Notice: We request that you don't just set up a new account at this time if you are a previous user.
If you used to be one of our moderators, please feel free to reach out to Chris via the facebook Outerlimits4x4 group and he will get you set back up with access should he need you.
If you used to be one of our moderators, please feel free to reach out to Chris via the facebook Outerlimits4x4 group and he will get you set back up with access should he need you.
Recovery:If you cannot access your old email address and don't remember your password, please click here to log a change of email address so you can do a password reset.
I know they don't work but I am building one anyway, Thread
I must have missed this photo, keep a very close eye on your shackle mount as it WILL fatigue and pull away if your car gets much action.hyzook wrote:
Not meaning to offend you but looking the underside of your car, it doesnt look like it gets much of a thrashing so you may be OK.
Peter.
Cable bracing is the way of the future!
v840 said "That sounds like a booty fab, hack job piece of shit no offence."
v840 said "That sounds like a booty fab, hack job piece of shit no offence."
Hours of funfool_injected wrote:I swear last time I saw that trackbar of yours it wasn't that straighthyzook wrote:blah blah blha
http://www.4x4wire.com/jeep/tech/susp/axlewrap/
[im]http://i164.photobucket.com/albums/u30/ ... 0_0524.jpg[/img]
[im]http://i164.photobucket.com/albums/u30/ ... 0_0520.jpg[/img]![]()


droopypete wrote:hyzook wrote:
I must have missed this photo, keep a very close eye on your shackle mount as it WILL fatigue and pull away if your car gets much action.
Not meaning to offend you but looking the underside of your car, it doesnt look like it gets much of a thrashing so you may be OK.
Peter.
Thanks, to date I have not noticed any fatigue though I will keep an eye on this . Is this stated due to its particular design, i.e would you have done it different or due to normal forces placed upon it.
Oh and no offence taken, this pic was taken 1 week after the car was just built, (the body wax inside the rails is still yellow

hyzook wrote:droopypete wrote:hyzook wrote:
I must have missed this photo, keep a very close eye on your shackle mount as it WILL fatigue and pull away if your car gets much action.
Not meaning to offend you but looking the underside of your car, it doesnt look like it gets much of a thrashing so you may be OK.
Peter.
Thanks, to date I have not noticed any fatigue though I will keep an eye on this . Is this stated due to its particular design, i.e would you have done it different or due to normal forces placed upon it.
Oh and no offence taken, this pic was taken 1 week after the car was just built, (the body wax inside the rails is still yellow)
I did it exactly the same the first time around, it is almost a photo of my car (except for the yellow wax

and I ended up with vertical cracks on both sides of the cross member, that were repaired a few times, this time I have a new cross member.
Peter.
Cable bracing is the way of the future!
v840 said "That sounds like a booty fab, hack job piece of shit no offence."
v840 said "That sounds like a booty fab, hack job piece of shit no offence."
I'll keep an eye on this, thanks for the tipdroopypete wrote:hyzook wrote:droopypete wrote:hyzook wrote:
I must have missed this photo, keep a very close eye on your shackle mount as it WILL fatigue and pull away if your car gets much action.
Not meaning to offend you but looking the underside of your car, it doesnt look like it gets much of a thrashing so you may be OK.
Peter.
Thanks, to date I have not noticed any fatigue though I will keep an eye on this . Is this stated due to its particular design, i.e would you have done it different or due to normal forces placed upon it.
Oh and no offence taken, this pic was taken 1 week after the car was just built, (the body wax inside the rails is still yellow)
I did it exactly the same the first time around, it is almost a photo of my car (except for the yellow wax)
and I ended up with vertical cracks on both sides of the cross member, that were repaired a few times, this time I have a new cross member.
Peter.

