Notice: We request that you don't just set up a new account at this time if you are a previous user.
If you used to be one of our moderators, please feel free to reach out to Chris via the facebook Outerlimits4x4 group and he will get you set back up with access should he need you.
If you used to be one of our moderators, please feel free to reach out to Chris via the facebook Outerlimits4x4 group and he will get you set back up with access should he need you.
Recovery:If you cannot access your old email address and don't remember your password, please click here to log a change of email address so you can do a password reset.
what to use? - notching tube
Moderators: toaddog, TWISTY, V8Patrol, Moderators
what to use? - notching tube
is there a proper tool, like some sort of large drill bit, to notch round tube?
i have been using a grinder, but surley there is something better. sick of gaps when joining tube together.
asked at a fuel tool shops, but they couldnt help.
i have been using a grinder, but surley there is something better. sick of gaps when joining tube together.
asked at a fuel tool shops, but they couldnt help.
HoldFast RocKrawlin
Tube Notching
Speedwerx make a holesaw type tube notcher
Fairly expensive if you only want to a few joins
Tube mitre is a progam you can get What you do is put in tube / pipe sizes (diametres) both base and mitred and the angle you want the tubes to meet at and print out a paper template. You then use this to mark and cut your tube, couple of angled cuts and a dress up with the grinder and your done
Would not let me attach it pm your email and I will send it
Fairly expensive if you only want to a few joins
Tube mitre is a progam you can get What you do is put in tube / pipe sizes (diametres) both base and mitred and the angle you want the tubes to meet at and print out a paper template. You then use this to mark and cut your tube, couple of angled cuts and a dress up with the grinder and your done
Would not let me attach it pm your email and I will send it
speedwerx is shit. i do not care who says what about them, i have tried time and time again. biggest waste of money. every time i have used it i have had to comprimise the fish mouth to use except for the centre on my x on the roll cage. steer clear you have been warned!
i use a plasma now, but a angle grinder and a die grinder works a treat.
cheers bru
i use a plasma now, but a angle grinder and a die grinder works a treat.
cheers bru
ADHD Racing would like to thank
Mrs Bru @ Sunshine Coast Developmental Physiotherapy - www.scdphysio.com.au , Ryano @ Fourbys www.generaltire.com.au Blitzkrieg Motorsport
Mrs Bru @ Sunshine Coast Developmental Physiotherapy - www.scdphysio.com.au , Ryano @ Fourbys www.generaltire.com.au Blitzkrieg Motorsport
I just bought a 50mm holesaw and use that .Works a treat for 90 deg joins.Have also used the tube mitre program and made up a few stensils.
Also used angle grinder and have tried the oxy.
When i can afford it i will get a plasma for sure.
Also used angle grinder and have tried the oxy.
When i can afford it i will get a plasma for sure.
"Why do the British drink their beer at room temperature? Because Lucas builds their refrigerators."
holesaw is the go. ya eat through them pretty quickly though. lucky to get 10 notches outta the cheap ones. but they're like $6 each, so doesn't matter that much
we dont use a notcher, just tack the pipe to a vice clamped to the drill and ya good to go
with the steeper angles, the tube bottoms out inside the holesaw, so you need a grinder handy to take some cuts outta the notch so ya can go all the way through
we dont use a notcher, just tack the pipe to a vice clamped to the drill and ya good to go
with the steeper angles, the tube bottoms out inside the holesaw, so you need a grinder handy to take some cuts outta the notch so ya can go all the way through
You must be doing something wrong here. We have had our speedwerx for a few years now and it would have done at least a thousand notches (15 tube buggies plus whatever else). If you set it up right you dont have to grind all. I would guess that on over 99% of our notches we never use a grinder. On the moon buggies there is only one notch that we have to grind cause the angle is too sharp. We even use the notcher free hand and just clamp it straight to a tube on the frame (not mounted to the bench)bru21 wrote:speedwerx is shit. i do not care who says what about them, i have tried time and time again. biggest waste of money. every time i have used it i have had to comprimise the fish mouth to use except for the centre on my x on the roll cage. steer clear you have been warned!
i use a plasma now, but a angle grinder and a die grinder works a treat.
cheers bru
To notch a tube including setting the angle would take less than 20 seconds and you get an absolutely perfect notch. Couldnt imagine doing it any other way.
