Page 7 of 11
Re: The Welding Thread
Posted: Wed Oct 05, 2011 5:53 pm
by 5inchgq
94lux wrote:5inchgq wrote:
Mate I don't want to start a shit fight but it might be worth pointing out that the weld you posted was done on two pieces that were joined at 90 deg where as Dudelux's welds are joining two bits of steel together in a flat style, a whole different kettle of fish IMO........
Pfft hardly different champ, im only an amateur welder that was offering another amteur some advice that i thought may help. I was showing a weld i was proud of that still required "a steady hand and consistant travel speed". If you dont wanna start a shit fight....dont comment

Hardly different ??? In my experience welding two bits of flat steel together as pictured will usually give a 'taller' weld than welding two bits of steel at right angles to each other, unless the two pieces of flat steel have been prepped (ie ground at 45 deg).
Your weld looked good I didn't knock it, I was just offering my opinion.

Re: The Welding Thread
Posted: Wed Oct 05, 2011 6:58 pm
by Struth
Dudelux did a butt weld and the second one is a fillet weld. They have different names because they are different welds.
Fillet welds are easier than butts, the fillet weld shown looks OK though.
Butt welds require more preparation, each face should be ground at a 30* angle and a root gap left between the two pieces of steel, once this is done you will find it easy to do nice butt welds.
Re: The Welding Thread
Posted: Wed Oct 05, 2011 7:38 pm
by 5inchgq
Thanks Struth

that is exactly what I was trying to say in my garbled ramble ......
Just out of curiosity whats the difference between a 30 deg prep and a 45 ?? Apart from the extra 15 deg ??? I was under the impression that for a but weld a 45 deg prep will work well if, for instance it is approximately 50 % of the parent material ? Does that make sense ?? Ie a 6mm piece with an approximately 3mm prep grind at 45 deg.
Re: The Welding Thread
Posted: Wed Oct 05, 2011 9:03 pm
by Struth
5inchgq wrote:Thanks Struth