Yeah Im as Droopypete has said pretty much onto my third bar now, first one was just week and ripped the thread out on the rose joint. Second one was okay still single bar new mountings and bigger rose joint it put pressure on my transfer case and I broke the mounts.
So now Im on the third one going a shackle welded on a box section that runs across the chassis bolted with 'U' bolts and also bolted to the body of my sierra as a rear floor support. Have made the top mount and run the top bar. As others have said the area to work in is just so small and running a longer bar is near on impossible, Im going to experiment with the new setup and the shackles to see if I can keep things from binding on full flex if not limit the flex before it gets to a certain point...?
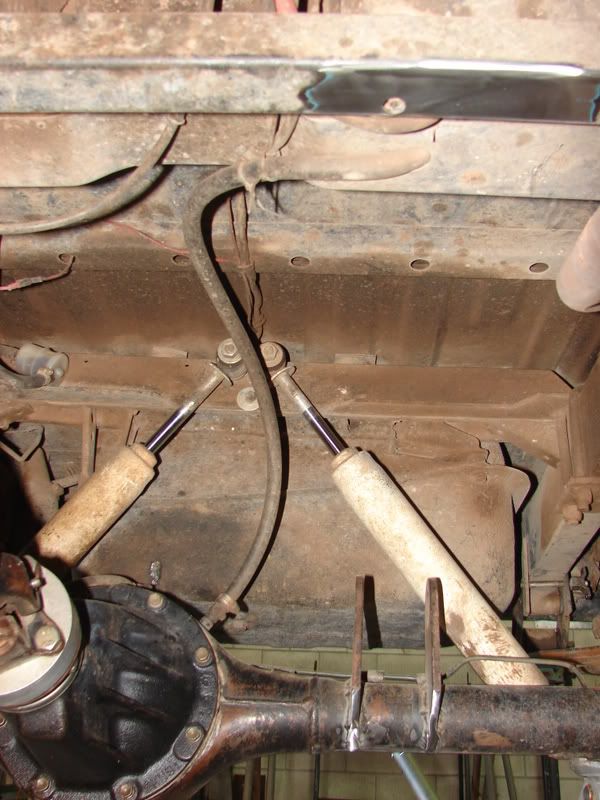
Have cut down combination of 80 series and Patrol panhard bars for the job.
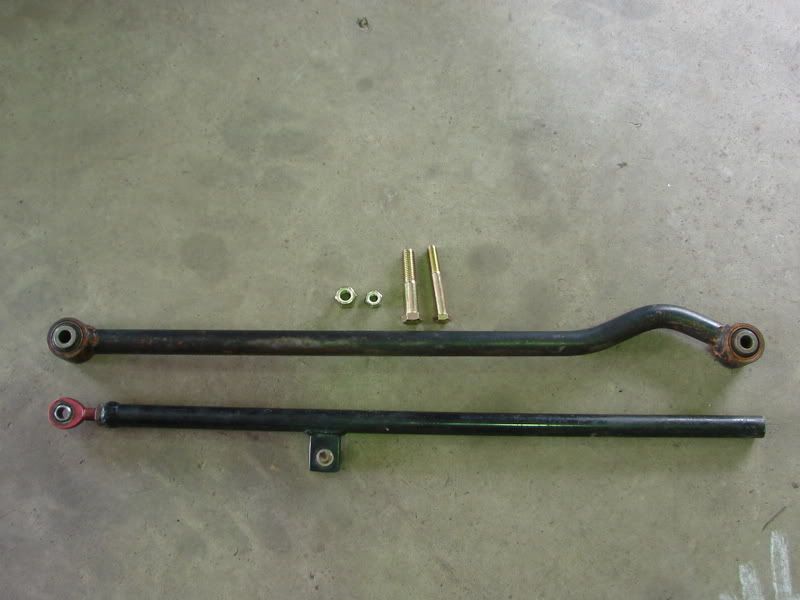
Not quite finished but will post when Im finished.
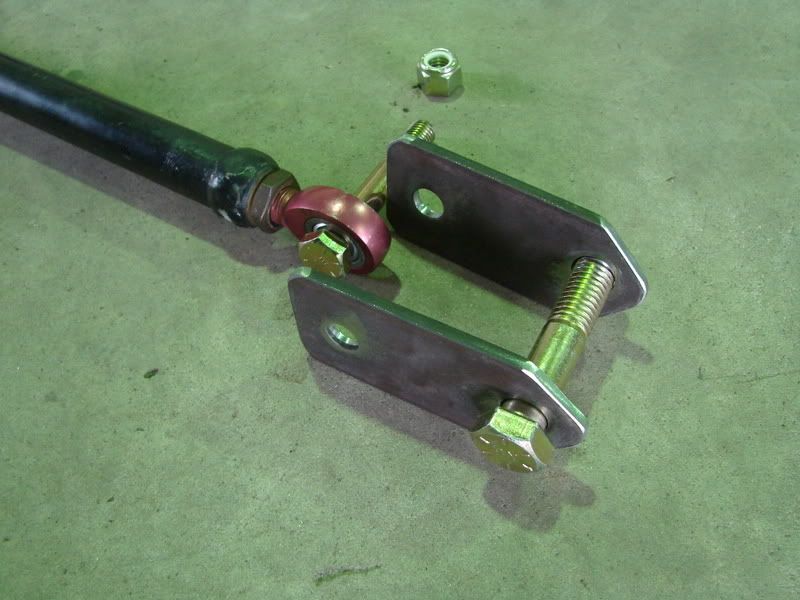
So now Im on the third one going a shackle welded on a box section that runs across the chassis bolted with 'U' bolts and also bolted to the body of my sierra as a rear floor support. Have made the top mount and run the top bar. As others have said the area to work in is just so small and running a longer bar is near on impossible, Im going to experiment with the new setup and the shackles to see if I can keep things from binding on full flex if not limit the flex before it gets to a certain point...?
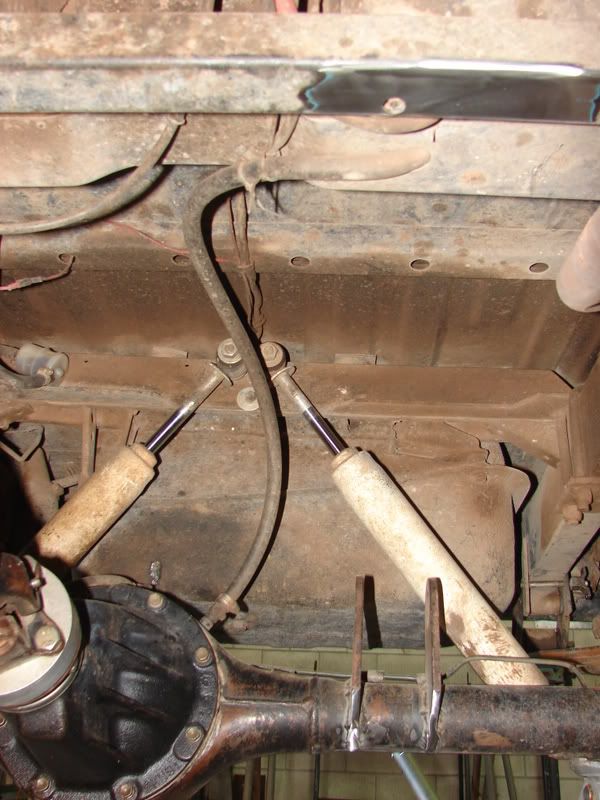
