Notice: We request that you don't just set up a new account at this time if you are a previous user.
If you used to be one of our moderators, please feel free to reach out to Chris via the facebook Outerlimits4x4 group and he will get you set back up with access should he need you.
If you used to be one of our moderators, please feel free to reach out to Chris via the facebook Outerlimits4x4 group and he will get you set back up with access should he need you.
Recovery:If you cannot access your old email address and don't remember your password, please click here to log a change of email address so you can do a password reset.
I know they don't work but I am building one anyway, Thread
God Of Emo
Posts: 7350
Joined: Sun Aug 24, 2003 7:04 pm
Joined: Sun Aug 24, 2003 7:04 pm
Location: Newy, home of the ZOOK (Rockin the 'diff)
Contact:
11_evl wrote:so what is the best way to over come this problem??
mart your idea looks good. has anyone else had success with this way??
The only way to overcome this, if you must stay with leaves is to go to a tri-4 link rear end with twin shackle setup leaves.
Leaves suffer from having to do many tasks, they have to hold the vehicle up, they have to provide springing action to the suspension, and they have to also transfer drive force from axle tube to the chassis, as well as brakeing force. They see a rotational force as well as a forward thrust at their connection to the axle tube, and must transfer this to a 'straight line' force at the connection to the chassis. Having to do all these things means there will always be compromise. If looking at the way a leaf suspension cycles through its arc of travel, any set point on the leaf will transcribe a eccentric arc. Unless we can replicate this arc of travel with the front end of a anti-wrap device, it will always influence the leave/axle assembly. As most track bars have a shackle or slip'n'twist joint, they can move forwards and backwars, but forward point (connection to the chassis) causes them to also transcribe an arc as the suspension cycles. This arc differs from what the axle usually travels in due to the action of the leaves. These two differing arcs mean that there will be binding in the system, causing loss of travel, or even damage as Pete found out

Soooooooooooooo, Basically there is no way that a traditional track bar can be built that will not influence the suspension. But by making it long, flat and low you can limit its negative influence on the suspension dynamics, to the point where it is not a major issue.
Layto....
[quote="v840"]Just between me and you, I actually really dig the Megatwon, but if anyone asks, I'm going to shitcan it as much as possible! :D[/quote]
but making it long, flat and low is pretty hard in a car with an 80" wheelbase and lots of lift.
Ihave sketched up most of these ideas for hours and they don't work without influence, even in a SPUA car.
Have alook though at the Superlift "torque fork" it seems to be working quite well in the US but when I looked at the design it didn't look to be it would do anything.
Petersens are running one in their UAJK, and whilst that is a long, low flat bar, the car does have 42's and almost 900nm.
Steve.
Ihave sketched up most of these ideas for hours and they don't work without influence, even in a SPUA car.
Have alook though at the Superlift "torque fork" it seems to be working quite well in the US but when I looked at the design it didn't look to be it would do anything.
Petersens are running one in their UAJK, and whilst that is a long, low flat bar, the car does have 42's and almost 900nm.
Steve.
[quote="greg"] some say he is a man without happy dreams, or that he sees silver linings on clouds and wonders why they are not platinum... all we know, is he's called the stevie.[/quote]
thankx lay80n
i thought as much, but just wanting a better way than what i had to get me by till i get my diff centers and go coil front and rear.
my current setup is a bar about 19" long with a shackle type aetup. it seems to flex ok but has a bad case of lifting the left side as i accelerate due to the way it operates. it lasted about 2 months till it did this

and this is only pic i got of it in operation. thats fully flexed with the rhr wheel stuffed

i thought as much, but just wanting a better way than what i had to get me by till i get my diff centers and go coil front and rear.
thats it. there must be a viable way to make it work as the yanks are 90% spoa and plenty of power.Gwagensteve wrote:but making it long, flat and low is pretty hard in a car with an 80" wheelbase and lots of lift.
Ihave sketched up most of these ideas for hours and they don't work without influence, even in a SPUA car.
Have alook though at the Superlift "torque fork" it seems to be working quite well in the US but when I looked at the design it didn't look to be it would do anything.
Petersens are running one in their UAJK, and whilst that is a long, low flat bar, the car does have 42's and almost 900nm.
