Notice: We request that you don't just set up a new account at this time if you are a previous user.
If you used to be one of our moderators, please feel free to reach out to Chris via the facebook Outerlimits4x4 group and he will get you set back up with access should he need you.
If you used to be one of our moderators, please feel free to reach out to Chris via the facebook Outerlimits4x4 group and he will get you set back up with access should he need you.
Recovery:If you cannot access your old email address and don't remember your password, please click here to log a change of email address so you can do a password reset.
Widened hi-mount
Moderators: toaddog, TWISTY, V8Patrol, Moderators
Freakazoid, you may be right in that the side plate will give up first. However I don't think you will be putting extra strain on the gears as (at least in theory) the torque remains the same as it is set by the motor. The motor drives the gears, not the load. Or have I got something wrong?
Actually my calculation of load is slightly out. I did not take account of the rope thickness! With 8mm wire (5/16") the theoretical max pull is 13,100 lb so you have a bit more to play with.
The figure should be about the same with 12mm Vectra - I haven't calculated it as I don't know what diameter that rope is under load, but the main point is that as the drum diameter is reduced the load gets greater and the effect is greater the smaller the drum.
Are you incorporating a sealed roller bearing in the end plate?
Like you I would be interested in hearing from anyone who has done this modification - wider, smaller dia drum and roller bearing. Could save us a lot of messing around.
Actually my calculation of load is slightly out. I did not take account of the rope thickness! With 8mm wire (5/16") the theoretical max pull is 13,100 lb so you have a bit more to play with.
The figure should be about the same with 12mm Vectra - I haven't calculated it as I don't know what diameter that rope is under load, but the main point is that as the drum diameter is reduced the load gets greater and the effect is greater the smaller the drum.
Are you incorporating a sealed roller bearing in the end plate?
Like you I would be interested in hearing from anyone who has done this modification - wider, smaller dia drum and roller bearing. Could save us a lot of messing around.
1982 Patrol K160 SWB (MQ) 4L P40 Petrol with Megasquirt fuel injection and EDIS ignition. Warn 8274 winch with Gigglepin head
Krimnl - I liked the pics on your site. Obviously your wide drum/bearing set up has stood up to some hard work. But can you remember what bearing you used or is it a trade secret? And is it a sealed bearing?
Freakazoid, I called at my friendly local bearing centre yesterday. Complicated things bearings apparently - not just a few balls in a cage!
I couldn't find any bearing which would fit in the end housing without a packing collar. And was told that roller bearings do not come in a sealed version. Cylindrical roller bearings can take a higher radial load than ball bearings. One I looked at (N209 I think) was rated at 46,000N (10,500lbs) but was pricy. A sealed ball bearing (6209 dimensions 45x85x19) was a quarter the price ($NZ40) and was rated at 7000lb rolling, 4500lb static.
I am assuming that the bearing would be mounted in the existing endplate using a packing ring and that you would have to fabricate an "adapter plug" which would project from the drum and be turned down to match the ID of the bearing. Or is there a simpler way?
Gosh! It would be a lot easier if someone could post details of how they had done it!:oops:
David
Freakazoid, I called at my friendly local bearing centre yesterday. Complicated things bearings apparently - not just a few balls in a cage!
I couldn't find any bearing which would fit in the end housing without a packing collar. And was told that roller bearings do not come in a sealed version. Cylindrical roller bearings can take a higher radial load than ball bearings. One I looked at (N209 I think) was rated at 46,000N (10,500lbs) but was pricy. A sealed ball bearing (6209 dimensions 45x85x19) was a quarter the price ($NZ40) and was rated at 7000lb rolling, 4500lb static.
I am assuming that the bearing would be mounted in the existing endplate using a packing ring and that you would have to fabricate an "adapter plug" which would project from the drum and be turned down to match the ID of the bearing. Or is there a simpler way?
Gosh! It would be a lot easier if someone could post details of how they had done it!:oops:
David
1982 Patrol K160 SWB (MQ) 4L P40 Petrol with Megasquirt fuel injection and EDIS ignition. Warn 8274 winch with Gigglepin head
Surely there is someone out there who has put a roller bearing in the free end of a hi-mount and is prepared to divulge roughly how he did it. Specifically the size and type of bearing.
I don't really want to reinvent "the square wheel"!