Have cut down combination of 80 series and Patrol panhard bars for the job.
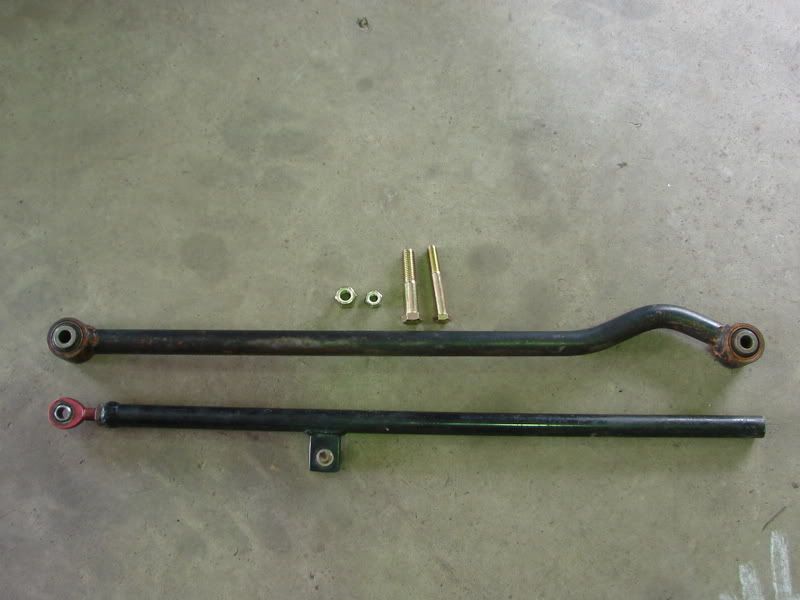
Not quite finished but will post when Im finished.
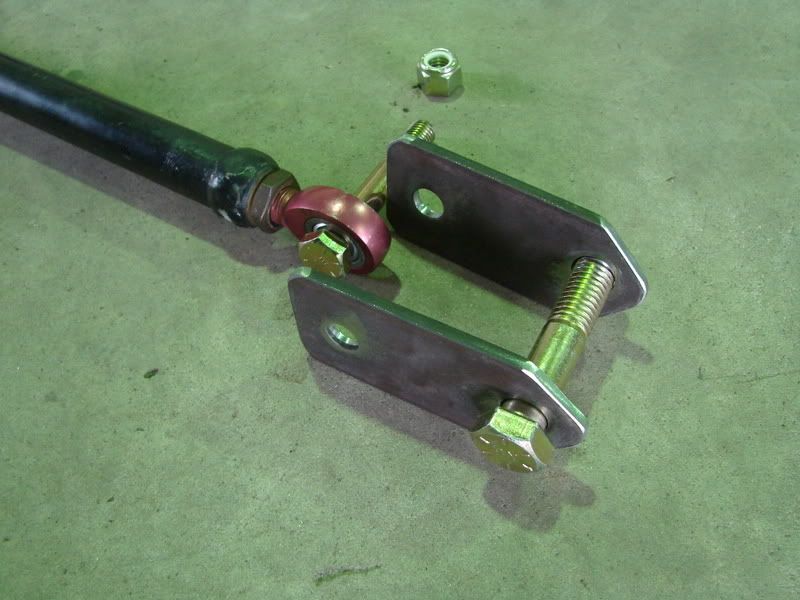
..wrench, wheel, wreck repeat..
check out the action @ http://www.darwin4x4.net
check out the action @ http://www.darwin4x4.net
when u do get that all braced up it will end up tearing a chunk out of your diff as the metal is too weak for the force you will be putting thru it at that pointMUD-PIGSIERRA wrote:Yeah Im as Droopypete has said pretty much onto my third bar now, first one was just week and ripped the thread out on the rose joint. Second one was okay still single bar new mountings and bigger rose joint it put pressure on my transfer case and I broke the mounts.
So now Im on the third one going a shackle welded on a box section that runs across the chassis bolted with 'U' bolts and also bolted to the body of my sierra as a rear floor support. Have made the top mount and run the top bar. As others have said the area to work in is just so small and running a longer bar is near on impossible, Im going to experiment with the new setup and the shackles to see if I can keep things from binding on full flex if not limit the flex before it gets to a certain point...?
just a thought as i happened to me
michael
Sadly this is correct MUD-PIGSIERRA, you will will be building your 4th one soon11_evl wrote: when u do get that all braced up it will end up tearing a chunk out of your diff as the metal is too weak for the force you will be putting thru it at that point
just a thought as i happened to me

