Notice: We request that you don't just set up a new account at this time if you are a previous user.
If you used to be one of our moderators, please feel free to reach out to Chris via the facebook Outerlimits4x4 group and he will get you set back up with access should he need you.
If you used to be one of our moderators, please feel free to reach out to Chris via the facebook Outerlimits4x4 group and he will get you set back up with access should he need you.
Recovery:If you cannot access your old email address and don't remember your password, please click here to log a change of email address so you can do a password reset.
steering rod strengthening
Moderators: toaddog, TWISTY, V8Patrol, Moderators
steering rod strengthening
i have done a bit of a search and cant find the info i need
i have seen some rigs with a bit of angle welded along the length
of there tierod - draglink to strenghten them up
whats has some of the members done and what advice to you have in regards to doing something like this
troop
i have seen some rigs with a bit of angle welded along the length
of there tierod - draglink to strenghten them up
whats has some of the members done and what advice to you have in regards to doing something like this
troop
.
I couldnt keep them straight (even snake's rock rods that are aparently tested on a 60tonne press) in the end i used me standard steering arm (front one) ground to fit inside the standard drag link (rear one) then welded angle onto the whole thing. I have competed with this setup for 3 years now without even a slight bend. (touch wood)
It was a bit of stuffing around but it has paid off
It was a bit of stuffing around but it has paid off
WHEELERS FABRICATIONS, DUEL CAB + EXO CAGE. 4"SUSP 2"BODY 35" CLAWS, TWIN LOCKED, BUILT 4 FUN
I had the angle welded to my steering arm, But I did have one cop who didn't like it.
I asked him what was more safer, my setup or a damaged and weakened steering arm breaking while on the highway coming home from a drive.
He agreed with me, and since there was nothing else wrong and it was obvious I took the cruiser off road he let it go.
I eneded using the machines at work to make a solid bar fitted to take standard tie rod ends. Painted black it looked factory.
I asked him what was more safer, my setup or a damaged and weakened steering arm breaking while on the highway coming home from a drive.
He agreed with me, and since there was nothing else wrong and it was obvious I took the cruiser off road he let it go.
I eneded using the machines at work to make a solid bar fitted to take standard tie rod ends. Painted black it looked factory.
I had to cut the pipe and weld it back together as the drag link has a ball joint at one end and a tapered hole at the other.troopymad wrote:want33s thats the way ill go
i want to try and get my pipe (4mm wall) to slide over the top of my tierod and draglink
whats was the reason you cut the pipe lenght ways before welding it on?
was it to hard to find the right sized pipe?
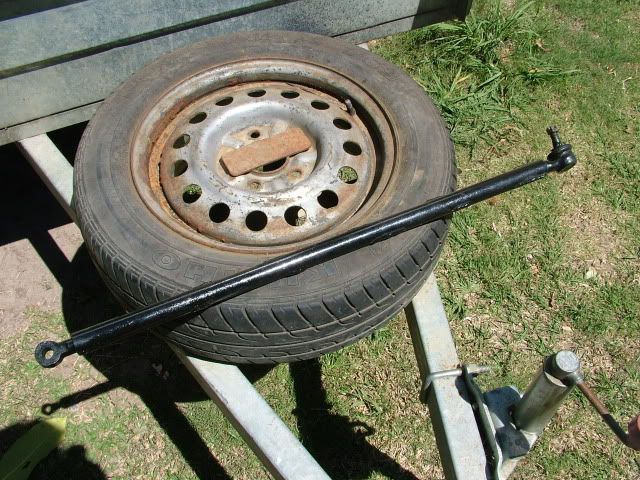
Pipe was easy to get at Onesteel. I think it was 20Nb.
Forgive my slight misinformation if it is so but ignoring the different choices of material I was always led to believe that a thick wall hollow section would actually give more strength that a solid bar. Theory being that the solid bar is a singular structure and still generates a certain amount of flex but the hollow bar presents 2 seperate walls which resist the flex more.80's_delirious wrote:find a local engineering shop who can make up one from solid 25mm 4130, it should cost you less than $100, its just a straight bar drilled and tapped both ends to suit your rod ends.
I would love the correct engineering interpretation on this if someone has it.
im no engineer but i was alao lead to belive the same thingfester2au wrote:Forgive my slight misinformation if it is so but ignoring the different choices of material I was always led to believe that a thick wall hollow section would actually give more strength that a solid bar. Theory being that the solid bar is a singular structure and still generates a certain amount of flex but the hollow bar presents 2 seperate walls which resist the flex more.80's_delirious wrote:find a local engineering shop who can make up one from solid 25mm 4130, it should cost you less than $100, its just a straight bar drilled and tapped both ends to suit your rod ends.
I would love the correct engineering interpretation on this if someone has it.
lol not this again! hahaha
ok - take a pipe with walls as thick as al-foil... it bends right??? now, thicken the walls to 3mm... its stronger... thicken to 6mm, stronger again right? does this mean that once the hole in the pipe reaches .001mm its at its stongest and as soon as you make it a solid bar it becomes weaker?
ok - take a pipe with walls as thick as al-foil... it bends right??? now, thicken the walls to 3mm... its stronger... thicken to 6mm, stronger again right? does this mean that once the hole in the pipe reaches .001mm its at its stongest and as soon as you make it a solid bar it becomes weaker?
The worst thing about censorship is ███████.
Who is online
Users browsing this forum: No registered users and 4 guests