David
I don't really want to reinvent "the square wheel"!
David
1982 Patrol K160 SWB (MQ) 4L P40 Petrol with Megasquirt fuel injection and EDIS ignition. Warn 8274 winch with Gigglepin head
Mine was done by Mal Leslie a few years ago. there was some machining and welding required on the endplateDavid_S wrote:Krimnl - I liked the pics on your site. Obviously your wide drum/bearing set up has stood up to some hard work. But can you remember what bearing you used or is it a trade secret? And is it a sealed bearing?
Freakazoid, I called at my friendly local bearing centre yesterday. Complicated things bearings apparently - not just a few balls in a cage!
I couldn't find any bearing which would fit in the end housing without a packing collar. And was told that roller bearings do not come in a sealed version. Cylindrical roller bearings can take a higher radial load than ball bearings. One I looked at (N209 I think) was rated at 46,000N (10,500lbs) but was pricy. A sealed ball bearing (6209 dimensions 45x85x19) was a quarter the price ($NZ40) and was rated at 7000lb rolling, 4500lb static.
I am assuming that the bearing would be mounted in the existing endplate using a packing ring and that you would have to fabricate an "adapter plug" which would project from the drum and be turned down to match the ID of the bearing. Or is there a simpler way?
Gosh! It would be a lot easier if someone could post details of how they had done it!:oops:
David
Just a comment on using a 50mm drum. Dyneema has a minmun radius been to keep it's rated strength. From memory it is, radius eaquals 5 times the rope diameter. So with 10 mm even the standard drum is a wee bit small! Obviously some people have been using smaller drums for a while but it is something to think about.
93 Nissan Pathfinder / Terrano Turboed VH45, GQ Trans and T-case, coil overs, hydraulic winch and fair bit of other stuff. (Currently a pile of parts in the workshop)
This is an interesting point which applies to wire as much as to synthetic rope. For wire rope one manufacturer gives the ratio of drum dia to wire dia as anything from 14 to 42 depending on the rope construction. Seenzdarin wrote:Just a comment on using a 50mm drum. Dyneema has a minmun radius been to keep it's rated strength. From memory it is, radius eaquals 5 times the rope diameter. So with 10 mm even the standard drum is a wee bit small! Obviously some people have been using smaller drums for a while but it is something to think about.
https://www.hanessupply.com/size.html
The standard Warn Hi-mount drum is 3.5" and the standard wire rope 5/16" which gives a ratio of only 11. A 2.5" drum would reduce this to 8. It is probable that you can get away with these smaller diameters because of the relatively infrequent use of 4wd winches. As the above site states the problem is one of fatigue. "The smaller the diameter of the sheave, the sooner these fatigue breaks will occur and the shorter rope life becomes." I am not sure that I would want a wire rope drum to be under 3".
The same effects probably occurs with synthetic rope though intuitively you would think that with its greater flexiblity it should cope with tighter bends than wire. Blocks and capstans on yachts are not that large diameter. 5 or 6 times the rope dia as nzdarin suggest would seem about right.
If there are any rope experts out there it would be interesting to have your comments.
David
1982 Patrol K160 SWB (MQ) 4L P40 Petrol with Megasquirt fuel injection and EDIS ignition. Warn 8274 winch with Gigglepin head
I've had my Estwing for over 15 years now Until the other day the bastard snapt the steel shaft rubber grip is still holding it together (hey don't they come with a life time warranty ) and yes I'm a Chippiechunderlicious wrote:if you use a hammer every day itll last 2 years before you need a new one..... even estwing are like that

CHEVRANGIECRUISER
my brothers are both carpenters and they both have thier eastwing hammers they baught during thier apprenticeships. 13 or so years ago.JUSTHI wrote:I've had my Estwing for over 15 years now Until the other day the bastard snapt the steel shaft rubber grip is still holding it together (hey don't they come with a life time warranty ) and yes I'm a Chippiechunderlicious wrote:if you use a hammer every day itll last 2 years before you need a new one..... even estwing are like that
One of them broke a claw on his recently, and it was replaced by tradetools.
i broke the handle off of mine about 6 months ago and glenfords replaced it under warranty and ive been a chippy for 12 yearsPosted: Sat Jan 27, 2007 12:46 pm
--------------------------------------------------------------------------------
JUSTHI wrote:
chunderlicious wrote:
if you use a hammer every day itll last 2 years before you need a new one..... even estwing are like that
I've had my Estwing for over 15 years now Until the other day the bastard snapt the steel shaft rubber grip is still holding it together (hey don't they come with a life time warranty ) and yes I'm a Chippie
my brothers are both carpenters and they both have thier eastwing hammers they baught during thier apprenticeships. 13 or so years ago.