Peter.
Cable bracing is the way of the future!
v840 said "That sounds like a booty fab, hack job piece of shit no offence."
v840 said "That sounds like a booty fab, hack job piece of shit no offence."
2 options Graham has already triedgreg wrote:or leave it parked in the shed... or sell it off...grimbo wrote:or you could just stay SPUA and not have to worry about these
both of these will elliviate your need to perform later repairs.


Peter.
PS, hi Greg
Cable bracing is the way of the future!
v840 said "That sounds like a booty fab, hack job piece of shit no offence."
v840 said "That sounds like a booty fab, hack job piece of shit no offence."
so anyway - bringing this back on topic.... lol
i have minor spring wrap under 1st and 2nd gear heavy acceleration, diff dips maybe 1" if im lucky but its enough to give vibrations....
anyone got a suggested style bar to remedy this??? Pics of the flex are in the link below. (thats not quite fully flexed either, still another 2" to go).
i have minor spring wrap under 1st and 2nd gear heavy acceleration, diff dips maybe 1" if im lucky but its enough to give vibrations....
anyone got a suggested style bar to remedy this??? Pics of the flex are in the link below. (thats not quite fully flexed either, still another 2" to go).
The worst thing about censorship is ███████.
Wheres the fun in that....? Though in taking on whats been said, Im only running 31"s my mount on the diff is on the axle tube and mounts around half the circumference of the axle tube, not of the side of the pumpkin......grimbo wrote:or you could just stay SPUA and not have to worry about these


