Notice: We request that you don't just set up a new account at this time if you are a previous user.
If you used to be one of our moderators, please feel free to reach out to Chris via the facebook Outerlimits4x4 group and he will get you set back up with access should he need you.
If you used to be one of our moderators, please feel free to reach out to Chris via the facebook Outerlimits4x4 group and he will get you set back up with access should he need you.
Recovery:If you cannot access your old email address and don't remember your password, please click here to log a change of email address so you can do a password reset.
Trailer construction question
Moderators: toaddog, TWISTY, V8Patrol, Moderators
Trailer construction question
Im about to start building a 7x5 bow trailer that will double up as a camper trailer, It is just going to be a short distance touring camper and will see no harder trails then dirt roads. I am going to build the main frame out of 75x50mm steel section (habent decided on wall thickness yet).
The main question is can i have the main side rails and Aframe sections in one piece per side by cutting a notch out bend and re-weld the length together again?
The main question is can i have the main side rails and Aframe sections in one piece per side by cutting a notch out bend and re-weld the length together again?
Its not cool, unless it's got boost :)
sounds a bit sketchy to me. im not 100% sure but i think a certain % of the draw bar has to continue under the chassis. but i could be wrong. maybe the draw bar cant exceed a % of the length of the chassis...
normally the draw bar attaches at two points under the chassis, so load is spread over say a 30cm length between the two welded points.
with what your suggesting the load is all transfered through the welds. this is probably ok if your welding is 100%, but any kind of fault could see stress and failure in a bad way on a rough dirt road. plus campers carry a bit of weight. you would also need to use a thicker and heavier wall to achieve this making the material more expensive and the trailer heavy.
it might be possible if the welds were x rayed etc but not worth the effort. trailers are made a certain way for a reason, it works.
On another note if your making the chassis out of 50 x 75 rhs, then it will be a very tough chassis, far superior to any of the rubbish made as the average box trailer, why then make a dodgy draw bar?
most basic trailers are made from angle for the chassis - the good ones are 50 x 50 shs, then the draw bar 50 x 75 or 100.
my 2c
normally the draw bar attaches at two points under the chassis, so load is spread over say a 30cm length between the two welded points.
with what your suggesting the load is all transfered through the welds. this is probably ok if your welding is 100%, but any kind of fault could see stress and failure in a bad way on a rough dirt road. plus campers carry a bit of weight. you would also need to use a thicker and heavier wall to achieve this making the material more expensive and the trailer heavy.
it might be possible if the welds were x rayed etc but not worth the effort. trailers are made a certain way for a reason, it works.
On another note if your making the chassis out of 50 x 75 rhs, then it will be a very tough chassis, far superior to any of the rubbish made as the average box trailer, why then make a dodgy draw bar?
most basic trailers are made from angle for the chassis - the good ones are 50 x 50 shs, then the draw bar 50 x 75 or 100.
my 2c
*there's a rock, drive over it :) there's a bigger rock, drive over it :twisted: there's an even bigger rock, oops broke it :oops: Upgrade broken bit :bad-words:
Goto *
Goto *
Thats a good point you have made, i was looking at the section size i mentioned because of the way i was thinking of designing it. If i go the standard way i was going to use 50x50 for the frame and 75x50 for the Aframe.thehanko wrote:sounds a bit sketchy to me. im not 100% sure but i think a certain % of the draw bar has to continue under the chassis. but i could be wrong. maybe the draw bar cant exceed a % of the length of the chassis...
normally the draw bar attaches at two points under the chassis, so load is spread over say a 30cm length between the two welded points.
with what your suggesting the load is all transfered through the welds. this is probably ok if your welding is 100%, but any kind of fault could see stress and failure in a bad way on a rough dirt road. plus campers carry a bit of weight. you would also need to use a thicker and heavier wall to achieve this making the material more expensive and the trailer heavy.
it might be possible if the welds were x rayed etc but not worth the effort. trailers are made a certain way for a reason, it works.