Steve.
my current setup is a bar about 19" long with a shackle type aetup. it seems to flex ok but has a bad case of lifting the left side as i accelerate due to the way it operates. it lasted about 2 months till it did this

and this is only pic i got of it in operation. thats fully flexed with the rhr wheel stuffed

Last edited by 11_evl on Thu Feb 07, 2008 8:56 pm, edited 1 time in total.
michael
Who said the ones in the US work? the most prevalent US design (the "Sam's offroad" style) was unable to be engineered here in Vic with the engineer we were using on Greg's project due to excessive spring influence.
The torque fork is a brand new design and was custom built for the UAJK which has over 120" of wheelbase. It's not being advertised as yet. THe UAJK is massive and the whole car is very very low - the bar is almost flat at ride height and looks to be about 5 feet long. (really)
AS I pointed out at the start of this thread, I have seen some very impressive torque bars on long wheelbase cars, but it's pretty much impossible in an 80" wheelbase sierra.
Steve.
The torque fork is a brand new design and was custom built for the UAJK which has over 120" of wheelbase. It's not being advertised as yet. THe UAJK is massive and the whole car is very very low - the bar is almost flat at ride height and looks to be about 5 feet long. (really)
AS I pointed out at the start of this thread, I have seen some very impressive torque bars on long wheelbase cars, but it's pretty much impossible in an 80" wheelbase sierra.
Steve.
[quote="greg"] some say he is a man without happy dreams, or that he sees silver linings on clouds and wonders why they are not platinum... all we know, is he's called the stevie.[/quote]
I have found reasonable success with a shackle mounted bar with a threaded section to allow twist, as stated it would technically create binding although ramping with and without bar gave me no more or less travel and I have a resonable amount of travel.
Somethings may work on paper but not on the car, other dont seem to work on paper but will give you enough of a result to improve a situation caused mods done to the car.
The first bar I made using falcon bushings and eyes and I elongated and finally ripped one open due to the force which would otherwise be on the springs, I have since machined thicker eyes and have had no problems (my housing has been strengthed aswell).
This works for me but every car is different and success to one may not be to another!
I found this site which shows some variations and has simple to understand explanations.
http://www.4x4wire.com/jeep/tech/susp/axlewrap/
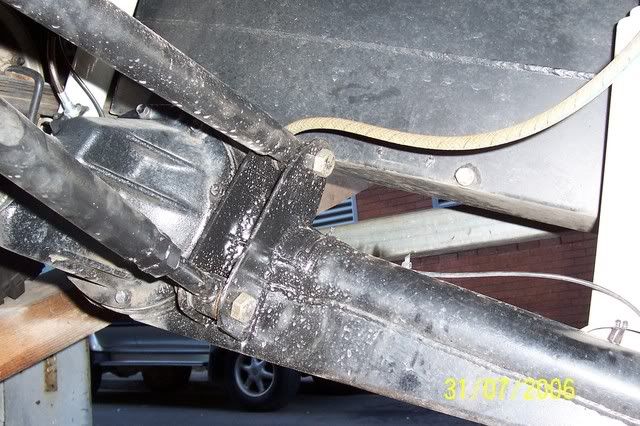
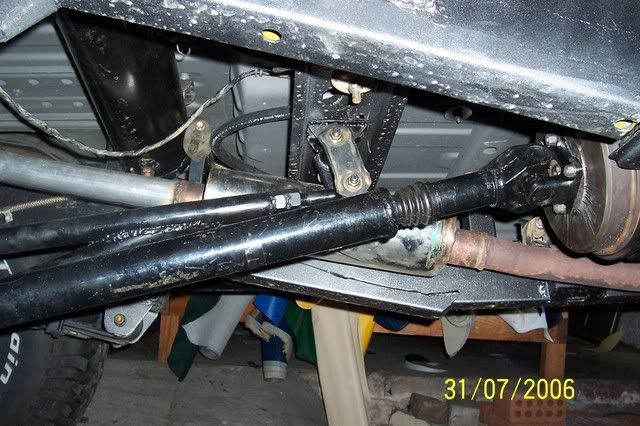
Somethings may work on paper but not on the car, other dont seem to work on paper but will give you enough of a result to improve a situation caused mods done to the car.
The first bar I made using falcon bushings and eyes and I elongated and finally ripped one open due to the force which would otherwise be on the springs, I have since machined thicker eyes and have had no problems (my housing has been strengthed aswell).
This works for me but every car is different and success to one may not be to another!