Sam
Sam, when you want to get really serious in tube notching here's what we use every day, a big @rsed bridgeport mill with RMR (rapid metal removal) cutters. We use a protractor to set the angle and tighten the vice and cut, you can't beat these in a production enviroment. Another good thing about the setup is if you only need to take off another fraction of a millimeter just put it back in the vice and cut again, you can't do that with the holesaw notchers.Strange Rover wrote: You must be doing something wrong here. We have had our speedwerx for a few years now and it would have done at least a thousand notches (15 tube buggies plus whatever else). If you set it up right you dont have to grind all. I would guess that on over 99% of our notches we never use a grinder. On the moon buggies there is only one notch that we have to grind cause the angle is too sharp. We even use the notcher free hand and just clamp it straight to a tube on the frame (not mounted to the bench)
To notch a tube including setting the angle would take less than 20 seconds and you get an absolutely perfect notch. Couldnt imagine doing it any other way.
Sam
Cutters are a bit exxy though

Regards Andrew.
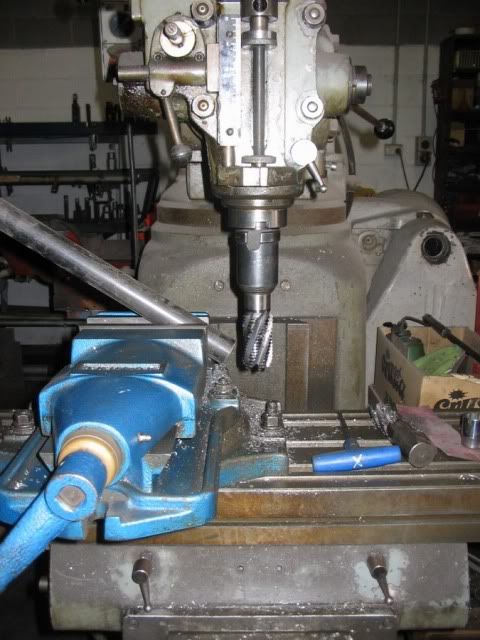
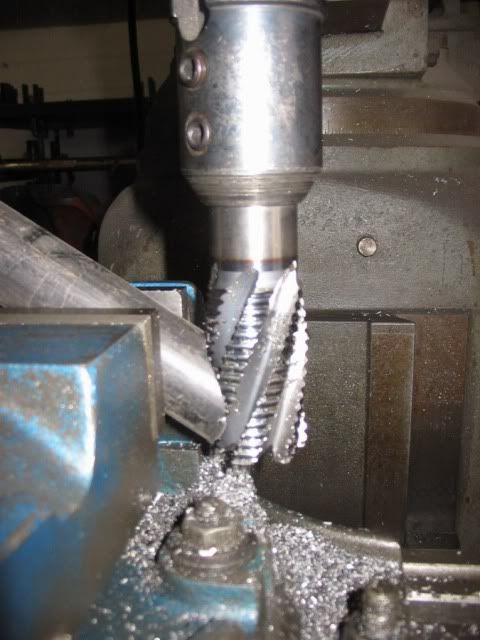
We are Tig welders, gravity doesn't worry us.