On another note if your making the chassis out of 50 x 75 rhs, then it will be a very tough chassis, far superior to any of the rubbish made as the average box trailer, why then make a dodgy draw bar?
most basic trailers are made from angle for the chassis - the good ones are 50 x 50 shs, then the draw bar 50 x 75 or 100.
my 2c
I understnd the stress of my origanial thought and if it was a ok way to do it i would have got the lengths professionally notched and welded.
Its not cool, unless it's got boost :)
just trailers make thier trailers by press bending the a frame at the front corners of the box and continuing the RHS down the side of thra trailer. about 50x50 rhs from memory.MARKx4 wrote:Thats a good point you have made, i was looking at the section size i mentioned because of the way i was thinking of designing it. If i go the standard way i was going to use 50x50 for the frame and 75x50 for the Aframe.thehanko wrote:sounds a bit sketchy to me. im not 100% sure but i think a certain % of the draw bar has to continue under the chassis. but i could be wrong. maybe the draw bar cant exceed a % of the length of the chassis...
normally the draw bar attaches at two points under the chassis, so load is spread over say a 30cm length between the two welded points.
with what your suggesting the load is all transfered through the welds. this is probably ok if your welding is 100%, but any kind of fault could see stress and failure in a bad way on a rough dirt road. plus campers carry a bit of weight. you would also need to use a thicker and heavier wall to achieve this making the material more expensive and the trailer heavy.
it might be possible if the welds were x rayed etc but not worth the effort. trailers are made a certain way for a reason, it works.
On another note if your making the chassis out of 50 x 75 rhs, then it will be a very tough chassis, far superior to any of the rubbish made as the average box trailer, why then make a dodgy draw bar?
most basic trailers are made from angle for the chassis - the good ones are 50 x 50 shs, then the draw bar 50 x 75 or 100.
my 2c
I understnd the stress of my origanial thought and if it was a ok way to do it i would have got the lengths professionally notched and welded.
admittadely they are a light 6x4 trailer, but it shows it is done commercially.
if you could press bend some 70x50 youd probably have enough strength, and you gain a little bit of hight by not having the aframe under the box frame.
Re: Trailer construction question
This makes sense to me except i would only 50x50 as 75x50 is overkill unless it was dual axle or for heavy loads, 1 change i would make is to make the drawbar come from about the centre of the axle out thru the middle of the A frame and then mount the coupling to that ?MARKx4 wrote:Im about to start building a 7x5 bow trailer that will double up as a camper trailer, It is just going to be a short distance touring camper and will see no harder trails then dirt roads. I am going to build the main frame out of 75x50mm steel section (habent decided on wall thickness yet).
The main question is can i have the main side rails and Aframe sections in one piece per side by cutting a notch out bend and re-weld the length together again?
Saddle up tonto, its the not so loanrangie! . 98 TDI DISCO lightly modded with more to come.
id say 75 x 50 as your minimum with a gusset across the bend/cut.
reason is 50 x 50 may be fine on a well loaded properly balanced trailer and rig, but how many of us have seen a badly or overloaded tralier behind a overloaded rig? And then there is the day its a bit heavy on the front or rear and you hit that foot deep hole on the side of our fantasticly maintained roads is AUS.
I reccon 75 x 50 up to 1500 - 1800 kg and 100 x 50 over that.
and yes ive built a few trailers in my time.
reason is 50 x 50 may be fine on a well loaded properly balanced trailer and rig, but how many of us have seen a badly or overloaded tralier behind a overloaded rig? And then there is the day its a bit heavy on the front or rear and you hit that foot deep hole on the side of our fantasticly maintained roads is AUS.
I reccon 75 x 50 up to 1500 - 1800 kg and 100 x 50 over that.
and yes ive built a few trailers in my time.
85 high roof 1.3, 6.5 tc, air lockers,ruf and 34 swampers. yep its an ugly pos.
Just to add my 2 cents worth. I have built quiet a few trailers over the last 20 years. 50 x 50 frame and 75 x 50 draw bar is more than you will ever need, I have never gone this big. Weld your draw bar just behind center/axel (50mm). Make sure your axle is just behind center. Make your draw bar as long as you need the longer the better will make reversing easyer. Measure from end of wheel stubs to hitch and make sure they are exatly the same. (to the millimetre). This will be easier to tow and reverse.
