Notice: We request that you don't just set up a new account at this time if you are a previous user.
If you used to be one of our moderators, please feel free to reach out to Chris via the facebook Outerlimits4x4 group and he will get you set back up with access should he need you.
If you used to be one of our moderators, please feel free to reach out to Chris via the facebook Outerlimits4x4 group and he will get you set back up with access should he need you.
Recovery:If you cannot access your old email address and don't remember your password, please click here to log a change of email address so you can do a password reset.
quick relay question
Moderator: -Scott-
quick relay question
im "bettering" the positive wires to my spotties coz the person who did it did a crap job as the wires be used have a decent voltage drop and are too thin. i need to also get another relay as the wires are stuck in the relay plug so my question is: do some relays give a better voltage boost than others? if so, which ones kick arse. atm it is a ipf relay and it seems ok.
1993 LWB vitara, Front & Rear alloy bars, towbar, spotties, UHF.
what do you mean "voltage boost"??
with a relay you should just have the right guage cable from your power source to the relay and then on the other side to your spotties or whatever.
just use a regular 40 or 50A relay and decent cable and you should be fine.
also solder the terminals on if possible.
the guy at ARB who wired my spotties up (previous owner) did a crappy job on crimping and they ended up melting when i was in the middle of nowhere
so as soon as i got home i removed it all and ran my own wires and soldered everything
with a relay you should just have the right guage cable from your power source to the relay and then on the other side to your spotties or whatever.
just use a regular 40 or 50A relay and decent cable and you should be fine.
also solder the terminals on if possible.
the guy at ARB who wired my spotties up (previous owner) did a crappy job on crimping and they ended up melting when i was in the middle of nowhere

so as soon as i got home i removed it all and ran my own wires and soldered everything
my GUBanzy wrote:Dial up internet.........you'd post something and come back 2 beers later to see if it loaded.
yeah did it all yesterday, soldered everything exept the solder wouldnt stick to most to the older wires so had to make it thick to work. i was thinking it must not solder well because it seemed to be burnt from the high current going throught over time or maybe just old age.
my new wires are now shorter and the correct gauge and soldered and it seems to produce a brighter light in my garage but haven't had time to go out and drive it at night yet.
my new wires are now shorter and the correct gauge and soldered and it seems to produce a brighter light in my garage but haven't had time to go out and drive it at night yet.
1993 LWB vitara, Front & Rear alloy bars, towbar, spotties, UHF.
Those wires would have oxidation on the strands. You can dip the striped wire in mild acid or use flux paste that cleans as it heats.gumtree wrote:exept the solder wouldnt stick to most to the older wires
If you don't have the acid or flux stuff, then use emery paper to make the strands shiny before soldering!
I'm the sharpest tool in the shed!
A well produced soldered joint is very reliable but a few things to watch...
1/ Solder has approx. seven times the volume resistivity of copper so you need a decent length of soldered lug to produce a low resistance joint.
2/ Solder can easily "wick" back up under the insulation making stranded cable brittle.
3/ Flux that is not completely removed can cause corrosion problems down the track.
IMO theres little difference in reliability between GOOD crimped and soldered connections, but with the right lugs and crimp tools crimping is far easier. I HATE the spade style lugs with the insulated sleeves - they are much more difficult to crimp properly.
1/ Solder has approx. seven times the volume resistivity of copper so you need a decent length of soldered lug to produce a low resistance joint.
2/ Solder can easily "wick" back up under the insulation making stranded cable brittle.
3/ Flux that is not completely removed can cause corrosion problems down the track.
IMO theres little difference in reliability between GOOD crimped and soldered connections, but with the right lugs and crimp tools crimping is far easier. I HATE the spade style lugs with the insulated sleeves - they are much more difficult to crimp properly.
( usual disclaimers )
It seemed like a much better idea when I started it than it does now.
It seemed like a much better idea when I started it than it does now.
How about this, - I heat and fill the hole in the lug with solder, then I "tin" the fresh shiny copper strands with solder, then I mate the 2 by heating and inserting the wire into the lug.MightyMouse wrote:I HATE the spade style lugs with the insulated sleeves - they are much more difficult to crimp properly.
How good is that?
I'm the sharpest tool in the shed!
Yes, unfortunately the insulated ones are almost universal nowadays.macca81 wrote:where do you get said lugs? all the ones i have seen are insulated...MightyMouse wrote: I HATE the spade style lugs with the insulated sleeves - they are much more difficult to crimp properly.
I get my bare lugs from a autoelectrical shop by the box ( Utilux ).
They aren't cheap by the box but you get a lot - a thousand or so......
