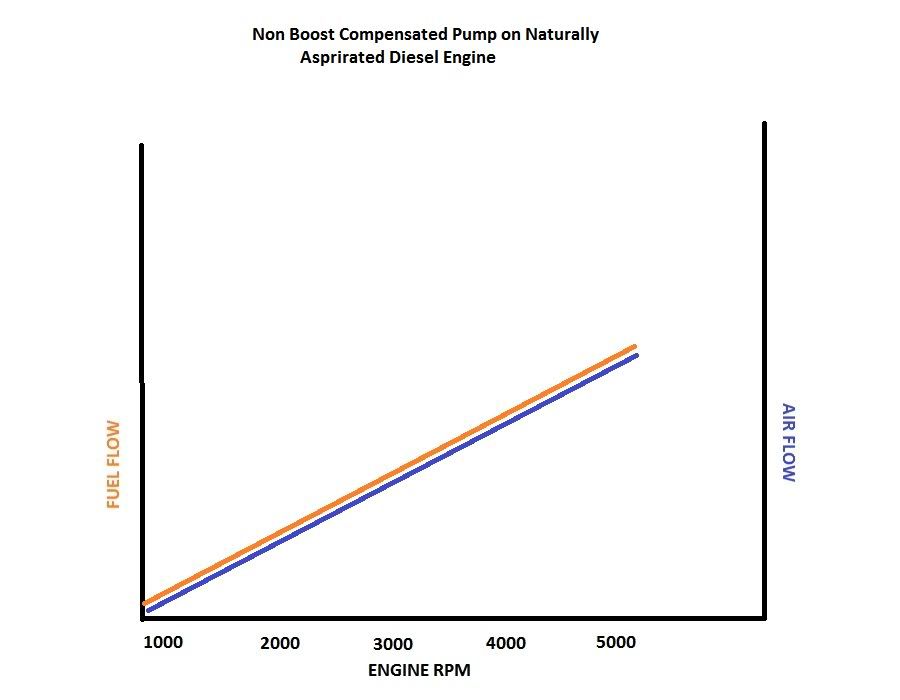
Standard Non Compensated Pump Fueling on Turbocharged Engine.
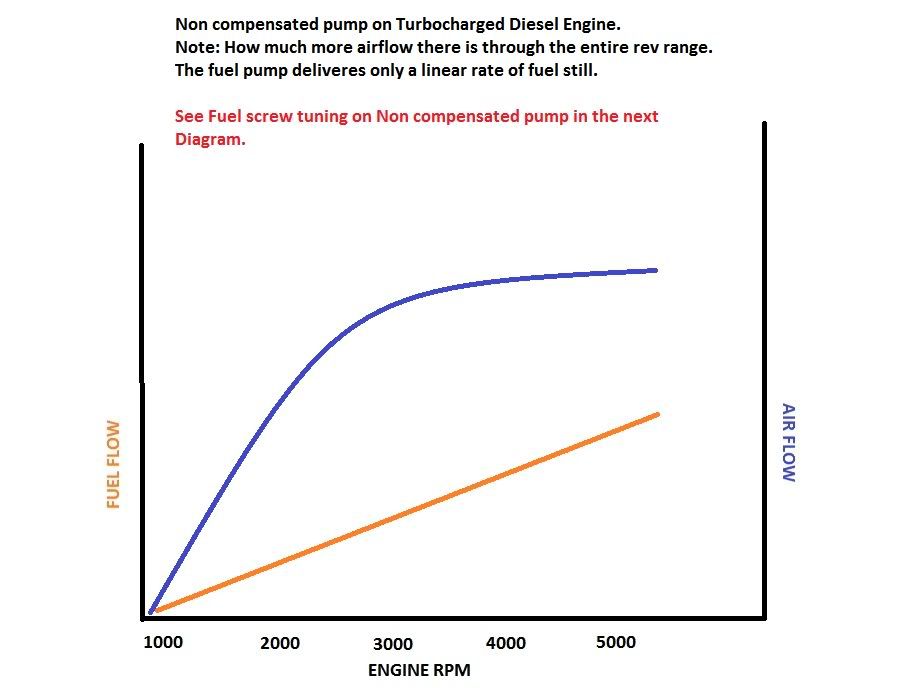
Non compensated pump fueling on a turbo engine
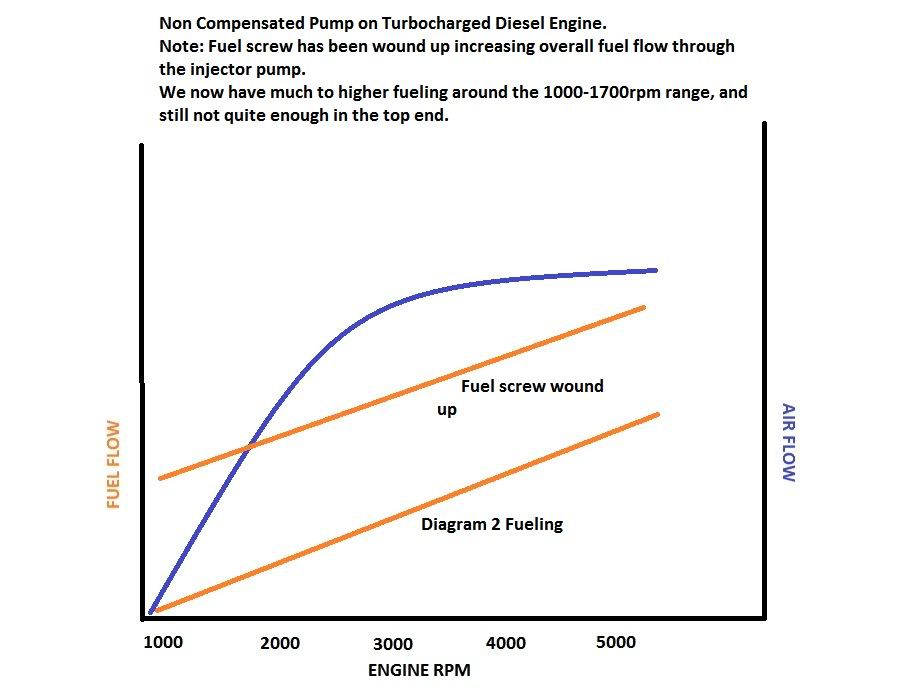
Fuel Screw tuning on a turbo engine without compensator
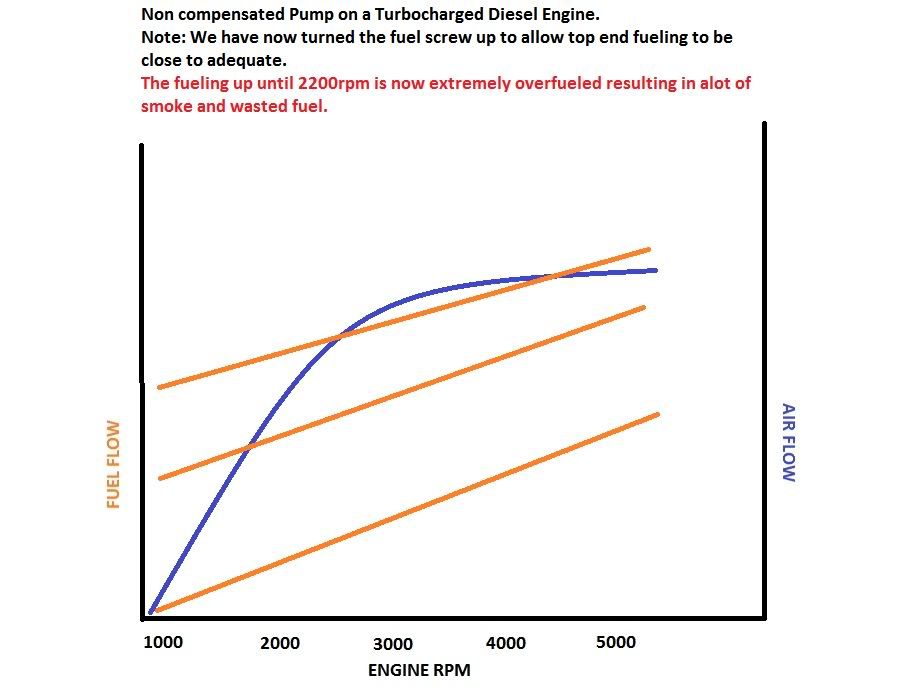
NO BOOST FUEL - COMPENSATOR
This is used to adjust the amount of fuel added off boost on a compensated pump.
It can greatly enhance throttle response by allowing more off boost fuel to be injected.