4x4 Addict. 2002 Patrol, 1977 Fj45, 1975 Fj40, 1993 Vitara, 1983 Sierra Off Road Buggy
That is where i wanted to start, that way i have a one peice side rail the full length of the trailer. Thanks for the draw bar length, i was stumped on what length to go.Skegbudley wrote:1.5 - 1.8m for the draw bar from front edge of box to end of draw bar not including hitch.
Start the bend at the front edge of the box.
Its not cool, unless it's got boost :)
Thats @ 90 degrees to the front of box, not the length of the bar from the front of box to the end of draw bar. (just to make sure. hehe.
)
As for suspension and axles. Go for a braked setup. You wont regret it. Here a site that will be helpful. These guys are just up the road from me and have a good reputation. Good prices too.
http://www.etrailerparts.com.au/index1. ... tus.html&1
Running the 100x50 rails (with 50x50 cross bars) all the way to the back provides a strong base to work with. The rear works a a slider too instead of hitting a stop (cross bar support or similar.) as with most trailers on the market.
Since you are building this from scratch. There is bugger all difference in cost in making it bulletproof so to speak. Here's a few pics of my chassis.
Use a 50x50 across the middle of draw bar to reinforce as well as providing strong base for chest, esky (75L on mine), bikes, etc.
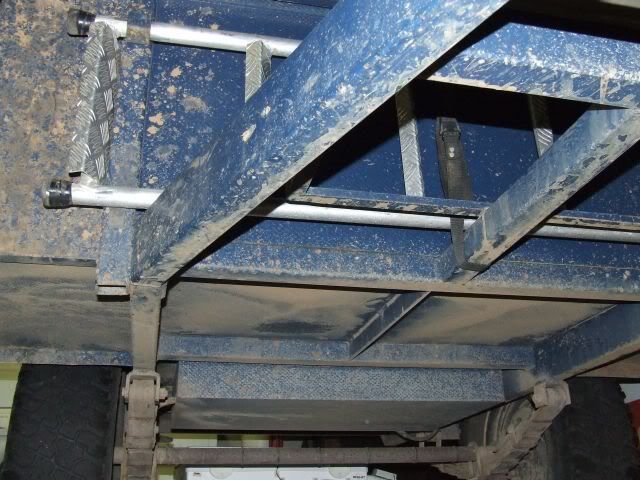
Gusset at bend.
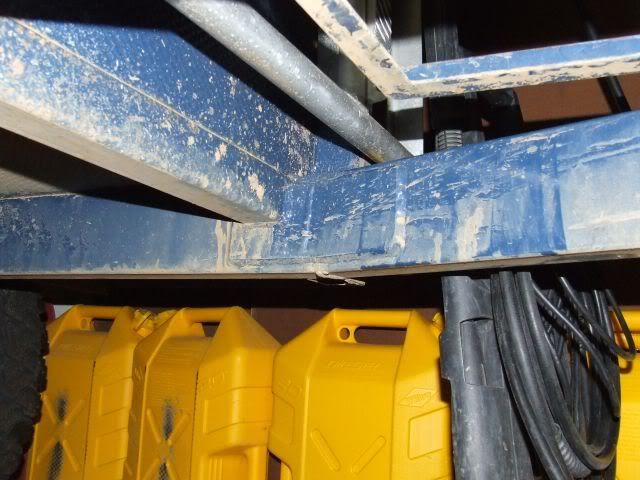
Back of chassis is lowest point so trailer never gets hung up. Makes a solid base to mount recovery hook too.