[img]http://www.studmonkeyracing.com/forums/smilies/weld.gif[/img]
[img]http://www.studmonkeyracing.com/forums/smilies/weld.gif[/img]
Thats nice - but you would be supprised how well the speedwerx notcher works. The way we build our buggies we have to notch tubes that are already in the fame (just easier to build them this way) so the mill isnt going to get to those. Also the speedwerx can renotch within millimetres, it doesent use a centre drill. Is has a linear bearing much like your mill - just no powerfeed.awill4x4 wrote: Sam, when you want to get really serious in tube notching here's what we use every day, a big @rsed bridgeport mill with RMR (rapid metal removal) cutters. We use a protractor to set the angle and tighten the vice and cut, you can't beat these in a production enviroment. Another good thing about the setup is if you only need to take off another fraction of a millimeter just put it back in the vice and cut again, you can't do that with the holesaw notchers.
Cutters are a bit exxy though![]()
Regards Andrew.
Sam
Probably the only downside to the speedwerx is that it doesent like notching close to a bend cause the pipe vice need a straight piece to run through to clamp onto.
And also its difficult to notch something off the centre line of the tube again because the vice always centres the tube. For example if you wanted to notch some 25NB to join to some 32NB and have it all flat on the outside - it wont do this. It will make the centrelines line up not - the outsides.
Sam
And also its difficult to notch something off the centre line of the tube again because the vice always centres the tube. For example if you wanted to notch some 25NB to join to some 32NB and have it all flat on the outside - it wont do this. It will make the centrelines line up not - the outsides.
Sam
I am getting the TN 100 tube notcher from JD squared through Peter Antunac as well as the model 4 bender. This seems to be the best set-up for tube work as this is widely used throughout the world.
I have got the bend tech programme that gives you the necessary information in a 3 axis format with cooridinates, angles & cutting lengths for notching. Absolutely brilliant.
brooksy
I have got the bend tech programme that gives you the necessary information in a 3 axis format with cooridinates, angles & cutting lengths for notching. Absolutely brilliant.
brooksy
C44F-Custom 4x4 Fabrications
0400 443 802
brooksy72@live.com.au
0400 443 802
brooksy72@live.com.au
brooksy wrote:I am getting the TN 100 tube notcher from JD squared through Peter Antunac as well as the model 4 bender. This seems to be the best set-up for tube work as this is widely used throughout the world.
I have got the bend tech programme that gives you the necessary information in a 3 axis format with cooridinates, angles & cutting lengths for notching. Absolutely brilliant.
brooksy

how easy is Bendtech to use?
Outers & Arms up stickers coming soon you hungry bitches!
http://www.myultimate4wd.com
http://www.myultimate4wd.com
GRIMACE wrote:How I miss the days of care free wheelin with the crews!
You could try the pipemaster...
http://vansantent.com/pipemaster.htm
not that expensive and looks like it would work pretty good, youll still need the grinder but at least it will be accurate. Ill be getting some of these when i start bending tube.
http://vansantent.com/pipemaster.htm
not that expensive and looks like it would work pretty good, youll still need the grinder but at least it will be accurate. Ill be getting some of these when i start bending tube.
Yurich Design Services
www.yds.net.au
www.yds.net.au
roc70y wrote:brooksy wrote:I am getting the TN 100 tube notcher from JD squared through Peter Antunac as well as the model 4 bender. This seems to be the best set-up for tube work as this is widely used throughout the world.
I have got the bend tech programme that gives you the necessary information in a 3 axis format with cooridinates, angles & cutting lengths for notching. Absolutely brilliant.
brooksy$$$$$$$$$$$$$
how easy is Bendtech to use?
You can get the programme now via the internet instead of waiting for the disc to arrive from the US. They're is 4 different programs & the cost is in $US. EZ- $59, EZ-3D - $149, SE- $399, PRO- $275.
The company that designed the program is www.2020ssi.com or go to this site www.bend-tech.com as you can order through their also as it is run by the company.
I was thinking of ordering the pipemaster through trick tools also. They look a great little tool.
brooksy
C44F-Custom 4x4 Fabrications
0400 443 802
brooksy72@live.com.au
0400 443 802
brooksy72@live.com.au
An easy way around making notches is buying a length of plastic pipe that is the same dimensions as the tube you are going to notch. Take time to cut the pipe to the correct angle and then use it as a template to slide over the tube. You start building up common angles that you can reuse.