that is exactly what I was trying to say in my garbled ramble ......
Just out of curiosity whats the difference between a 30 deg prep and a 45 ?? Apart from the extra 15 deg ??? I was under the impression that for a but weld a 45 deg prep will work well if, for instance it is approximately 50 % of the parent material ? Does that make sense ?? Ie a 6mm piece with an approximately 3mm prep grind at 45 deg.
Makes sense, but with a 30* right down to a small root face you will get full penetration at the root of the weld.
That's 30 each side for an included angle of 60
Re: The Welding Thread
Posted: Wed Oct 05, 2011 9:41 pm
by DUDELUX
So you guys like my welding then??
I didnt grind out anything, just gave both pieces a hit with the wire brush. Im pretty happy with how it came out.
Yes, I need more practice, but I havent been welding for very long, so Im happy.
But if I was welding anything apart from some scrap, I wouldve more than likely gone to more effort to make sure I had prepared the steel. But it was just some scrap that my mate left me, for practicing on.
Re: The Welding Thread
Posted: Wed Oct 05, 2011 10:22 pm
by tehekho
DUDELUX wrote:So you guys like my welding then??
I didnt grind out anything, just gave both pieces a hit with the wire brush. Im pretty happy with how it came out.
Yes, I need more practice, but I havent been welding for very long, so Im happy.
But if I was welding anything apart from some scrap, I wouldve more than likely gone to more effort to make sure I had prepared the steel. But it was just some scrap that my mate left me, for practicing on.
You would have had a bit of a chamfer on the corner of the steel anyway, giving you the fillet to an extent - wouldn't have been perfect but would have helped. Good that you cleaned it up with a wire brush. It's incredible the difference preparation makes.
Re: The Welding Thread
Posted: Thu Oct 06, 2011 6:32 am
by uninformed
would it be correct in saying that you dont need to grind any relief angle on any material under 3mm thick? also I believe that it is only at 3mm and above you start to leave a gap between for butt joins???
Re: The Welding Thread
Posted: Thu Oct 06, 2011 8:15 am
by Struth
uninformed wrote:would it be correct in saying that you dont need to grind any relief angle on any material under 3mm thick? also I believe that it is only at 3mm and above you start to leave a gap between for butt joins???
Always grind a prep and leave a small root gap, then set the welder appropriately to weld the steel and prep. You could get away with just a root gap on 3mm and under though.
EG: When capping the ends of 2" tube I cut a 1.6mm thick disc from some sheetmetal, leave it about 1mm a side smaller than the inside of the tube, then weld. That way I get full peno and can grin the weld flush for looks.
Re: The Welding Thread
Posted: Thu Oct 06, 2011 9:45 am
by 80's_delirious
Hey Struth, how much gap would you leave with say 6mm material if you've also bevelled off the edges?
Dudelux, preparation can make a big difference to your weld quality, especially with a small 240 volt welder, they don't have the grunt to burn through paint and scale etc. I like using flap discs on a grinder to quickly clean up edges etc before welding
Re: The Welding Thread
Posted: Thu Oct 06, 2011 10:56 am
by Struth
80's_delirious wrote:Hey Struth, how much gap would you leave with say 6mm material if you've also bevelled off the edges?
Dudelux, preparation can make a big difference to your weld quality, especially with a small 240 volt welder, they don't have the grunt to burn through paint and scale etc. I like using flap discs on a grinder to quickly clean up edges etc before welding
Leave a 2mm high root face (only bevel far enough to still have 2mm of flat surface on each piece) and a 2mm wide root gap.
Cheers
Re: The Welding Thread
Posted: Thu Oct 06, 2011 12:31 pm
by 80's_delirious
Cheers Struth
Re: The Welding Thread
Posted: Sun Oct 09, 2011 9:26 am
by ZOOK60
This is the first weld I have done with the licoln electric 180c.
It has a handy chart all you do is hold the material against the chart and what size wire and it tells you
on the chart what settings to put it on. This weld is 2 bits of 5mm with gasless wire.
Im by no means a pro welder Im just self taught so dont laugh too hard.
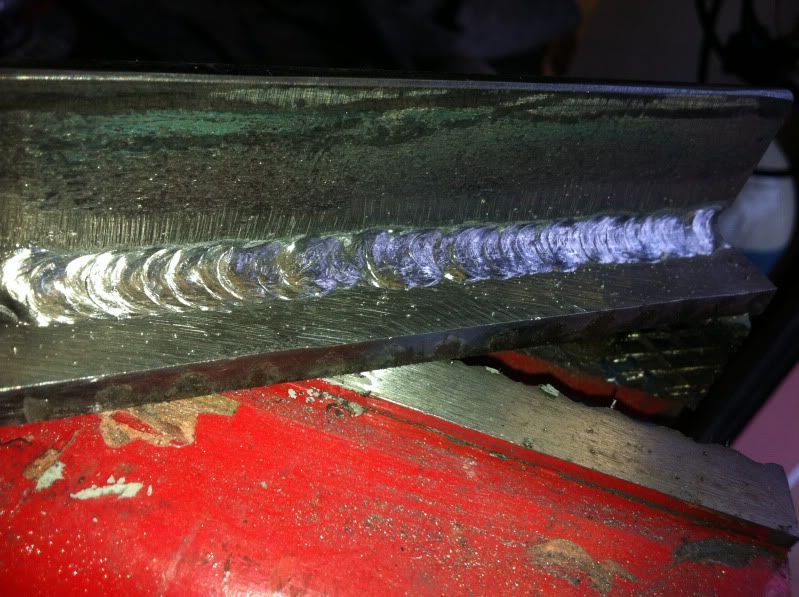
Re: The Welding Thread
Posted: Mon Oct 10, 2011 12:02 am
by DUDELUX
Is that chart the one under the lid??
Ive seen the chart, but never really looked at it.

Re: The Welding Thread
Posted: Mon Oct 10, 2011 8:37 pm
by ZOOK60
DUDELUX wrote:Is that chart the one under the lid??
Ive seen the chart, but never really looked at it.

Yep thats the one give it ago it works pretty well.
Re: The Welding Thread
Posted: Mon Oct 10, 2011 11:01 pm
by 80's_delirious
found a helpful site tonight, lots of good videos and tips for different welding methods
http://www.weldingtipsandtricks.com
Re: The Welding Thread
Posted: Wed Oct 12, 2011 9:10 pm
by 5inchgq
Bookmarked..... Nice find.