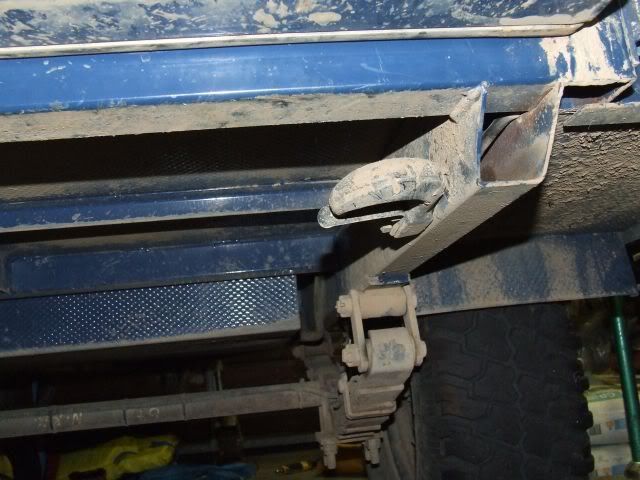

As for suspension and axles. Go for a braked setup. You wont regret it. Here a site that will be helpful. These guys are just up the road from me and have a good reputation. Good prices too.

http://www.etrailerparts.com.au/index1. ... tus.html&1
Running the 100x50 rails (with 50x50 cross bars) all the way to the back provides a strong base to work with. The rear works a a slider too instead of hitting a stop (cross bar support or similar.) as with most trailers on the market.
Since you are building this from scratch. There is bugger all difference in cost in making it bulletproof so to speak. Here's a few pics of my chassis.
Use a 50x50 across the middle of draw bar to reinforce as well as providing strong base for chest, esky (75L on mine), bikes, etc.
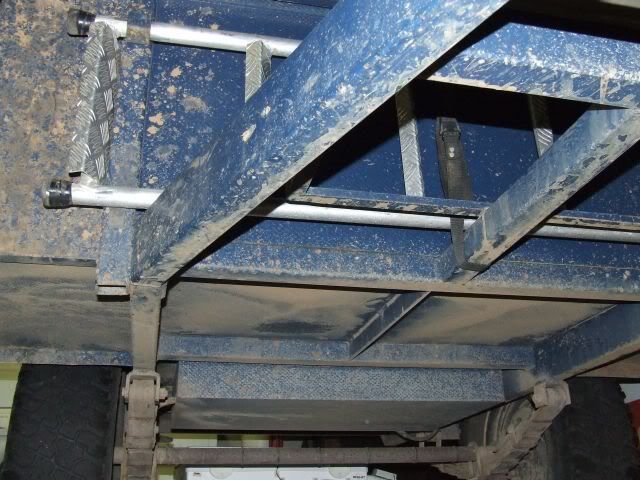
Gusset at bend.
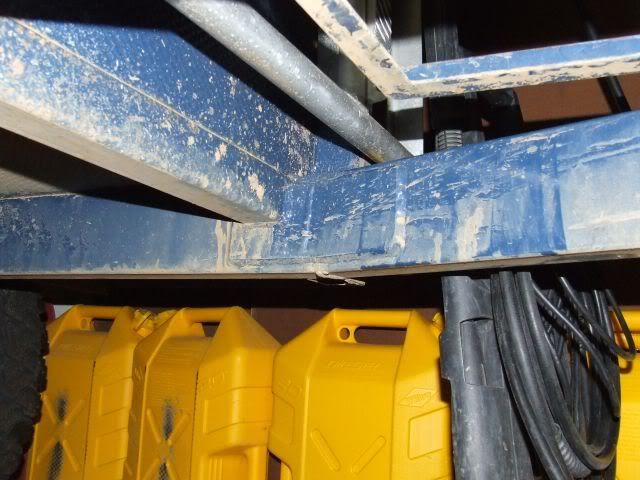
Back of chassis is lowest point so trailer never gets hung up. Makes a solid base to mount recovery hook too.