This is generally not adjusted on most vehicles, unless significant airflow improvements are made to the engine, which will necessitate in more fueling requirements off boost.
Standard Tuning with Boost Compensated Pump on Turbo Engine
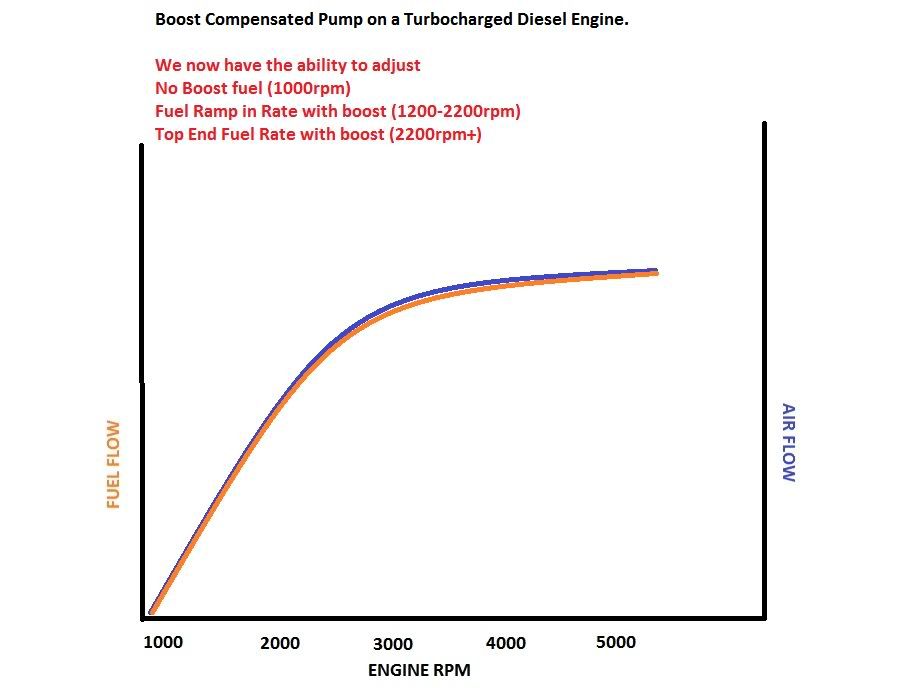
No Boost fuel adjustment
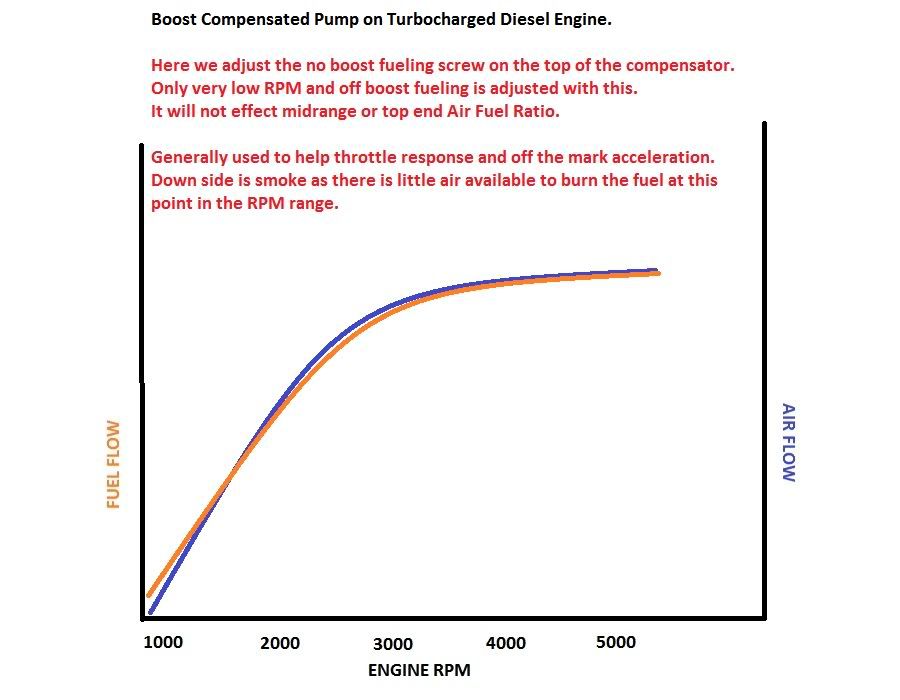
Spring Tension Adjustment:
The spring tension of the pin adjusts how far 'X' amount of boost pushes the compensator pin down. Lower tension means more fuel for the same boost pressure, more tension means less fuel for the same boost pressure.