I found this site which shows some variations and has simple to understand explanations.
http://www.4x4wire.com/jeep/tech/susp/axlewrap/
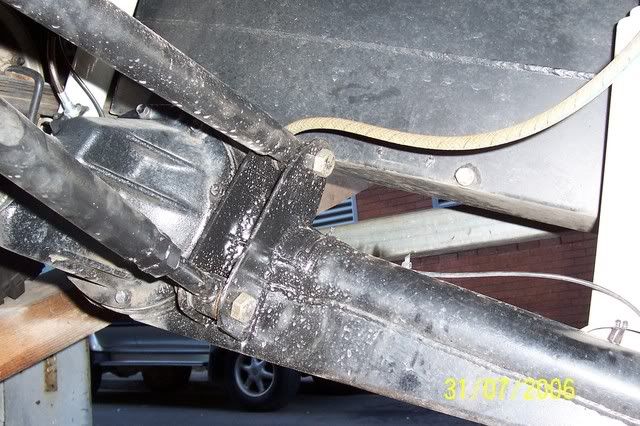
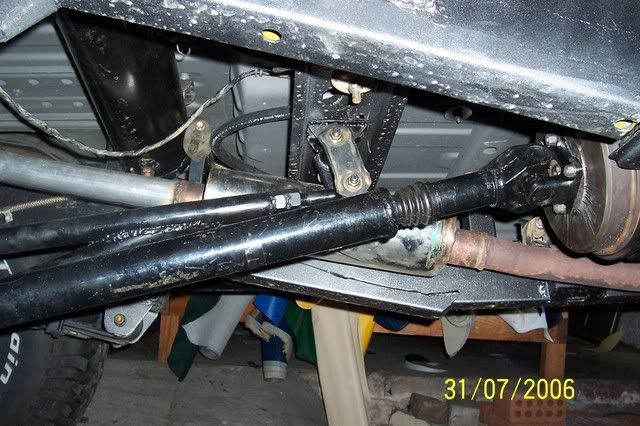
This has some pics of my Torque bar / anti wrap bar
I have finished the welding and put some black paint on it
works well but has a little slack in it which can make a loud knock sound
other then that it I am happy with it
Torque Bar http://www.outerlimits4x4.com/phpBB2/vi ... highlight=
I have finished the welding and put some black paint on it
works well but has a little slack in it which can make a loud knock sound
other then that it I am happy with it
Torque Bar http://www.outerlimits4x4.com/phpBB2/vi ... highlight=
God Of Emo
Posts: 7350
Joined: Sun Aug 24, 2003 7:04 pm
Joined: Sun Aug 24, 2003 7:04 pm
Location: Newy, home of the ZOOK (Rockin the 'diff)
Contact:
Have a good look under some of the Yank rigs, not all of them run track bars. Due to the weight of most of the big power full size rigs, they can run a much larger and higher rate spring pack, which helps with resisting wrap.11_evl wrote:
thats it. there must be a viable way to make it work as the yanks are 90% spoa and plenty of power.
Layto....
[quote="v840"]Just between me and you, I actually really dig the Megatwon, but if anyone asks, I'm going to shitcan it as much as possible! :D[/quote]
I swear last time I saw that trackbar of yours it wasn't that straighthyzook wrote:blah blah blha
http://www.4x4wire.com/jeep/tech/susp/axlewrap/
[im]http://i164.photobucket.com/albums/u30/ ... 0_0524.jpg[/img]
[im]http://i164.photobucket.com/albums/u30/ ... 0_0520.jpg[/img]


[url=http://www.4x4masters.com.au/]Australian 4X4 Masters Series website[/url]
non illegitimi carborundum!
[url=http://www.suzuki4wd.com.au/forum/]Suzuki 4wd Club of NSW forum[/url]
non illegitimi carborundum!
[url=http://www.suzuki4wd.com.au/forum/]Suzuki 4wd Club of NSW forum[/url]
11_evl wrote:changing unis is a pain.
i just assumed the us ones worked because there is SO many going spoa and are still spoa. its like the first mod they do
just searched and this is a torque fork.
That's a better picture than I had seen. Now I understand how it works it looks like a winner.
Steve.
[quote="greg"] some say he is a man without happy dreams, or that he sees silver linings on clouds and wonders why they are not platinum... all we know, is he's called the stevie.[/quote]
Thinking about it the shackle at the top has the same effect as an adjustable lower link. It allow the angle to change to suit the intitial setup and that's it. The distance between the two pivot points on the actual bar are set therefore for a particular shackle length there will only be two points, one each side of the line between the two centres that this setup will sit. Fixed shackle length, fixed diff mounting length (between centres).
