Notice: We request that you don't just set up a new account at this time if you are a previous user.
If you used to be one of our moderators, please feel free to reach out to Chris via the facebook Outerlimits4x4 group and he will get you set back up with access should he need you.
If you used to be one of our moderators, please feel free to reach out to Chris via the facebook Outerlimits4x4 group and he will get you set back up with access should he need you.
Recovery:If you cannot access your old email address and don't remember your password, please click here to log a change of email address so you can do a password reset.
Dual Battery system to protect ECU whilst winching
Moderator: -Scott-
Dual Battery system to protect ECU whilst winching
Whilst winching up a long steep slope at the weekend with some rather tired batteries the drop in voltage was such that the Electronic Control Unit was affected causing misfiring, leaning out and backfiring.
The current draw of the Ecu is quite small so I am considering installing a third small (motorcycle size ) 8AH battery dedicated to the ecu. What I would like to achieve is this.
Under ordinary use the two winching/starter batteries and the ecu battery would be charged together in parallel. When winching, as soon as the voltage dropped significantly, the ECU battery would be isolated so that the ECU would run on an independent power source. On completion of winching the ECU battery would be charged first (which would not take long) and then the starter/winching batteries.
The easiest (?) way to achieve this would be with manually operated relays which would direct the charging current to either the starter/winch battery circuit or the ECU battery circuit or both as required. I would need a voltmeter on the ECU battery to monitor it's charge. But is there a way this could be done automatically without running the risk of the ECU battery draining into the winch batteries?
Standard 4wd battery isolation systems such as the Redarc are not appropriate (as far as I can ascertain) as they are designed to isolate the starter battery when using the auxiliary battery to run the fridge etc and to charge the starter battery first. I don't want to switch the alternator feed to the ECU battery as I want to use it's output to assist the batteries when winching.
Any ideas anyone without going overboard with 2nd alternators and extensive rewiring etc.
David
The current draw of the Ecu is quite small so I am considering installing a third small (motorcycle size ) 8AH battery dedicated to the ecu. What I would like to achieve is this.
Under ordinary use the two winching/starter batteries and the ecu battery would be charged together in parallel. When winching, as soon as the voltage dropped significantly, the ECU battery would be isolated so that the ECU would run on an independent power source. On completion of winching the ECU battery would be charged first (which would not take long) and then the starter/winching batteries.
The easiest (?) way to achieve this would be with manually operated relays which would direct the charging current to either the starter/winch battery circuit or the ECU battery circuit or both as required. I would need a voltmeter on the ECU battery to monitor it's charge. But is there a way this could be done automatically without running the risk of the ECU battery draining into the winch batteries?
Standard 4wd battery isolation systems such as the Redarc are not appropriate (as far as I can ascertain) as they are designed to isolate the starter battery when using the auxiliary battery to run the fridge etc and to charge the starter battery first. I don't want to switch the alternator feed to the ECU battery as I want to use it's output to assist the batteries when winching.
Any ideas anyone without going overboard with 2nd alternators and extensive rewiring etc.
David
1982 Patrol K160 SWB (MQ) 4L P40 Petrol with Megasquirt fuel injection and EDIS ignition. Warn 8274 winch with Gigglepin head
use a smart isolator, and turn your ignition line off when winching
effectively cutting the link between your prim. and aux batt .... or buy bigger battery's, how ever if you have a red arc solenoid, put a switch in your dash that controls the 12V ign line on it
that will isolate your problems and your ecu wont die in hysterics