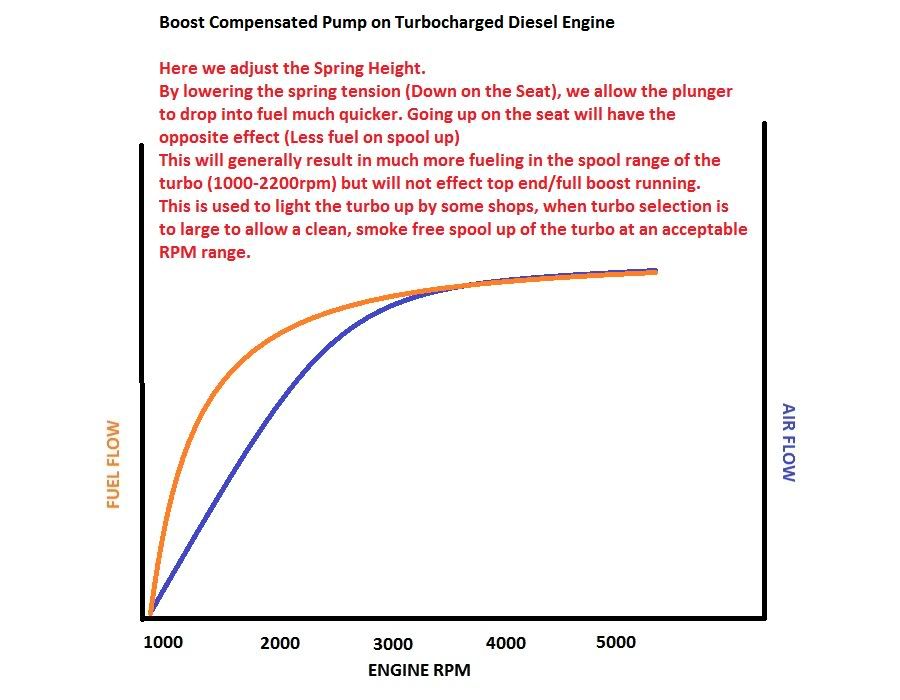
Overall Pin Travel Adjustment / Shim Packs:
The amount of shims underneath the pin increases or reduces how far down into the compensator the pin will travel under full boost conditions.
More shims = Full boost fueling
Less shims = less full boost fueling
Fuel Pin Travel Adjustment
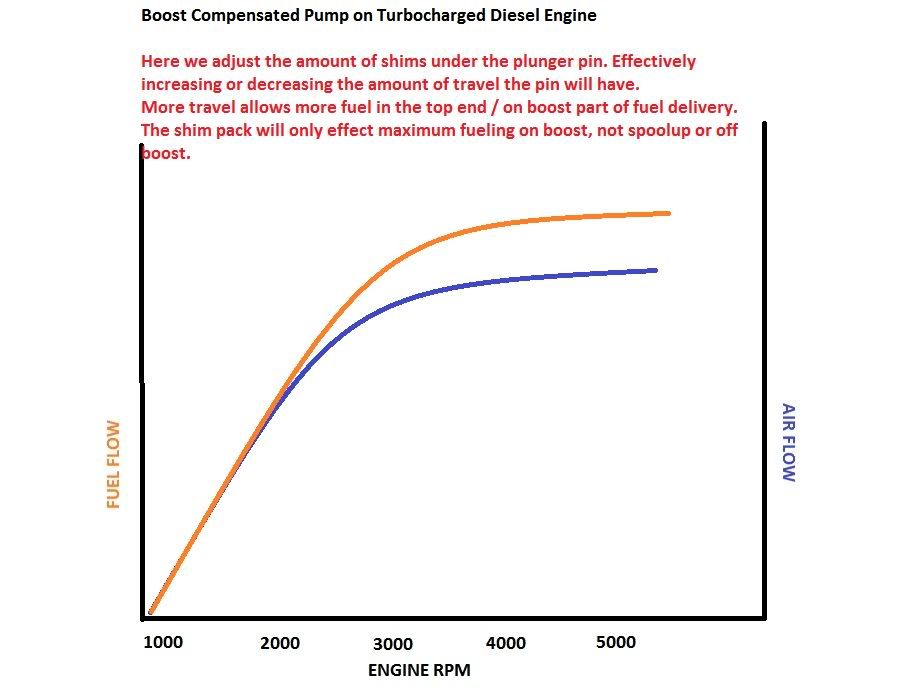
Fuel Pin Rotation
Fuel pins are in most cases eccentric. What this means is that on one side they have a steep taper, and on the other a shallow taper.