Maybe Ill add some extra gusseting while im at it...

..wrench, wheel, wreck repeat..
check out the action @ http://www.darwin4x4.net
check out the action @ http://www.darwin4x4.net
Anyone seen or have or heard about the sky bolt on traction bar....? Our Dollar is buying about .92c US at the mom maybe its the go.....?:?


On another note I need to run one as a part of my registration, I also have to run a front Panhard bar as well so having something that works


On another note I need to run one as a part of my registration, I also have to run a front Panhard bar as well so having something that works
..wrench, wheel, wreck repeat..
check out the action @ http://www.darwin4x4.net
check out the action @ http://www.darwin4x4.net
I dont mean to have a go, but the more weld you put into the tube the more it will let go.MUD-PIGSIERRA wrote:Wheres the fun in that....? Though in taking on whats been said, Im only running 31"s my mount on the diff is on the axle tube and mounts around half the circumference of the axle tube, not of the side of the pumpkin......grimbo wrote:or you could just stay SPUA and not have to worry about theseSo yeah Ill post up some pics when i get to build number 4 then........
Maybe Ill add some extra gusseting while im at it...
Peter.
Cable bracing is the way of the future!
v840 said "That sounds like a booty fab, hack job piece of shit no offence."
v840 said "That sounds like a booty fab, hack job piece of shit no offence."
[quote="Larry the Leper"]Hello Senor Pete,
You could also ditch the Sierra and go get a real one like my Disco!!
It has it's own coils as standard!!!!!!!!
[/quote]
I don't know what is funnier,
the fact that you posted that
or that you actualy beleive it!
Peter.


You could also ditch the Sierra and go get a real one like my Disco!!
It has it's own coils as standard!!!!!!!!

I don't know what is funnier,
the fact that you posted that
or that you actualy beleive it!
Peter.
























































































































































































































































































































































































































































































































































































































































































































































































































































































































































































































































































