One of them broke a claw on his recently, and it was replaced by tradetools.
GQ TD42, 4" lift, 2" bodylift, 4.6 s, detroit lockers, 35,s t3/t4 plus a turbo,
Thats interesting ,I was thinking about taking it to the yard I get my materials from now , the place I bought it from closed down a long time ago ,and who's going to have a reciept from that long ago anyway.Cheers guy's
92mav wrote:i broke the handle off of mine about 6 months ago and glenfords replaced it under warranty and ive been a chippy for 12 yearsPosted: Sat Jan 27, 2007 12:46 pm
--------------------------------------------------------------------------------
JUSTHI wrote:
chunderlicious wrote:
if you use a hammer every day itll last 2 years before you need a new one..... even estwing are like that
I've had my Estwing for over 15 years now Until the other day the bastard snapt the steel shaft rubber grip is still holding it together (hey don't they come with a life time warranty ) and yes I'm a Chippie
my brothers are both carpenters and they both have thier eastwing hammers they baught during thier apprenticeships. 13 or so years ago.
One of them broke a claw on his recently, and it was replaced by tradetools.
CHEVRANGIECRUISER
I started reading this thread because it said "widened high mount".... Not can all the outers chippies please tell me about your friggin hammers
I'd love to hear from someone that has done the roller bearing in the end plate aswell...

I'd love to hear from someone that has done the roller bearing in the end plate aswell...
[quote="Uhhohh"]As far as an indecent proposal goes, I'd accept nothing less than $100,000 to tolerate buggery. Any less and it's just not worth the psychological trauma. [/quote]
Hear! Hear!Ruffy wrote:I started reading this thread because it said "widened high mount".... Not can all the outers chippies please tell me about your friggin hammers![]()
I'd love to hear from someone that has done the roller bearing in the end plate aswell...
Actually Ruffy I have been considering off and on over the duration of this thread how to install a roller bearing. I have not actually seen an installation or had one described so have been starting from scratch. But here are my current thoughts.
Reducing the drum dia from 3½" to 2½" will increase the winch capacity from 8000Lbs to 10,400-10,800lbs depending on the wire diameter. (10,400lbs for 11mm synthetic). The maximum load on the bearing will occur when winching off the 1st layer from a position at the end of the drum where the bearing is. Allowing for the necessary 5 wraps on the drum gives a radial load on the bearing of approx 9,500lbs (say 4300Kg).
The bearing can be seated either in the end plate, or inside the drum. In both cases a "stub axle" will be required.
Locating inside the drum is better from the point of view of keeping the bearing clean, and also easier to locate the bearing but a 2½" drum with 8mm wall thickness say will only take a bearing of 47mm OD. From the NTN bearing catalogue (downloadable from their website) the heaviest roller bearing of this OD is a 47 OD x 18 wide on a 20mm shaft - 2890kgf static. So you will need 2. A 20mm shaft is also rather narrow - I haven't checked it out.
The other way is to locate the bearing in the end plate. This is 21mm wide with a 91mm dia hole. No bearing will exactly fit this so some form of sleeve will be required and also a method of locating the bearing so that it does not pop out. So you are looking for a bearing of about 80mm OD on a 30mm shaft. NTN do a 72mm OD x 19 mm wide x 30ID with a static radial load capacity of 5100kgf which looks about right.
And that's about as far as I have got. Other factors to consider are:
How to locate the bearing
How to seal it against mud and water
How to lubricate it
How to locate the sleeve in an external bearing set up
How to accommodate axial movements
How easy is the bearing to fit and replace
How to terminate the rope
etc!!
Any comments on the above thoughts woyuld be appreciated. David
1982 Patrol K160 SWB (MQ) 4L P40 Petrol with Megasquirt fuel injection and EDIS ignition. Warn 8274 winch with Gigglepin head
My lathe is a bit too small for this work but I intended to do a proper design and drawing and get quotes from local engineers for the machining work, or alternatively twist the arm of my younger brother who is a qualified toolmaker.Hales231271 wrote:David
Have you got all the machines , ie centre lathe, to do all this work yourself??