With obviously a smooth transition between each on the cylindrical shaft.
If the taper is steep, the amount of fuel added will be greater.
If the taper is shallow, the amount of fuel added will be less.
By turning this pin though 360 degrees of rotation, we go from minimum fueling at 0 degrees, to maximum fueling at 180degrees and back to minimum fueling when we hit 360degrees again. With an equal and progressive amount more/less throughout its rotation.
This gives us an overall adjustment from 0psi to full psi.
Fuel Pin Rotation Adjustment:
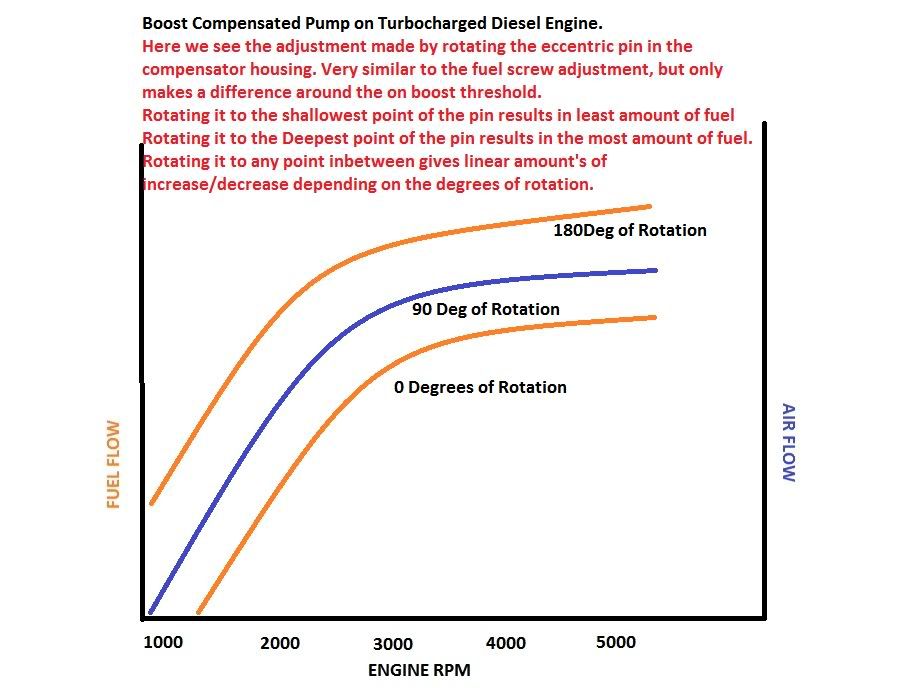
So when you get your pump tuned - Ask the shop, how do they tune it?
Is it fuel screw? Is it on the compensator? Because there is a big difference to be had in economy and overall power between the two types of tuning.
And please remember, this is a basic guide only. I will not be going into alot of depth regarding how pumps or injectors work. Just the basics so people can understand what I am talking about.
Please DO NOT!!!!! Use this guide without the proper tools and equipment to tune your vehicle correctly and more importantly SAFELY! Take it to your local Diesel specialist, question how they go about things then choose weather or not to use them.
Diesel Injector Pump - Supplies pressure to the injectors at the correct time, to allow them to fire when needed.
It does this through the compression of the fuel inside by using interference fit components that shrink in size as the pump rotates, forcing fuel through certain passages which increases the pressure the fuel is under.
Injector Pressure - Injectors have what is called a 'Crack Pressure'
This is the pressure that the fuel forces the needle/pintle off its seat, and allows fuel to flow through the tip of the injector.
As the pump continues through its revolution, the provided pressure decreases and the injector will return to a closed state.
The important parts of the injectors are.
Body - Nozzle - Pintle - Spring - Shim
The pressure each injector will fire at depends on one thing alone. How much tension the spring provides on the pintle which is seated against the nozzle.
We can reduce or increase this tension by adjusting the size of the shim that is underneath the spring. Thicker shims mean more tension, thinner shims mean less tension.
If we lower the pressure they open at we effectively advance the timing of the injector firing sequence, if we increase it we effectively retard the timing of the injector firing sequence.
Different cars are built around different injector opening pressures. It is important to have these checked/reset every 90-100K kms due to the spring loosing tension over a period of time.
How Timing Works on a Non Electric Pump -
As the pump ramps the pressure up to Crack pressure, the injector will fire. If the pump is rotated one way, this pressure will build up earlier in the stroke, meaning Crack pressure will be achieved earlier than normal resulting in fast or 'advanced timing'
If we rotate the pump the other way, the crack pressure will build up later in the stoke, resulting in the injector firing later or 'more retarded'
So it is very important to remember, there is more than one timing adjustment on this style of engine.
Pump Timing Adjustment
Injector Pressure Timing Adjustment.