Cheap and easy.
By the way how much is the JD2 bender, dies and notcher costing you
Cheap and easy.
By the way how much is the JD2 bender, dies and notcher costing you
Isnt it a lot stronger if you actually cut into the " other pipe" and feed the ( notched pipe) into it rather than notching it. That way your not totally relying on welds to hold a cage together. Its my belief that sprintcar cages have to built using this method. I hope this makes sense to you as i cant really think of a better way to describe itawill4x4 wrote:Strange Rover wrote:
Cheers
Considering we build and repair sprintcar chassis' as a full time job, I think we're doing it the right waypongo wrote: Isnt it a lot stronger if you actually cut into the " other pipe" and feed the ( notched pipe) into it rather than notching it. That way your not totally relying on welds to hold a cage together. Its my belief that sprintcar cages have to built using this method. I hope this makes sense to you as i cant really think of a better way to describe it
Cheers

Regards Andrew.
We are Tig welders, gravity doesn't worry us.
[img]http://www.studmonkeyracing.com/forums/smilies/weld.gif[/img]
[img]http://www.studmonkeyracing.com/forums/smilies/weld.gif[/img]
I am getting my model 4 JD2 bender & dies threw Peter Antunac (OPW) & considering the local made bender from a Melbourne company wants $11,500 for just the bender- NO DIESjeep97tj wrote:Thats what i want to know, final $$ on the bender and die?


You can also get the bender from ABT4x4.
brooksy
C44F-Custom 4x4 Fabrications
0400 443 802
brooksy72@live.com.au
0400 443 802
brooksy72@live.com.au
Maybe the actual joint would be strong if you tried to pull both pieces apart latterally but that's not the idea of a cage or frame. The pipe you have "cut into" would no doubt have it's strength comprimised as the tubular shape is where the strength lies. A side impact would see the tube fold open or bend a lot easier if the tube was "cut into" than if you done it the "correct" way as you'd only have half of the tube left and your strength would be in your weld only, not the tube and the weld.pongo wrote:awill4x4 wrote:Isnt it a lot stronger if you actually cut into the " other pipe" and feed the ( notched pipe) into it rather than notching it. That way your not totally relying on welds to hold a cage together. Its my belief that sprintcar cages have to built using this method. I hope this makes sense to you as i cant really think of a better way to describe itStrange Rover wrote:
Cheers
are we talking about the same cutter!! I can only assume that you allow excess tube in your bends and clam to the discarded tube, or use a defferent radius bend to mine or smaller diameter tube - i use 50mm mainly. every join on my cage is halfway through a bend and cannot be clamped by the notcher. i guess buggies have mainy straight notches without bends. also unless you cut away the centre line of the tube the saw will not get all the way through even on straight notches, and often jams the cutter when passing through the centre.Strange Rover wrote:You must be doing something wrong here. We have had our speedwerx for a few years now and it would have done at least a thousand notches (15 tube buggies plus whatever else). If you set it up right you dont have to grind all. I would guess that on over 99% of our notches we never use a grinder. On the moon buggies there is only one notch that we have to grind cause the angle is too sharp. We even use the notcher free hand and just clamp it straight to a tube on the frame (not mounted to the bench)bru21 wrote:speedwerx is shit. i do not care who says what about them, i have tried time and time again. biggest waste of money. every time i have used it i have had to comprimise the fish mouth to use except for the centre on my x on the roll cage. steer clear you have been warned!
i use a plasma now, but a angle grinder and a die grinder works a treat.
cheers bru
To notch a tube including setting the angle would take less than 20 seconds and you get an absolutely perfect notch. Couldnt imagine doing it any other way.