Cheers
Dazza
Cheers, David.
1982 Patrol K160 SWB (MQ) 4L P40 Petrol with Megasquirt fuel injection and EDIS ignition. Warn 8274 winch with Gigglepin head
I'll second that I've researched them for work. Does need a fair bit of air though but could work.Shadow wrote:i dont understand the whole seperate idea. Its not like there are two distinct temperature airs coming out of the compressor. It is air, all at one temp (effectively). To produce cold air you need to remove heat. How does a vortex do this?YankeeDave wrote:no, it actually seperates air with a vortex, and the amount of air you supply dictates final temp, you can supply bugger all air and it gets very cold, or lots of air for just cool air.
very impressive actually.
Build Thread - http://www.outerlimits4x4.com/viewtopic.php?f=16&t=168546&p=1927514&hilit=GRPABT1%27s+zook#p1927514
I had the drunm cut out and had a 1.5 inch solid steel shaft that is 3 inches longer installed. I use Masterpull rope rated at over 20,000 pounds - 125 feet - but could fit a lot more on.
Most of the winching I do still leaves alot of line on the drum as I don't usually have to pull long distances - so I am not concerned about a narrow drum as there is atleast a layer or 2 on the drum - this shit is tough and I am trying to break it - but no luck yet.
Also, securing it is important, I use a double clove hitch, a hole through the shaft and a rope protector sheath on the first 15 feet of rope, the line never slips.
Most of the winching I do still leaves alot of line on the drum as I don't usually have to pull long distances - so I am not concerned about a narrow drum as there is atleast a layer or 2 on the drum - this shit is tough and I am trying to break it - but no luck yet.
Also, securing it is important, I use a double clove hitch, a hole through the shaft and a rope protector sheath on the first 15 feet of rope, the line never slips.
Interesting that this thread has been resurrected. What did I do in the end? I didn't pursue the roller bearing as it was looking expensive and I would like to incorporate a freespool as well which will take a lot more thought.
So I just cut the splined end (with flange) off and grafted it onto a new shaft and end flange. New dimensions 12" wide by 2" long as shown below. Shaft was ex AISI 4140 HT bar drilled out at the outer end to allow for rope termination.
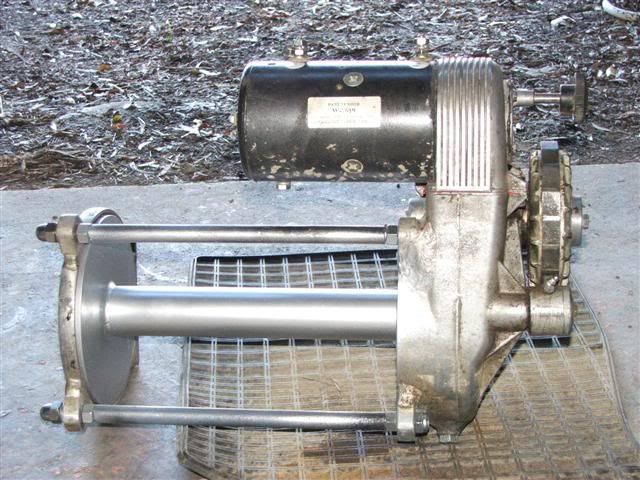
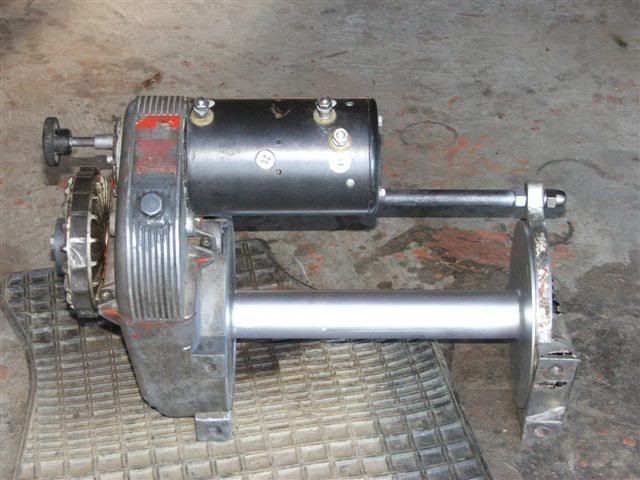
This has worked well with synthetic rope - 12mm Amsteel Blue though there have been two problems. Anchoring the rope was a bit tricky through a 16mm hole into the bored out shaft but can be done. We work on a minimum of five wraps on the drum. A bigger problem was that with slippery synthetic rope the sideways "wedging" effect is much greater than wire - so much so that the original Warn flange at the splined end bowed into a cone shape fouling the gear box and causing the oil to leak out. This was fixed by reinforcing the inside. The other end had a new 8mm thick flange and was fine.