Both must be set to compliment each other. You can have thicker shims in the injector to increase injection pressure which is good!
But you must advance the pump up to ensure it is being injected at the correct time.
Boost Compensators -
With turbocharged engines we have vastly different amounts of airflow on boost to what we have off boost. A 'Compensator' is designed to modify the pump in a 3D fashion dependant on this extra flow/pressure the turbo provides.
It does this through a pressure intake port in the top of it, which pushes an internal diaphragm containing the fuel pin down into the pump. This increases the amount of fuel delivered depending on the boost pressure pushing down on it.
Types of Adjustment -
These types of pumps have a few adjustments.
1) Fuel Screw / Main Metering Screw (overall adjustment)
2) Compensator No Boost Screw (off boost fueling)
3) Compensator Pin Spring Tension (Turbo Spool fueling)
4) Compensator Pin Shims / Max travel shim (Max boost fueling)
5) Compensator Pin Rotation (for eccentric pins only) (overall on boost fueling)
Now, I apologise for my lack of diagram making skills you will see below. But it is the best I could do. So if anybody feels like making nice and spiffy diagrams for me, I would welcome it so I dont look like such a dork with what I have made

FUEL SCREW
This adjusts your overall fueling in any pump.
More or less and by an equal amount through the pumps delivery range.
If you add here, you gain more at idle all the way through to maximum rpm.
This is the only adjustment on a non compensated pump. You will see below the downfalls to this on a turbocharged engine.
The main drawbacks to using just the fuel screw on a turbo engine is it doesnt take into account the extra pressure or flow of turbo adjustments or upgrades.
Upgrading you turbo and or intercooler, will normally mean more airflow. But not through the whole rpm range.
Some will provide bucket loads of boost and flow down low, others provide alot more higher in the rev range.
Its for this reason alone, the fuel screw should be kept as is until more overall fueling is required. Then the compensator should be readjusted to suit this extra flow.
Standard Non Compensated Pump Fueling on a naturally aspirated diesel
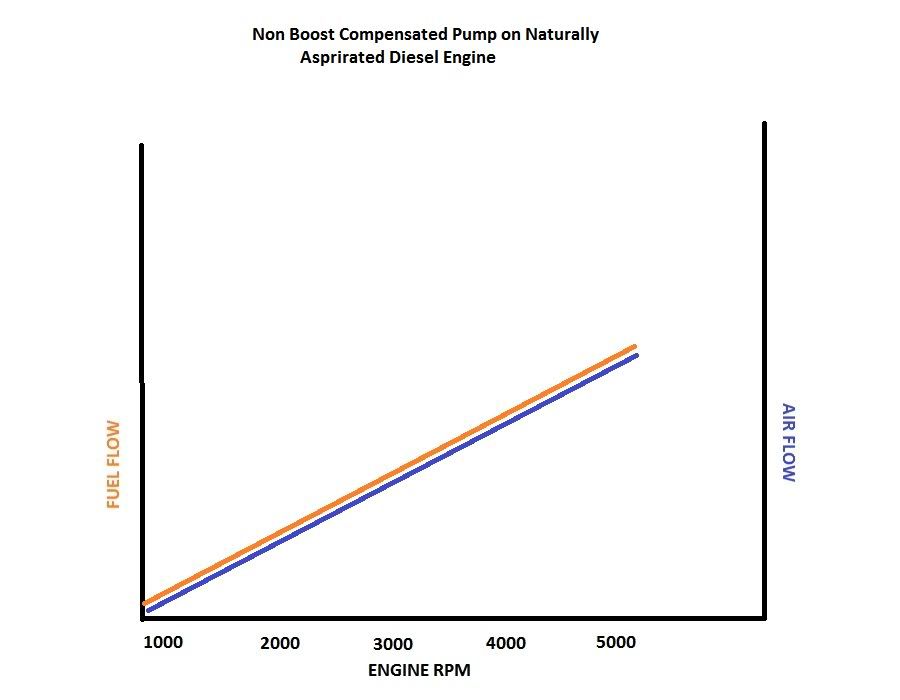
Standard Non Compensated Pump Fueling on Turbocharged Engine.