Cable bracing is the way of the future!
v840 said "That sounds like a booty fab, hack job piece of shit no offence."
v840 said "That sounds like a booty fab, hack job piece of shit no offence."
I agree, but there seems to be some nuts inside the bracket, perhaps indicating a u bolt around the axle tube or similar, this would do very little to combat rotational force on the tube but would sure help in preventing the thing being peeled off the diff centre.alien wrote: my only concern would be the force applied to the housing through those screws...
Peter.
Cable bracing is the way of the future!
v840 said "That sounds like a booty fab, hack job piece of shit no offence."
v840 said "That sounds like a booty fab, hack job piece of shit no offence."
yeah i checked the site - its Ubolted on there... i suppose tabs could be welded to the housing next to the Ubolts to stop it rotating... unless theyre welding perches to the diff for the u-bolts?
Anyone got better images of this bar??? im quite interested....
Anyone got better images of this bar??? im quite interested....
The worst thing about censorship is ███████.
Well I guess the hole would be bigger. I don't want to come across as ignorant as to the pics and the experience everyone has contributed, but if your doing a fillet weld to a area in length of say of of 2"inches and then compare that to the same situation but weld 4" inches your spreading the area in which the load is transferred too, therefore reducing your chance of breakage...?droopypete wrote: I dont mean to have a go, but the more weld you put into the tube the more it will let go.
Peter.
..wrench, wheel, wreck repeat..
check out the action @ http://www.darwin4x4.net
check out the action @ http://www.darwin4x4.net
I'm new to welding, still almost virginal.MUD-PIGSIERRA wrote:Well I guess the hole would be bigger. I don't want to come across as ignorant as to the pics and the experience everyone has contributed, but if your doing a fillet weld to a area in length of say of of 2"inches and then compare that to the same situation but weld 4" inches your spreading the area in which the load is transferred too, therefore reducing your chance of breakage...?droopypete wrote: I dont mean to have a go, but the more weld you put into the tube the more it will let go.
Peter.
But what I understand is: longer welding time, larger area = more heat to the metal, thus increasing the chance of weakening the metal itself, not the weld? Tho an expert would know how to avoid that prob.
But I could be talkin from me bumm

christover
4WD SUZUKI CLUB VICTORIA
http://www.vic.suzuki4wd.com/forum/
http://www.vic.suzuki4wd.com/forum/
Yeah not putting to much heat into the area you weld, so doing small sections of at a time, how much you heat the object your welding to before you weld. How you cool it after its finished. Can all effect how it turns out.
..wrench, wheel, wreck repeat..
check out the action @ http://www.darwin4x4.net
check out the action @ http://www.darwin4x4.net
Re: I know they don't work but I am building one anyway, Thr
How is all this going Droopy.....? Come on get some pics up for us all I want to sort out mine and need some ideas....droopypete wrote: so I am onto the mach 3.
I will post some pics as I go and you can hang shyte on my welds![]()
Peter.

..wrench, wheel, wreck repeat..
check out the action @ http://www.darwin4x4.net
check out the action @ http://www.darwin4x4.net
Just put a vertical plate (running along the top of the axle tube) 200 or 300mm long or whatever - cut the corners off to make it look pretty - thats welded behind the 2 vertical bush mounting plates in your picture.MUD-PIGSIERRA wrote:Yeah not putting to much heat into the area you weld, so doing small sections of at a time, how much you heat the object your welding to before you weld. How you cool it after its finished. Can all effect how it turns out.
Then do the same sort of thing on the front edge of the 2 vertical bush mounting plates to pick up 200 to 300mm of the bottom of the axle tube. This plate will have to be notched to clear the lower traction bar mount.
So now instead of the 2 vertical mounting trying to rip out 75mm of axle tube it will have to rip out 300mm of axle tube.
Edit - here is a dodgy arse picture...

Sam
Hey Strange Rover... LoL I like your dodgy picture it looks good, I guess the more contact area the better chance of it not self destructing... And well if it does I guess its time for Patrol diffs or something...
A friend and I are part of the recovery crew up here for the Mud racing and on the weekend was the finals and I had the chance to check out the suspension setups of the Open class racers, now these are guys running Nitrous nothing smaller than 350ci Chevs and what not, hell one of them is a 460 race motor from the states, yet most are still fairly standard running gear but one had two control arms running from the top of the pumpkin no gusseting or anything and these guys go hard all I can assume is that either these diff housings are alot thicker or they have really well thought out suspension setups....?
A friend and I are part of the recovery crew up here for the Mud racing and on the weekend was the finals and I had the chance to check out the suspension setups of the Open class racers, now these are guys running Nitrous nothing smaller than 350ci Chevs and what not, hell one of them is a 460 race motor from the states, yet most are still fairly standard running gear but one had two control arms running from the top of the pumpkin no gusseting or anything and these guys go hard all I can assume is that either these diff housings are alot thicker or they have really well thought out suspension setups....?
..wrench, wheel, wreck repeat..
check out the action @ http://www.darwin4x4.net
check out the action @ http://www.darwin4x4.net
Who is online
Users browsing this forum: No registered users and 6 guests