The proper crimp tool is also very important, the ones that simply squeeze the lug aren't good IMO - a proper tool folds and crimps the lug. Look at a factory spade connector and you will immediately see the difference.
v6hilux - done properly your method will produce good connections - still watch the "wicking" effect and flux removal.
I can understand why people solder lugs as so many poor crimps are produced using those insulated lugs and crappy crimp tools.
( usual disclaimers )
It seemed like a much better idea when I started it than it does now.
It seemed like a much better idea when I started it than it does now.
Sorry but that's not always correct.ausoops wrote:the only difference between a soldered and a crimped connection is the mechanical strength of the joint, electrically they will be the same.
Solder has around seven times the volume resistivity of copper, so depending on the design of a solder joint it can have a lower conductivity than a good crimp.
You obviously need a soldered contact area of seven times the cables cross sectional area to ensure the solder has the same effective resistance as the cable.
Like I stated earlier theres nothing between GOOD soldered and crimped connections but each have to correctly designed and performed.
( usual disclaimers )
It seemed like a much better idea when I started it than it does now.
It seemed like a much better idea when I started it than it does now.
This is getting ridiculous!
A panel beater told me once he had problems with solder joints he did and will always crimp instead. Now, how do we measure his abilities with a soldering iron!
Two clean and shiny copper stranded wires twisted tightly together have the ultimate contact. Then you heat it up and solder the joint. How is any corrosion or resistance of solder ever going to reduce the quality of that joint, unless you solder like my panel beater mate did! There is no air getting to the copper under the solder.
A panel beater told me once he had problems with solder joints he did and will always crimp instead. Now, how do we measure his abilities with a soldering iron!
Two clean and shiny copper stranded wires twisted tightly together have the ultimate contact. Then you heat it up and solder the joint. How is any corrosion or resistance of solder ever going to reduce the quality of that joint, unless you solder like my panel beater mate did! There is no air getting to the copper under the solder.
I'm the sharpest tool in the shed!
Why is it? At least the panel beater is on the right track. Soldering is always my last choice for joining cables, mostly due to reliability. You can theorize all you like, but i have numerous years experience as an Electrician and a lot of that has been working around all kinds of large mobile equipment, from Drag Lines to Trains. When an issue was caused by a poor connection, it was typically always a soldered joint.v6hilux wrote:This is getting ridiculous!
Crimping is always the first option, the only problem with crimping is it's more costly to set yourself up with all the right tools.
If God did not intend for us to eat animals, then why did he make them out of meat?
A poor crimp won't be any more reliable than a poor solder joint - and that's the key, the quality of the process.
The heat of soldering affects the copper, making it more brittle and prone to fracturing. This is probably a significant contributor to the reliability problems on mobile equipment - at the very least, the solder joint shouldn't be subject to any mechanical stress (i.e. tension on the wire.)
Cleaning is also important with soldering - before the joint is made, and after. Don't do it properly and what appears to be a good joint can eventually fail.
With the right tools crimp joints are faster, easier and 100% reliable. Without the right tools, crimping can be very hit and miss - and I'd prefer to solder.
The heat of soldering affects the copper, making it more brittle and prone to fracturing. This is probably a significant contributor to the reliability problems on mobile equipment - at the very least, the solder joint shouldn't be subject to any mechanical stress (i.e. tension on the wire.)
Cleaning is also important with soldering - before the joint is made, and after. Don't do it properly and what appears to be a good joint can eventually fail.
With the right tools crimp joints are faster, easier and 100% reliable. Without the right tools, crimping can be very hit and miss - and I'd prefer to solder.
X2-Scott- wrote:Solder & heatshrink.
If you want a method, place heat shrink on one wire, strip the 2 wires, push the strands toward each other, but don't overlap the insulation, (like head-on), give the joint a twist to tight0en it up, solder away, shrink the heat shrink.

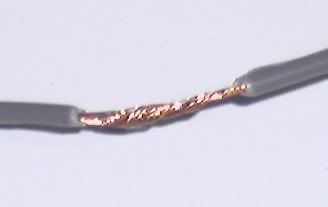
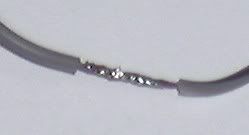
The trick is to avoid movement with the wires while the solder is hot and to heat the strands till it's hot enough for the strands to melt the solder, not the iron, then just let it flow into the strands.
I'm the sharpest tool in the shed!
Depends on the situation. Typically a correct sized barrel connector with the correct calibrated crimper (the important bit), then if it needs sealing, some rubber splicing tape to cover.chimpboy wrote:What method do you guys prefer for joining wires? ie no terminal, just joining two pieces to make a continuous length.
If God did not intend for us to eat animals, then why did he make them out of meat?