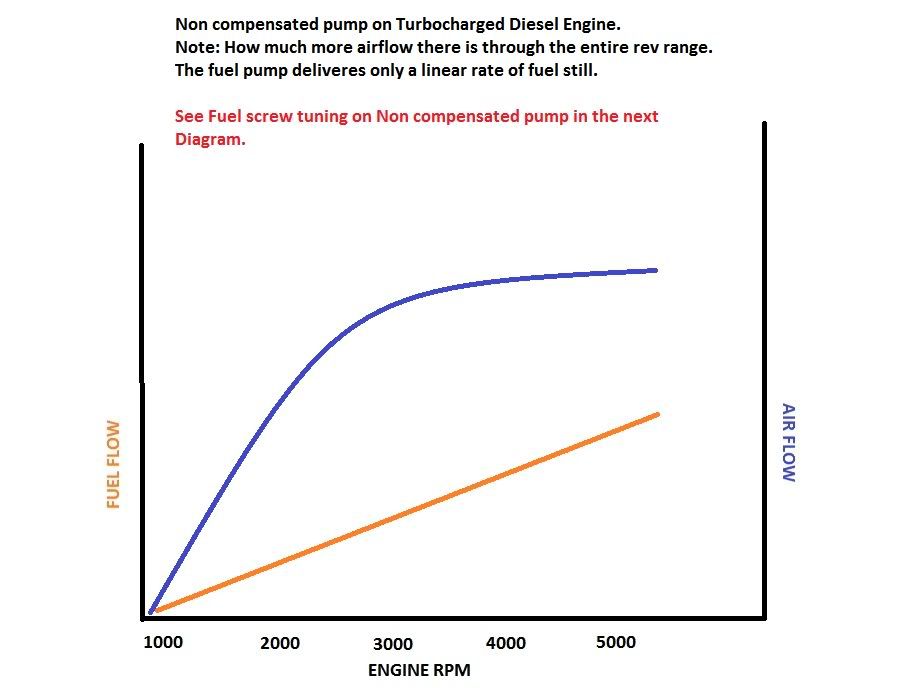
Non compensated pump fueling on a turbo engine
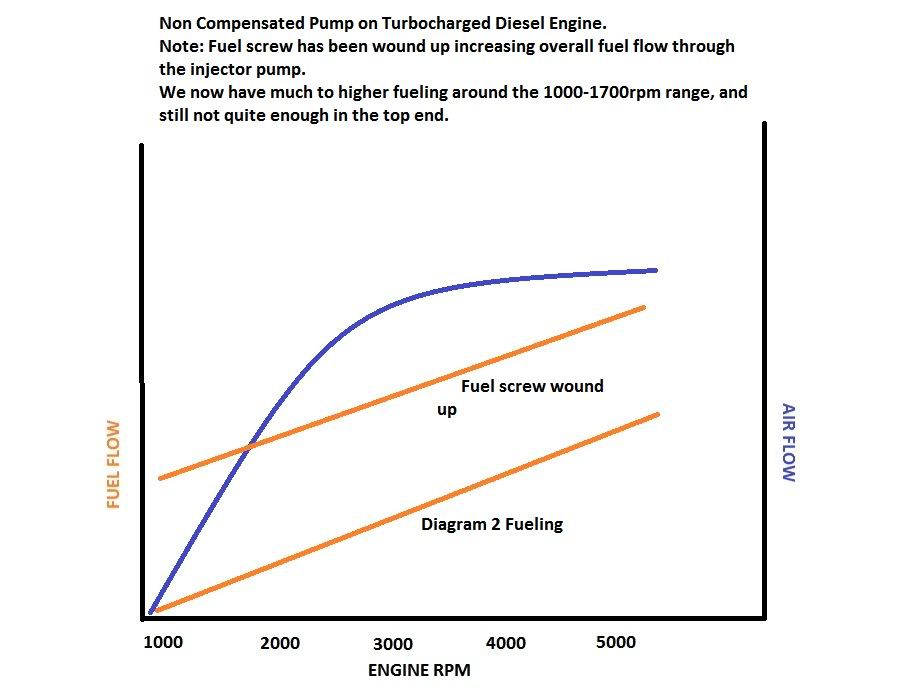
Fuel Screw tuning on a turbo engine without compensator
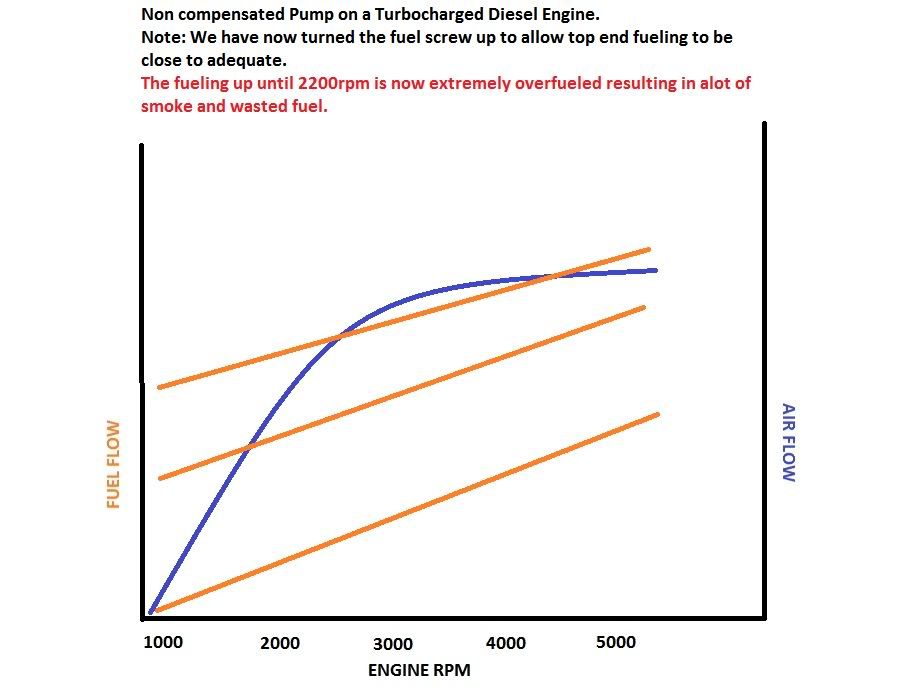
NO BOOST FUEL - COMPENSATOR
This is used to adjust the amount of fuel added off boost on a compensated pump.
It can greatly enhance throttle response by allowing more off boost fuel to be injected.
This is generally not adjusted on most vehicles, unless significant airflow improvements are made to the engine, which will necessitate in more fueling requirements off boost.