Sam
please post pics i must be missing something major, have a different notcher, or something.
i am on my 3rd cutter too. i use a reduction drill so it is not too fast and apply water directly to the cut during cutting to save the blades - can't see that i would have done any more than 50 notches with it and at $25 a blade it is a dear method. i have often thought that the milling cutter would be better even in a drill.
with the plasma i just hold the tube to be notched close mark the notch centreline on both sides and a basic shape, 30 sec later i am cleaning out the centre with the die grinder and its 100% - also the edges are fulll thickness and are better to weld as well as being stronger than the paper thin notched ones! the advantage is also where mirrored tubes and hence notches are i just mark by placing the notched tube back to back both ways, cut and its a snug fit, the speedwerx needs the angle changed!
cheers bru
ADHD Racing would like to thank
Mrs Bru @ Sunshine Coast Developmental Physiotherapy - www.scdphysio.com.au , Ryano @ Fourbys www.generaltire.com.au Blitzkrieg Motorsport
Mrs Bru @ Sunshine Coast Developmental Physiotherapy - www.scdphysio.com.au , Ryano @ Fourbys www.generaltire.com.au Blitzkrieg Motorsport
I'm not offended at all Pongo, hence the "winking smileypongo wrote:I hope i havent offended you. I saw you avatar and figured you knew sprintcars. I guess you cleared that up for me.
Do you think the way i suggested would make it any stronger or just a waste of time/ hassle?
thanx

Cutting a hole in a tube to insert another tube would actually weaken the joint drastically and on tubes where both are the same diameter it's simply not feasible anyway.
Regards Andrew.
We are Tig welders, gravity doesn't worry us.
[img]http://www.studmonkeyracing.com/forums/smilies/weld.gif[/img]
[img]http://www.studmonkeyracing.com/forums/smilies/weld.gif[/img]
Mine is an eariler version of this one (only thing different is the clamp)bru21 wrote: are we talking about the same cutter!! I can only assume that you allow excess tube in your bends and clam to the discarded tube, or use a defferent radius bend to mine or smaller diameter tube - i use 50mm mainly. every join on my cage is halfway through a bend and cannot be clamped by the notcher. i guess buggies have mainy straight notches without bends. also unless you cut away the centre line of the tube the saw will not get all the way through even on straight notches, and often jams the cutter when passing through the centre.
please post pics i must be missing something major, have a different notcher, or something.
i am on my 3rd cutter too. i use a reduction drill so it is not too fast and apply water directly to the cut during cutting to save the blades - can't see that i would have done any more than 50 notches with it and at $25 a blade it is a dear method. i have often thought that the milling cutter would be better even in a drill.
cheers bru
http://www.speedwerx.com.au/tubenotcher.html
And yes we make sure we have a straight piece of pipe going through the vice - we basically design the tube work this way.
Some hole saws are better than others. We always use a cutting compound (trefolux (sp?)).
Also have a belt sander right beside the notcher and we sand the end of the pipe after we notch to make the edges full thickness (its only the tips of the notch where the pipe ends up this) This process takes less time to do that wiping the cutting fluid from the end of the pipe.
If you had to notch most of your tubes midway through a bent I could see that this notcher isnt going to work well.
Sam
On mild steel, using cutting compound, with a slow speed drill (around 600rpm) I would guess over 100 notches. I think we had one hole saw last building a couple of buggies.DAWSO 4x4 wrote:how many notchs can be done on a hole saw before resharping and do you use it on 4140
You can stuff the hole saw in one go if you dont know what you are doing though - you can chip teeth or bend the saw if the piece you are notching jams the saw.
Sam
Has anyone tried this one before???
It is an actual notcher, not a hole cuuter.
http://www.steeraust.com.au/steer/notcher.htm

It is an actual notcher, not a hole cuuter.
http://www.steeraust.com.au/steer/notcher.htm

2005 GU3 Patrol ST Ute
only 2 probs i see with that, only does up to 2.9mm wall, and can it do angle notches? or only straight?Mytqik wrote:Has anyone tried this one before???
It is an actual notcher, not a hole cuuter.
http://www.steeraust.com.au/steer/notcher.htm
Who is online
Users browsing this forum: No registered users and 2 guests