Actually you'd be better off with an adjustable lower arm or you'd end up throwing out a lot of shackles getting it right.
Actually you'd be better off with an adjustable lower arm or you'd end up throwing out a lot of shackles getting it right.
;)
Whats the toughts on replacing bushings with heim joints. At the moment i have a shackle mounted off a crossmember and bushings on the diff end. There is some amount of slack due to the bushings so was thining heims would eliminate that and also would not limit flex.
Just thinking out loud.
Just thinking out loud.
Hardcore Wheelin' www.ozwheelers.net
- 94 Zuki - Lux diffs, SPOA, twin locked, 35's, 1.5" wheel spacers, exo, series 4 rockhoppers
- 94 Zuki - Lux diffs, SPOA, twin locked, 35's, 1.5" wheel spacers, exo, series 4 rockhoppers
No pictures yet. My original one is very similar to your drawing you posted MART. My second version will be the same but with hiems instead of bushes. I'll post up once i've sorted it out but wont be for a few weeks as i've got plenty of repairs to the drivetrain that need addressing before then.
Cheers Sanger
Cheers Sanger
Hardcore Wheelin' www.ozwheelers.net
- 94 Zuki - Lux diffs, SPOA, twin locked, 35's, 1.5" wheel spacers, exo, series 4 rockhoppers
- 94 Zuki - Lux diffs, SPOA, twin locked, 35's, 1.5" wheel spacers, exo, series 4 rockhoppers
I currently use a triangulated type like someone had posted a drawing of , this is the one offered by Breeze Industries in Canada . Excellent design and works great but can really shock load the driveline easily . It's triangulated design controls spring wrap nicely, haven't damaged a set of springs now for 4 years . The front section of it has a sliding tube that allows the rear axle to articulate without binding and can slide in and out to follow the uneven arc of the springs as they compress . The mount is a decent made crossmemeber that sits above the frame to clear the driveshaft and has a threaded head for the tri-arm to mount to with a bushing . It really needs a set of high durometer bushings at two mounting points at the rear axle , this would relieve the shock load against the axle housing . That's my only real complaint, despite truss work to the housing that trac bar has bent 2 housings now , one bad enough it wouldn't allow the lockrite to engage under a load .
Sarge
Sarge
Grab that bar, this is gonna hurt ....
Midwest Performance Parts
Weber tech/parts/service
Midwest Performance Parts
Weber tech/parts/service
im new to all this but would i hd sping pack in the centre of the diff work instead of a wrap bar. it would have the same arc of movement if u used same shackels and made the mounts in the same spot as originals.
It would take most of the weight of the back end so u could run softer packs in normal position and if u made the mount on the diff tilt from side to side it would not have that much affect on flex.a
It would take most of the weight of the back end so u could run softer packs in normal position and if u made the mount on the diff tilt from side to side it would not have that much affect on flex.a
1990 lwb vit
4 in lift
winch,lockers,gears, 31's
4 in lift
winch,lockers,gears, 31's
I get your idea, but bear in mind a sierra only runs 150lb/" rear springs.
Let's say one 150lb/" spring was run in the centre, and a 75lb/" spring at each side, rear roll stiffness would vanish, and the axle would want to pivot around the centre spring, both fore/aft and side to side. Cars with soft springs and a central track bar tend to do this a bit already.
this is almost the same idea as Land Rover used in the original Range Rover - the Boge Hydromat supported the weight of the car in the centre and the coils could then be very light.
however, with a coil design the links already control axlewrap.
Did I mention that SPUA cars don't really suffer from axlewrap?
Steve.
Let's say one 150lb/" spring was run in the centre, and a 75lb/" spring at each side, rear roll stiffness would vanish, and the axle would want to pivot around the centre spring, both fore/aft and side to side. Cars with soft springs and a central track bar tend to do this a bit already.
this is almost the same idea as Land Rover used in the original Range Rover - the Boge Hydromat supported the weight of the car in the centre and the coils could then be very light.
however, with a coil design the links already control axlewrap.
Did I mention that SPUA cars don't really suffer from axlewrap?

Steve.
[quote="greg"] some say he is a man without happy dreams, or that he sees silver linings on clouds and wonders why they are not platinum... all we know, is he's called the stevie.[/quote]
And a similar setup is used on the Trail Tough "bonz eye" springs that are designed for a SPOA application.
