EDIT: A pic of the bugger. I found a number for Acme Machine Works in Sydney, but all I got was this pissed off old Italian guy whinging that they got the number listed wrong

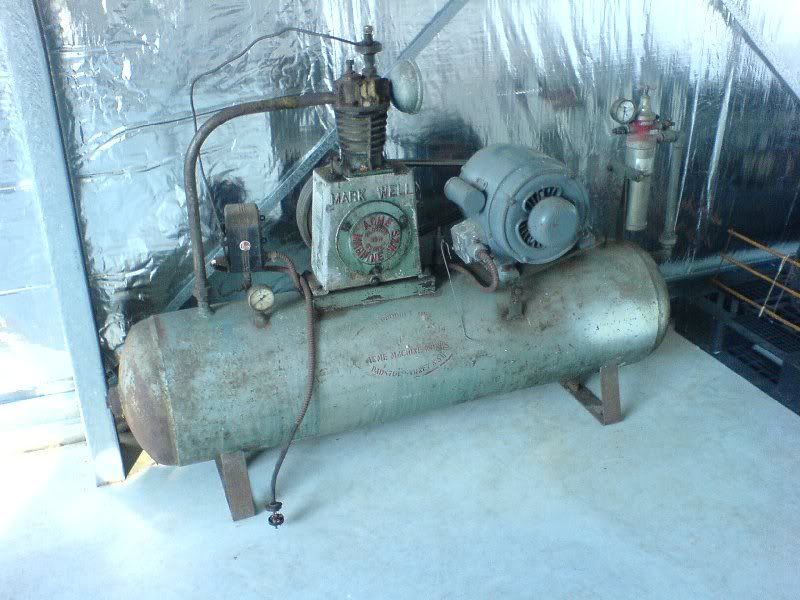
Moderators: toaddog, TWISTY, V8Patrol, Moderators
Damo wrote:I found a number for Acme Machine Works in Sydney, but all I got was this pissed off old Italian guy whinging that they got the number listed wrong![]()
If his mood was anything to go by i'd say quite a fewHekta wrote:Damo wrote:I found a number for Acme Machine Works in Sydney, but all I got was this pissed off old Italian guy whinging that they got the number listed wrong![]()
![]()
I wonder how many calls he gets to fix people's junk ?
Yepudlman wrote:Did U get that one off Ebay??
I think I will end up taking the head off if only just to check things.udlman wrote: It should be a simple matter of checking the poppet valves in the head.
I've read that multi staged compressors only made a real difference to the pressure that can be made. But when I think about it 2 cylinders = 2 times the air displaced in each revolution. In any case yes it is slow to come up to pressure, but I think that is mostly due to the fact that the reciever is so large.udlman wrote: It looks as tho it would be slow to pump up as it seems to be a single stage unit..
Uh huh. Sony Ericsson W810idroopypete wrote:Have you got a new cam Damo?![]()
Peter.
Pilot Air Compressors can supply parts. They bought all the old stock when Acme (the manufacturer) went under about 10 years ago. You can find their contact details on their web site www.pilotair.com.au. If you have troubles getting info out of them contact Bob at the Brisbane store, he's been really helpful.460cixy wrote:i have the exact same compressor its prety slow to pump up but the tank is huge and has no trouble keeping up when i spray. if you find some one that can get parts for them let me know i wouldent mind re ringing mine theres a little oil getting in to the tank its getting a bit tired. i love the noise it makes when its running but the folks next door dont.
Is that a standard thing? Sounds wierd to me. I have a spare one if you need it460cixy wrote:mine has no decomp valve so i have to wind it round to tdc before i flick the switch
well the decomp is there but its rootedDamo wrote:Is that a standard thing? Sounds wierd to me. I have a spare one if you need it460cixy wrote:mine has no decomp valve so i have to wind it round to tdc before i flick the switch
Got a bit more progress yesterday. Got the head pulled apart. The plug on the exhaust side did NOT want to come off. I dont have my shed setup at the moment so I didn't have a chance of getting it off, so I dropped it off at my local tyre place. Tyre place because they have a 3/4" drive rattle gunbut it still needed a heap of heat to free it.
I still need to clean up the valves and refit them and see if that makes a difference.
Users browsing this forum: No registered users and 4 guests