Re: The Welding Thread
Posted: Wed Oct 12, 2011 9:13 pm
by 80's_delirious
Yep, thought it was worth sharing, good simple explanations and good clear videos
Re: The Welding Thread
Posted: Thu Oct 13, 2011 3:46 pm
by bru21
Bit of a hijack but - are there any welding certificates worth doing - eg chassis welding etc, I am looking at turning a few of my skills into paper, as you never know when yous might need them later on. I'm talking about automotive etc not pipe lines etc,
cheers bru
Re: The Welding Thread
Posted: Thu Oct 13, 2011 4:11 pm
by bru21
Fark these are good! My little bro bought one much to my disgust - and when I used it I apologised to him and said it's awesome!
I might buy one for the smaller jobs!
Re: The Welding Thread
Posted: Thu Oct 13, 2011 5:34 pm
by nayto
Anyone who has the Lincoln 180c, does it use a standard 10Amp plug or 15 Amp?
Re: The Welding Thread
Posted: Thu Oct 13, 2011 6:30 pm
by ZOOK60
nayto wrote:Anyone who has the Lincoln 180c, does it use a standard 10Amp plug or 15 Amp?
It uses a 15 amp plug but I have made up an adaptor so I can plug it into the 10amp power lead.
Im running mine on a 30m 10amp lead from the back of the house and it seems to work pretty well.
Re: The Welding Thread
Posted: Thu Oct 13, 2011 9:52 pm
by DUDELUX
I got my neighbour to put in a 15A plug specially for the welder to run off. Hes a sparky, did it for a slab.
I was told not to run it off 10A.
Re: The Welding Thread
Posted: Fri Oct 14, 2011 12:26 pm
by phippsy
bru21 wrote:
Fark these are good! My little bro bought one much to my disgust - and when I used it I apologised to him and said it's awesome!
I might buy one for the smaller jobs!
I can get a price on one of these if you want, we have an account with Aitkens and they are trying to get more of our business
Re: The Welding Thread
Posted: Fri Oct 14, 2011 8:58 pm
by ledgend80
the price i got it from aitken was 1550 from memory
Re: The Welding Thread
Posted: Wed Jan 04, 2012 4:04 pm
by loosecanon
Hi guys,
I haven't had the time to read this whole thread but I did search, so brownie points for me.
Wondering if someone could give so knowledgeable input to welding sheet 1.6mm or so, for panels. What type of welds, the best way to achieve the best results ect, ect.
I have successfully done this before but I am still a novice compared to most of the people in this thread, was hopping to learn something to make it easier and a better end result.
Cheers.
Re: The Welding Thread
Posted: Fri Mar 30, 2012 4:38 pm
by Chook91
Howdy Outers. Name's Chook and I am a first year (approx 9mnths in) boilermaker/fabricator. Just started work at a new place here in Adelaide so I am cheering. By the way if anyone is looking for welding work here in Adelaide, particularly around the northern suburbs then please pm me. There is one place which needs to be avoided at all costs.
Back to the welding, we generally use 3phase welders in the workshop although we do have a couple of Cigweld 350 MIG welders that run off 240v. Had some scrap under my bench so I thought I'd glue them together and see what everyone thinks.
6mm upright welded to 8mm base plate. I have approx 2000 of these brackets to make

8mm upright to 10mm plate

8mm upright to 6mm base

8mm to 8mm

and although ive never tried it (never needed to) i tried the famed tac-tac-tac weld on some more scrap. please note that this piece is never going to be used for anything, nor would i do this type of weld on anything structural. this was just me goofing around.
Lemme know what you guys think!
Now, where did the bar fridge get to....
Re: The Welding Thread
Posted: Fri Mar 30, 2012 6:26 pm
by hj 45
^^^cool.
I'm giving serious thought to buying a new Esab 200 amp inverter mig. Reports seem very positive. Anyone here used one?
Re: The Welding Thread
Posted: Sat Mar 31, 2012 6:50 pm
by TURBO LS2
So out of all the fabricators that come on this site who actually is a qualified welder/boily? I see quite a few people use pulse on their mig welders for doing cage work. Pulse welding at semi long pulse intervals are not strong welds. I would never weld someone elses work with this method.
Re: The Welding Thread
Posted: Sat Mar 31, 2012 8:08 pm
by UNJUST
Re: The Welding Thread
Posted: Sun Apr 01, 2012 7:16 am
by awill4x4
UNJUST wrote:
also a pic of my turbo manifold I tig welded (purged) with a technique that is know to me as "walking the dog" !! well thats what my mate calls it who is a contract tig welder
It's actually called "walking the cup".
Regards Andrew.