Steve.
Steve.
[quote="greg"] some say he is a man without happy dreams, or that he sees silver linings on clouds and wonders why they are not platinum... all we know, is he's called the stevie.[/quote]
Ok, here is what I am trying.
first some background for those that came in late (or have just forgotten), I have a 92 SWB Sierra, 1.6 Vit engine, 34" swampers, 5.125:1 diff gears and S3 transfer gears, it is SPOA with OME springs and I could bend a set of new springs into pretzels in one weekend if I so desired.
First was a single bar from the top of the diff to the body xmember above the transfer, this exacerbated the problem by massively dropping the pinion on acceleration and raising it on compression.
Second came the triangulated bar welded to the axle tube beside the centre and mounted to the body xmember with a rubber bushed suspension type shackle, this was better but still influenced the springs and ultimately was ripped off the axle tube by the forces generated.
This brings us to now.
I still have a triangulated bar with a rubber bushed shackle at the top but now it is attached to a chassis mounted xmember at the top and at the bottom it picks up the 4 right hand diff centre bolts (effectly making it heaps stronger and getting it almost to the centre line of the diff,
now here is the wacky bit (stick with me) instead of mounting the springs to the axle tube with U bolts (as per normal) I have made up a type of bearing block consisting of 2 aluminium cups that are bolted together with 6 cap screw and are fitted with a grease nipple that feeds grease in through a hole in the cap and is distributed inside the cap by several machined grooves, they have 4 studs at the top that mount the springs using fish plates, the bearing blocks are located lateraly on the axle tube by machined steel rings on either side.
The track bar doesnt influence the spring one bit, flex's well, handles fine and so far i have no negatives at all, but it is very early days and I am keeping a close eye on it.
I went this route in an attempt to counter the damaging effects of a standard track bar, I was not so concerned with squat and anti squat issues, just making my beloved leaf springs last.
Peter.
first some background for those that came in late (or have just forgotten), I have a 92 SWB Sierra, 1.6 Vit engine, 34" swampers, 5.125:1 diff gears and S3 transfer gears, it is SPOA with OME springs and I could bend a set of new springs into pretzels in one weekend if I so desired.
First was a single bar from the top of the diff to the body xmember above the transfer, this exacerbated the problem by massively dropping the pinion on acceleration and raising it on compression.
Second came the triangulated bar welded to the axle tube beside the centre and mounted to the body xmember with a rubber bushed suspension type shackle, this was better but still influenced the springs and ultimately was ripped off the axle tube by the forces generated.
This brings us to now.
I still have a triangulated bar with a rubber bushed shackle at the top but now it is attached to a chassis mounted xmember at the top and at the bottom it picks up the 4 right hand diff centre bolts (effectly making it heaps stronger and getting it almost to the centre line of the diff,
now here is the wacky bit (stick with me) instead of mounting the springs to the axle tube with U bolts (as per normal) I have made up a type of bearing block consisting of 2 aluminium cups that are bolted together with 6 cap screw and are fitted with a grease nipple that feeds grease in through a hole in the cap and is distributed inside the cap by several machined grooves, they have 4 studs at the top that mount the springs using fish plates, the bearing blocks are located lateraly on the axle tube by machined steel rings on either side.
The track bar doesnt influence the spring one bit, flex's well, handles fine and so far i have no negatives at all, but it is very early days and I am keeping a close eye on it.
I went this route in an attempt to counter the damaging effects of a standard track bar, I was not so concerned with squat and anti squat issues, just making my beloved leaf springs last.
Peter.
Cable bracing is the way of the future!
v840 said "That sounds like a booty fab, hack job piece of shit no offence."
v840 said "That sounds like a booty fab, hack job piece of shit no offence."
You know, that's not a bad idea allowing the axle to work semi-independent of the springs . This way, the axle cannot wreak havoc on the springs and allow the traction bar setup to take the full torque . Question is, can you mount the bar solid enough yet prevent shock loads? That is the biggest issue with tri bars, if you beef the mounting point enough to prevent spring and housing damage the gears and axles suffer instead .
Sarge
Sarge
Grab that bar, this is gonna hurt ....
Midwest Performance Parts
Weber tech/parts/service
Midwest Performance Parts
Weber tech/parts/service
Who is online
Users browsing this forum: No registered users and 5 guests