Standard Tuning with Boost Compensated Pump on Turbo Engine
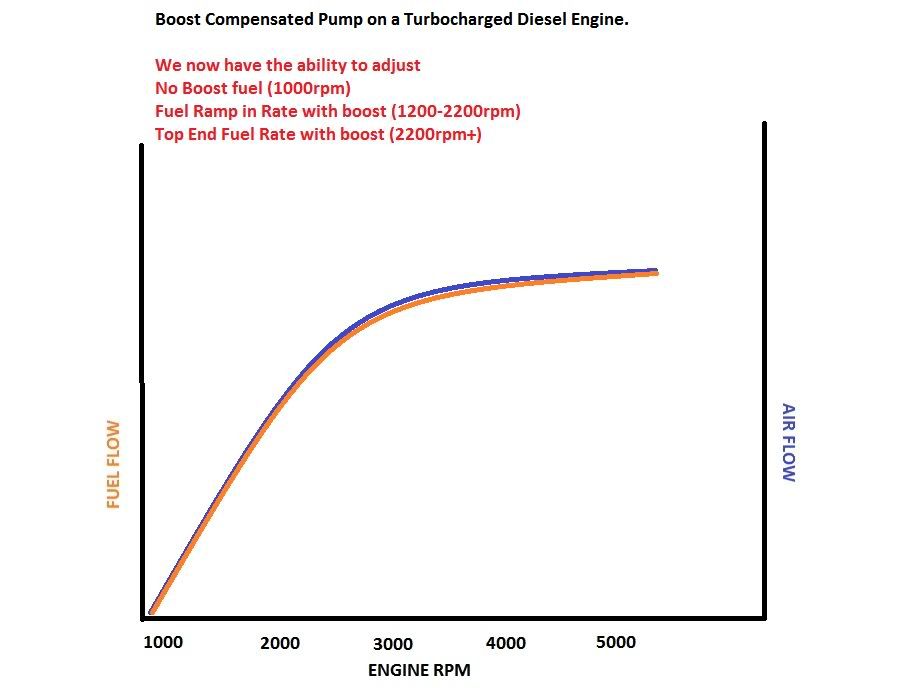
No Boost fuel adjustment
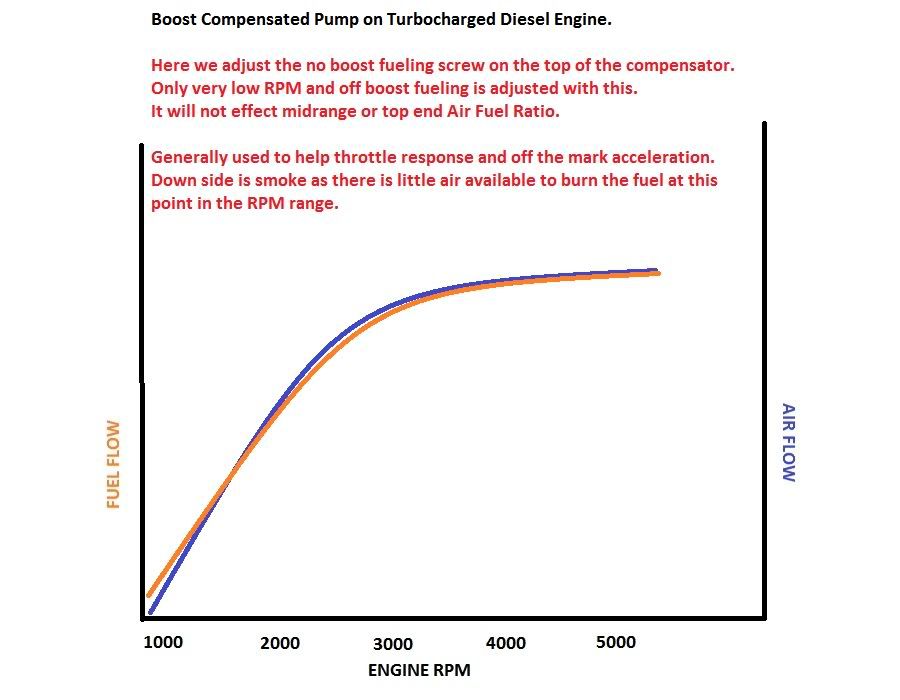
Spring Tension Adjustment:
The spring tension of the pin adjusts how far 'X' amount of boost pushes the compensator pin down. Lower tension means more fuel for the same boost pressure, more tension means less fuel for the same boost pressure.
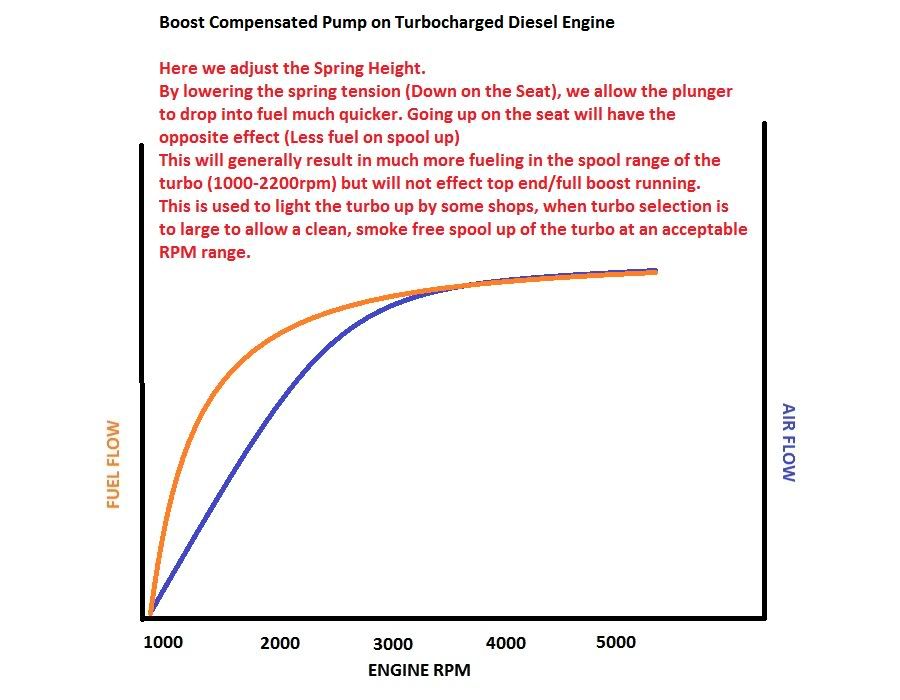
Overall Pin Travel Adjustment / Shim Packs:
The amount of shims underneath the pin increases or reduces how far down into the compensator the pin will travel under full boost conditions.