From the pics you will note a few other standard mods I did at the same time - two lateral bars ex 12mm threaded rod, a positive collar and thread anchor to the brake and oil drain and fill holes. With the widened drum I consider the lateral bars essential to ensure the end flange is square to the shaft. I also put on a 7.8Hp motor with two Titan solenoids connected in parallel. And the roller fairlead was replaced with a stainless fairlead. In general the setup worked well.
Just recently I installed a Gigglepin head with two 7.8HP motors and a strengthened mainshaft. My old standard lead acid batteries were not really up to the twin motors so I splashed out and installed two Odyssey PC1500 AGM batteries along with a 130A alternator. This setup really pulls.
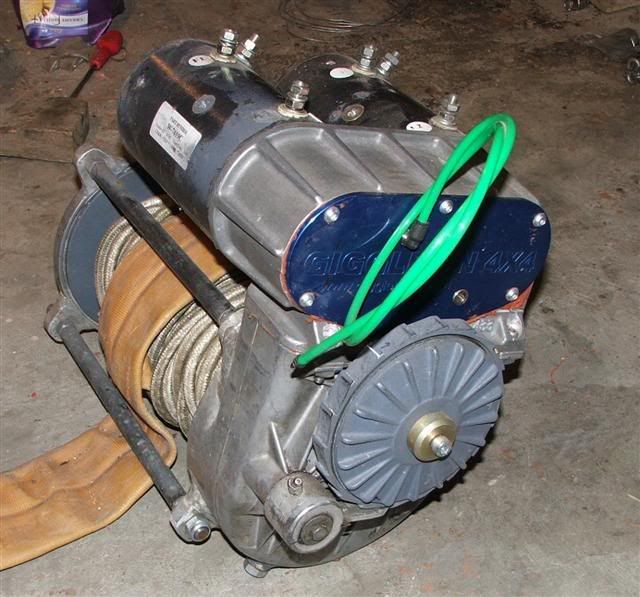
The picture shows it fitted with 9mm Dynex Dux overbraid which appears to be more abrasion resistant than the Amsteel but also more prone to kinks. The brown sleeve is a length of fire hose turned inside out which I use as an anti-abrasion sleeve when winching over banks etc. It also doubles as a UV protector when wound onto the drum.
So I just cut the splined end (with flange) off and grafted it onto a new shaft and end flange. New dimensions 12" wide by 2" long as shown below. Shaft was ex AISI 4140 HT bar drilled out at the outer end to allow for rope termination.