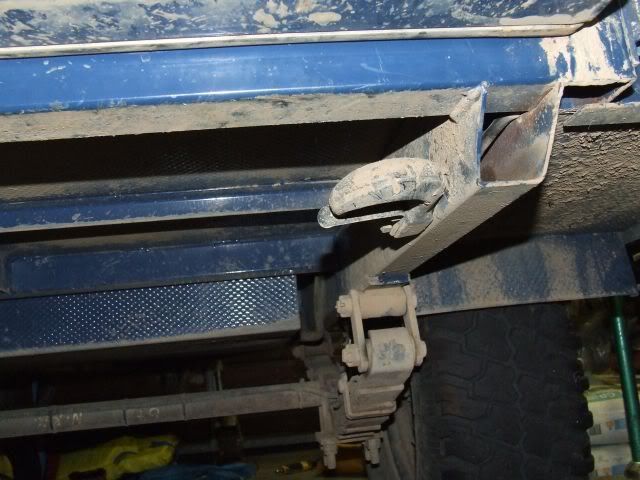
GU Patrol with go better bits added
wrong
skeg, you should always join the draw bar under the body not level or past the front so you can weld both parts securely to the under side and dont weld across the top of the draw bar to the body it will flex and it will break, it needs to flex. i build trailers, www.trailermade.com.au cheers steve
i dont naturaly look this bad work done it to me
Re: wrong
good point. i'm told that they often keep the draw bar a little light so it will flex and absorb a lot of the bumps. for a leaf spring road trailer thats very handy but 4x4 trailer with decent springs and shocks i would rather go with it being heavy duty.hollywood wrote:........... it needs to flex...........
shocks are well worth the cost. i got quad shocks on our tandem we get no vibration from it when it hits bumps on the road.
Thankyou for the pics, that is what i was thinking. I like how you finished the end of the trailer off, i may have pinch that idea (i may cap the ends off though).Skegbudley wrote:Thats @ 90 degrees to the front of box, not the length of the bar from the front of box to the end of draw bar. (just to make sure. hehe.)
As for suspension and axles. Go for a braked setup. You wont regret it. Here a site that will be helpful. These guys are just up the road from me and have a good reputation. Good prices too.
http://www.etrailerparts.com.au/index1. ... tus.html&1
Running the 100x50 rails (with 50x50 cross bars) all the way to the back provides a strong base to work with. The rear works a a slider too instead of hitting a stop (cross bar support or similar.) as with most trailers on the market.
Since you are building this from scratch. There is bugger all difference in cost in making it bulletproof so to speak. Here's a few pics of my chassis.
Use a 50x50 across the middle of draw bar to reinforce as well as providing strong base for chest, esky (75L on mine), bikes, etc.
Gusset at bend.
Back of chassis is lowest point so trailer never gets hung up. Makes a solid base to mount recovery hook too.
Its not cool, unless it's got boost :)
I wish I could take credit for the trailer build but it was made by NRR (no roads required) trailers in Brisbane. (Out of business now?)MARKx4 wrote: Thankyou for the pics, that is what i was thinking. I like how you finished the end of the trailer off, i may have pinch that idea (i may cap the ends off though).
Its different to just about every trailer on the market. Bloody strong unit.
The tent unit is on teflon sliders and slides out to the side. I have a full length rack up the top as well as boat carrier. Can setup the tent without taking anything off the top first.
I was planning on building one with this type of chassis but I was offered this trailer at a price that I could not refuse. (10k off retail

One other thing. Make sure to use an off road hitch. Normal trailer hitches suck offroad.
GU Patrol with go better bits added
Re: Trailer construction question
thats how mine is. drawbar starts back at the axles and goes out heaps infront.. brilliant for towing and reversing.Loanrangie wrote:1 change i would make is to make the drawbar come from about the centre of the axle out thru the middle of the A frame and then mount the coupling to that ?
Re: Trailer construction question
Can u post pics if u get the chance please.bogged wrote:thats how mine is. drawbar starts back at the axles and goes out heaps infront.. brilliant for towing and reversing.Loanrangie wrote:1 change i would make is to make the drawbar come from about the centre of the axle out thru the middle of the A frame and then mount the coupling to that ?
Its not cool, unless it's got boost :)
Re: Trailer construction question
kewl..MARKx4 wrote:Can u post pics if u get the chance please.bogged wrote:thats how mine is. drawbar starts back at the axles and goes out heaps infront.. brilliant for towing and reversing.Loanrangie wrote:1 change i would make is to make the drawbar come from about the centre of the axle out thru the middle of the A frame and then mount the coupling to that ?
Who is online
Users browsing this forum: No registered users and 5 guests