There are very good reasons that the electrical and automotive industry uses crimp and screw connections for the vast majority of it connections - that is its basically more reliable / quicker / low resistance.
This assumes however that the correct parts and crimpers are used - which is rarely the case with the generic auto crimp tools.
Once again a properly produced soldered joint is very reliable, but it takes far more skill, equipment and time to get it right. I have a "High Reliability Hand Soldering" qualification and its a painfully slow process to produce connections to the standard required.
Having the correct tools and lugs, I crimp - not because its the only solution, mostly because its faster.
This assumes however that the correct parts and crimpers are used - which is rarely the case with the generic auto crimp tools.
Once again a properly produced soldered joint is very reliable, but it takes far more skill, equipment and time to get it right. I have a "High Reliability Hand Soldering" qualification and its a painfully slow process to produce connections to the standard required.
Having the correct tools and lugs, I crimp - not because its the only solution, mostly because its faster.
( usual disclaimers )
It seemed like a much better idea when I started it than it does now.
It seemed like a much better idea when I started it than it does now.
Cool, that is exactly what I do but I wondered if I should be doing something else, after reading all the abovev6hilux wrote:X2-Scott- wrote:Solder & heatshrink.
If you want a method, place heat shrink on one wire, strip the 2 wires, push the strands toward each other, but don't overlap the insulation, (like head-on), give the joint a twist to tight0en it up, solder away, shrink the heat shrink.
The trick is to avoid movement with the wires while the solder is hot and to heat the strands till it's hot enough for the strands to melt the solder, not the iron, then just let it flow into the strands.

This is not legal advice.
Crimp it, it will be more reliable than soldering.I should be doing something else,
Why, solder joins as above in vechiles are prone to fraying. The solder is very rigid and movment in the cable will cause cracking at the egde of the joint. Heatshrink wont offer any additional strenght unless you use 3 or 4 layers.
RB
ONLY if you have decent crimp tools, AND you know how to use them.Rascal wrote:Crimp it, it will be more reliable than soldering.I should be doing something else,
Which is why it's important to ensure soldered joints are not mechanically stressed.Rascal wrote:Why, solder joins as above in vechiles are prone to fraying. The solder is very rigid and movment in the cable will cause cracking at the egde of the joint.
Yes. I only mentioned heatshrink for insulation. I try to avoid insulation tape, I use it only when heatshrink is impractical (or not available.)Rascal wrote:Heatshrink wont offer any additional strenght unless you use 3 or 4 layers.
Anyway, I think it's important to stress the quality aspect in this argument.
Yes, crimp joints are perfectly reliable and acceptable, with none of the "down side" of solder joints - if done properly. Cheap automotive crimp connectors crimped with cheap crimp tools onto improperly sized wire are a reliability problem in the making - just like poor solder joints.
Heating copper anneals it, making it more flexible and less likely to kink or fracture. Bending annealed copper, cause the reverse. It becomes stiff and can cause it to fracture.-Scott- wrote:The heat of soldering affects the copper, making it more brittle and prone to fracturing. This is probably a significant contributor to the reliability problems on mobile equipment
-Scott- wrote:at the very least, the solder joint shouldn't be subject to any mechanical stress (i.e. tension on the wire.
So you guys are saying there is no hard point in the wire that is crimped?Rascal wrote: solder joins as above in vechiles are prone to fraying. The solder is very rigid and movment in the cable will cause cracking at the egde of the joint.
The point where the wire exits the crimped lug is going to be subject to the exact same forces as the point where the solder in a wire joint ends.
Both correctly crimped and soldered wire connectors suffer the same effects of fracturing from movement, unless there is some type of flexible crimp available I don't know about.
I think we are all missing the point - crimped or soldered wires in an automotive situation should be cable tied or taped to some supporting device the closest wiring loom on either side of the joint!
I'm the sharpest tool in the shed!
Very Very true - unsupported or mechanically stressed wiring and connections are just asking for trouble.v6hilux wrote:crimped or soldered wires in an automotive situation should be cable tied or taped to some supporting device the closest wiring loom on either side of the joint!
On the subject of flexibility, wicking of solder back up under the cables insulation promotes stress fractures in multistrand cables. High Reliability Soldering uses "Anti Wicking Tweezers" to prevent this effect.
By soldering you effectively create a solid cable out of multistrand one which is significantly less flexible than a comparable multistrand cable. So a crimped connection and a soldered one will "flex" from the same point but the strands of the multistrand cable will make it more flexible and less prone to fracture at the joint.
( usual disclaimers )
It seemed like a much better idea when I started it than it does now.
It seemed like a much better idea when I started it than it does now.
Who is online
Users browsing this forum: No registered users and 1 guest