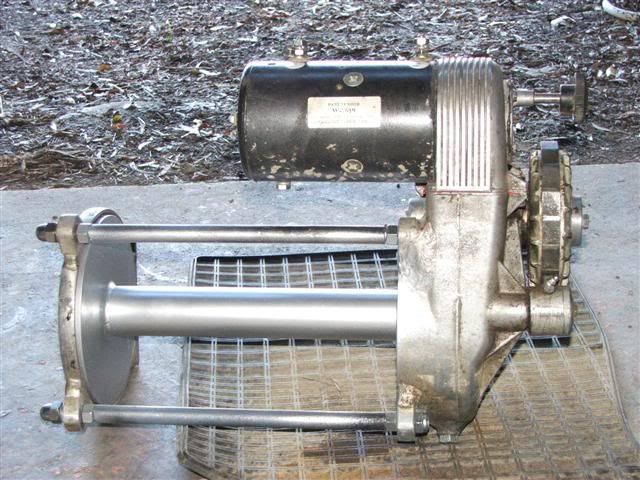
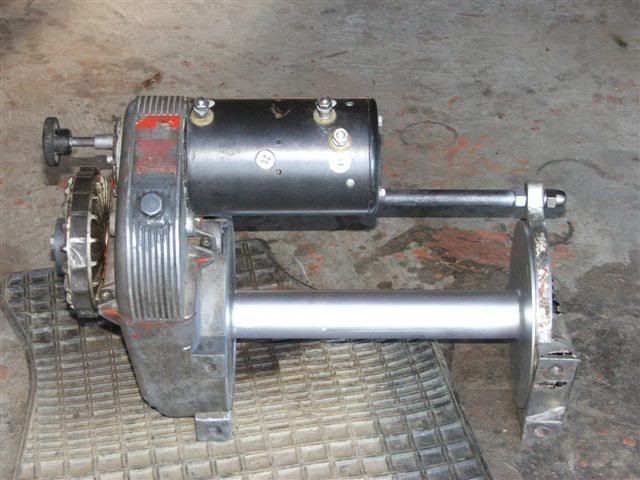
This has worked well with synthetic rope - 12mm Amsteel Blue though there have been two problems. Anchoring the rope was a bit tricky through a 16mm hole into the bored out shaft but can be done. We work on a minimum of five wraps on the drum. A bigger problem was that with slippery synthetic rope the sideways "wedging" effect is much greater than wire - so much so that the original Warn flange at the splined end bowed into a cone shape fouling the gear box and causing the oil to leak out. This was fixed by reinforcing the inside. The other end had a new 8mm thick flange and was fine.
From the pics you will note a few other standard mods I did at the same time - two lateral bars ex 12mm threaded rod, a positive collar and thread anchor to the brake and oil drain and fill holes. With the widened drum I consider the lateral bars essential to ensure the end flange is square to the shaft. I also put on a 7.8Hp motor with two Titan solenoids connected in parallel. And the roller fairlead was replaced with a stainless fairlead. In general the setup worked well.
Just recently I installed a Gigglepin head with two 7.8HP motors and a strengthened mainshaft. My old standard lead acid batteries were not really up to the twin motors so I splashed out and installed two Odyssey PC1500 AGM batteries along with a 130A alternator. This setup really pulls.
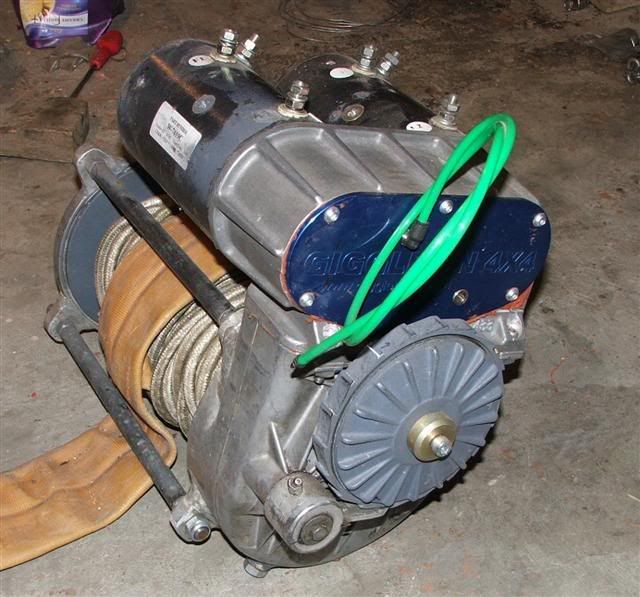
The picture shows it fitted with 9mm Dynex Dux overbraid which appears to be more abrasion resistant than the Amsteel but also more prone to kinks. The brown sleeve is a length of fire hose turned inside out which I use as an anti-abrasion sleeve when winching over banks etc. It also doubles as a UV protector when wound onto the drum.
1982 Patrol K160 SWB (MQ) 4L P40 Petrol with Megasquirt fuel injection and EDIS ignition. Warn 8274 winch with Gigglepin head
Keep in mind the bearing ratings are at 100% duty cycle for the lifetime of the bearing.
A winch is not a high duty cycle item - and is damped somewhat by the rope from shock loading.
You could probably overload the roller or ball bearing significantly without coming close to it's lifespan.
Paul
A winch is not a high duty cycle item - and is damped somewhat by the rope from shock loading.
You could probably overload the roller or ball bearing significantly without coming close to it's lifespan.