More shims = Full boost fueling
Less shims = less full boost fueling
Fuel Pin Travel Adjustment
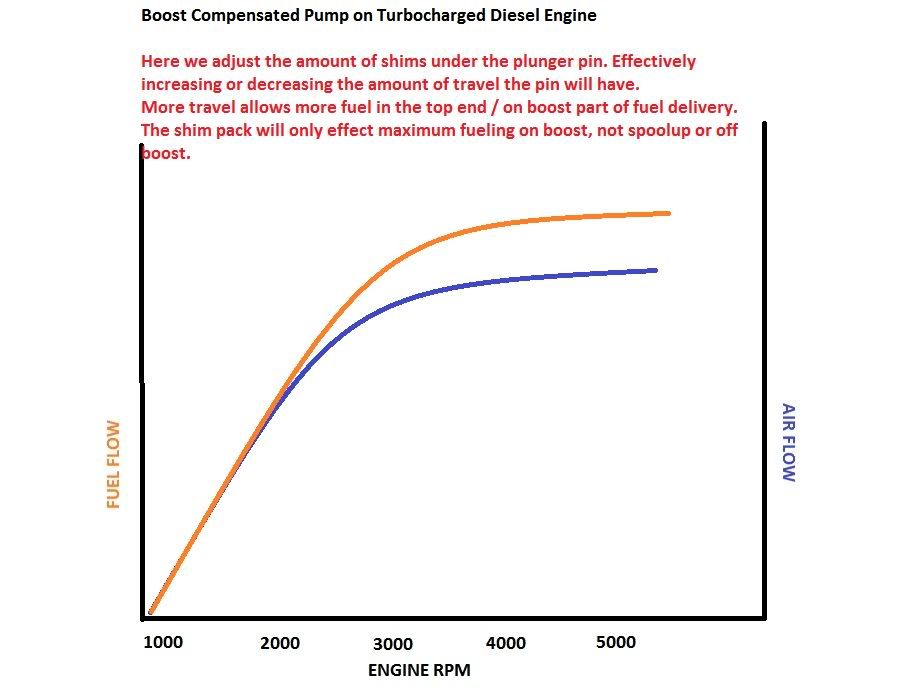
Fuel Pin Rotation
Fuel pins are in most cases eccentric. What this means is that on one side they have a steep taper, and on the other a shallow taper.
With obviously a smooth transition between each on the cylindrical shaft.
If the taper is steep, the amount of fuel added will be greater.
If the taper is shallow, the amount of fuel added will be less.
By turning this pin though 360 degrees of rotation, we go from minimum fueling at 0 degrees, to maximum fueling at 180degrees and back to minimum fueling when we hit 360degrees again. With an equal and progressive amount more/less throughout its rotation.
This gives us an overall adjustment from 0psi to full psi.
Fuel Pin Rotation Adjustment:
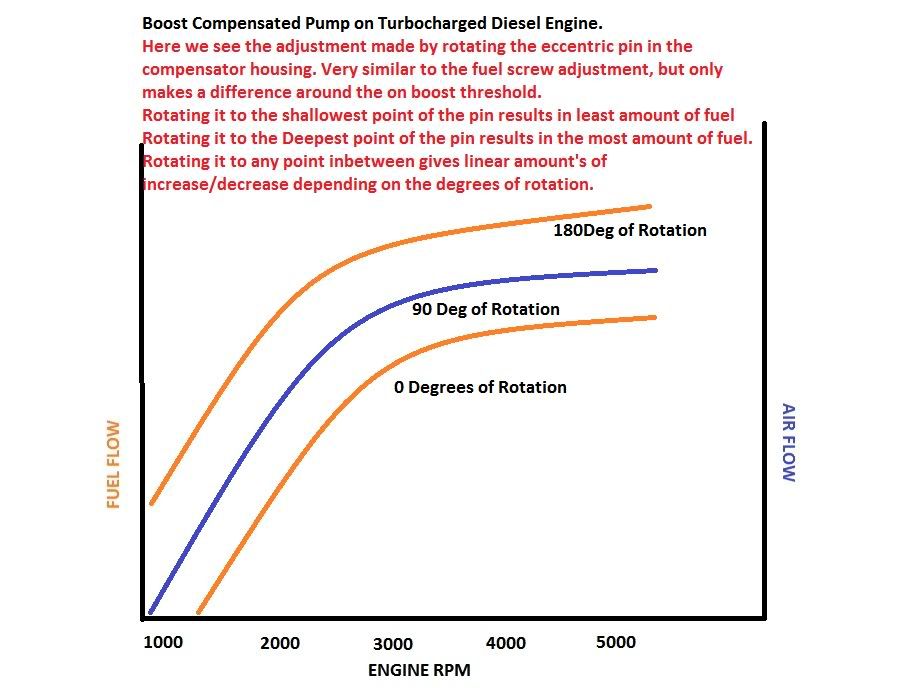
So when you get your pump tuned - Ask the shop, how do they tune it?
Is it fuel screw? Is it on the compensator? Because there is a big difference to be had in economy and overall power between the two types of tuning.