Paul
Lexus LX470 - hrrm Winter Tyres
Gone - Cruiser HZJ105 Turbo'd Locked & Lifted
Gone - 3L Surf
Gone - Cruiser HZJ105 Turbo'd Locked & Lifted
Gone - 3L Surf
The 7.8HP are Superduty motors. In New Zealand they are supplied by Traxion . For details go to http://www.traxion.co.nz/product/details.asp?pid=16benhl wrote:what are these 7.8hp motors you speak of?? I though 6hp was the ducks nutz
They certainly pull and do run cool. They are not any faster than the standard motors so with the Gigglepin I have installed a +13% gear set which helps and will probably change to +25%. However I have not been overly impressed by the build quality of the Superduty motors. They claim to be made in the USA but there is no actual marking on the motor to support this and mine came fitted with Chinese bearings which I did not think a good sign.

The first motor stopped after 6 months and when we opened it up we found a lot of corrosion and one of the internal screws had come loose. 6 months later it stopped again and we had to completely strip it, clean it and put insulating "rubber" on the windings insulation. Maybe this was just an isolated case but when it came to adding the second motor I seriously contemplated going back to two Warn 6HP. However I opted for a second 7.8HP. I have had no problems so far with this one and it did seem to be of better quality than the first. However before using it I stripped it down and painted the inside of the casing (it was unpainted), sealed all the screw holes, loctited the screws and used the paint-on "rubber" insulation on all terminals.
I would be interested to hear if anyone else has had similar problems. (To be fair I must point out that Traxion have been very helpful and offered to replace the first motor if it had been other than a loose screw)
1982 Patrol K160 SWB (MQ) 4L P40 Petrol with Megasquirt fuel injection and EDIS ignition. Warn 8274 winch with Gigglepin head
Where is the Dynex rope available from? Looks to be more resistant to dirt ingress from when I have seen it in action. Might be an option when I upgrade.David_S wrote:
The picture shows it fitted with 9mm Dynex Dux overbraid which appears to be more abrasion resistant than the Amsteel but also more prone to kinks.
The Dynex Coverbraid is made by Hampidjan of Iceland for the fishing industry. I got mine from Hampidjan NZ in Nelson but they are sure to have sales outlets in Australia - yacht riggers and fishing industry supplies etc. There are a lot of data sheets on http://www.hampidjan.co.nz/ Just look under Dynex.Mudzuki wrote:Where is the Dynex rope available from? Looks to be more resistant to dirt ingress from when I have seen it in action. Might be an option when I upgrade.
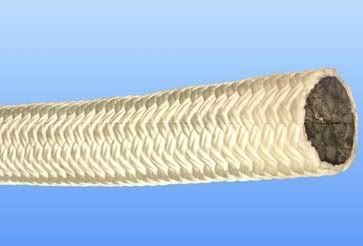
It was not cheap but it is good and as they say
I tend to use my 12mm Amsteel Blue for the occasional winch challenge and the like as it is easier to handle, slightly stronger - 14,800Kg for 12mm Amsteel v 12,000 kg for the 9mm Dynex - and does not kink. For everyday use I use the Dynex and am very pleased with it. Because of its stiffness you just have to check for potential kinks before winding in but you should do that anyway. I am not sure how you would splice it if you had too - have never had to do it - but there is probably a simple way.Coverbraided Dynex is extremely tough against abrasion and will ensure much longer lifetime of the rope in harsh environment. The overbraiding will keep the rope round and very stiff which is important in some applications.
David
1982 Patrol K160 SWB (MQ) 4L P40 Petrol with Megasquirt fuel injection and EDIS ignition. Warn 8274 winch with Gigglepin head
Not sure where you can buy it in Australia but when I googled "Dynex Dux 75 au" I came up with a lot of places such as yacht riggers including for example http://www.ropewa.com.au which has a 4wd winch section. But don't expect it to be cheapbenhl wrote:can anyone provide an australian distributor of Dynex and 1 better a price of some sort??

And you should go for the Dynex Dux 75 not the Dynex 75 which is not as strong, and the coverbraid if you want the abrasion resistant sheath.
1982 Patrol K160 SWB (MQ) 4L P40 Petrol with Megasquirt fuel injection and EDIS ignition. Warn 8274 winch with Gigglepin head
Who is online
Users browsing this forum: No registered users and 2 guests