Maverick. Unlocked on 35's MOTTO: Lock, Stomp & Hold on
I'm trying to get my head around this but surely if the power drain is that bad, if you stall there wouldnt be enough juice to crank it over ? Which batt do you winch from ? power for the ignition / coil wont come from the ecu directly so i would think its just a case of not large enough battery being used ? I'm no expert but thats just how i read it.
Saddle up tonto, its the not so loanrangie! . 98 TDI DISCO lightly modded with more to come.
I have been giving this further thought and think I will end up using a voltage sensitive relay such as the Redarc Smart Start located on the alternator to battery feed. This will work as follows.
In normal use the relay will be closed and winch and ecu batteries will be charged in parallel. When winching as soon as the ecu battery drops below 12.5 volts the relay will open isolating the ecu battery. The ecu will now run off battery power only and the alternator will continue to feed the winch battery to assist in winching and to charge the winch batteries on completion of winching. As soon as the winch batteries come up to 13.2V the relay will close and both batteries will now be charged in parallel.
I will have to check what the ecu current demand is - the load is the ecu itself, electric fuel pump, injectors, and LC1 O2 controller - probably around 3-5 amps to see how long the ecu battery will last.
Although I wrote winch "battery" the winch/starter battery is in fact two 70AH batteries in parallel so I will end up with a three battery system. The two 70AH batteries have been fine in the past but are now at the end of their life so I am replacing them with AGM batteries which combine the characteristics of deep cycle and starter batteries. I am also upgrading the alternator to 130A.
Cheers
David
In normal use the relay will be closed and winch and ecu batteries will be charged in parallel. When winching as soon as the ecu battery drops below 12.5 volts the relay will open isolating the ecu battery. The ecu will now run off battery power only and the alternator will continue to feed the winch battery to assist in winching and to charge the winch batteries on completion of winching. As soon as the winch batteries come up to 13.2V the relay will close and both batteries will now be charged in parallel.
I will have to check what the ecu current demand is - the load is the ecu itself, electric fuel pump, injectors, and LC1 O2 controller - probably around 3-5 amps to see how long the ecu battery will last.
Although I wrote winch "battery" the winch/starter battery is in fact two 70AH batteries in parallel so I will end up with a three battery system. The two 70AH batteries have been fine in the past but are now at the end of their life so I am replacing them with AGM batteries which combine the characteristics of deep cycle and starter batteries. I am also upgrading the alternator to 130A.
Cheers
David
1982 Patrol K160 SWB (MQ) 4L P40 Petrol with Megasquirt fuel injection and EDIS ignition. Warn 8274 winch with Gigglepin head
I don't think you need to overthink this. If you can isolate the ECU circuit, maybe at the fuse, an ordinary "smart" (ie voltage sensitive) dual battery controller will do the job for you.
It will jsut need to be wired up as normal, when the alternator/main batt voltage is good, everything will be connected together, and when you start winching etc and the main system voltage drops down, your ECU will be isolated and maintain 12V plus.
But, you need to be sure you have the circuit completely separate, if you accidentally hook back into some other 12V stuff via an injector relay or whatever, it won't work.
Another option would be to use a good voltage regulator that is capable of upping the voltage to the ECU if necessary. Something that will take anything from 10-14V and put out a consistent 12V no matter what. eg you could buy an automotive laptop power supply and hardwire it in. Possibly cheaper and better overall provided you can find one that will up the voltage if it does drop below 12V as well as drop it.
My only query is, are you sure you didn't just have a weak spark problem when the voltage dropped, ie nothing to do with the ECU at all?
It will jsut need to be wired up as normal, when the alternator/main batt voltage is good, everything will be connected together, and when you start winching etc and the main system voltage drops down, your ECU will be isolated and maintain 12V plus.
But, you need to be sure you have the circuit completely separate, if you accidentally hook back into some other 12V stuff via an injector relay or whatever, it won't work.
Another option would be to use a good voltage regulator that is capable of upping the voltage to the ECU if necessary. Something that will take anything from 10-14V and put out a consistent 12V no matter what. eg you could buy an automotive laptop power supply and hardwire it in. Possibly cheaper and better overall provided you can find one that will up the voltage if it does drop below 12V as well as drop it.
My only query is, are you sure you didn't just have a weak spark problem when the voltage dropped, ie nothing to do with the ECU at all?
This is not legal advice.
They do but it should be running off a relay triggered by the ecu.chimpboy wrote:ps I dunno about leaving the fuel pump in the protected part of the system, I would assume they draw a reasonable amount of current.
Saddle up tonto, its the not so loanrangie! . 98 TDI DISCO lightly modded with more to come.
I agree but my main concern is whether the small ecu battery will team up with two larger batteries and 130A alternator. For the ecu battery I propose using the Odyssey PC310 which supposedly can handle large charging currents. Quote from the Odyssey Owner's Manualchimpboy wrote:I don't think you need to overthink this. If you can isolate the ECU circuit, maybe at the fuse, an ordinary "smart" (ie voltage sensitive) dual battery controller will do the job for you.
We will seeAlso, with simple constant voltage charging (alternator or independent charger), there is no limitation on the inrush current, so the user is assured of fast charge recovery.

When I wired up the megasquirt I kept the ecu, fuel pump and injectors on one circuit with a central relay box so it can be readily isolated.But, you need to be sure you have the circuit completely separate, if you accidentally hook back into some other 12V stuff via an injector relay or whatever, it won't work.
It is necessary to keep it within the system as it is controlled via the Megasquirt - it purges the fuel lines of air by running the pump for a few secs when the ignition is switched on. I have just checked the current draw as follows.ps I dunno about leaving the fuel pump in the protected part of the system, I would assume they draw a reasonable amount of current.
Fuel pump 2.5A
Megasquirt Negligible
Injectors 1-2A depending on rpm
At 3000rpm the total draw is 4A
so an 8AH battery should last a while.
Good point but I never had a problem till I installed the ecu. Still it is a possibility but ecu's definitely don't like low voltages so isolating the ecu circuit is not a waste of time and a good place to start.My only query is, are you sure you didn't just have a weak spark problem when the voltage dropped, ie nothing to do with the ECU at all?
Thanks for your comments/suggestions
David
1982 Patrol K160 SWB (MQ) 4L P40 Petrol with Megasquirt fuel injection and EDIS ignition. Warn 8274 winch with Gigglepin head
David, your ECU battery will only attempt to draw a large charge current if it is deeply discharged. At a guess, I'd say you'd need to be winching literally non-stop for more than 30 minutes before you start to worry about your ECU battery in-rush current. Can your existing system winch non-stop for 30 minutes?David_S wrote:I agree but my main concern is whether the small ecu battery will team up with two larger batteries and 130A alternator. For the ecu battery I propose using the Odyssey PC310 which supposedly can handle large charging currents. Quote from the Odyssey Owner's Manualchimpboy wrote:I don't think you need to overthink this. If you can isolate the ECU circuit, maybe at the fuse, an ordinary "smart" (ie voltage sensitive) dual battery controller will do the job for you.
We will seeAlso, with simple constant voltage charging (alternator or independent charger), there is no limitation on the inrush current, so the user is assured of fast charge recovery.!
My existing system with dud batteries - DEFINITELY NO. My new system with new Odyssey batteries - Better (I hope) but NO too-Scott- wrote:
David, your ECU battery will only attempt to draw a large charge current if it is deeply discharged. At a guess, I'd say you'd need to be winching literally non-stop for more than 30 minutes before you start to worry about your ECU battery in-rush current. Can your existing system winch non-stop for 30 minutes?

Thanks for the reassuring comment about the in-rush current.
David
PS Had a new thought.


1982 Patrol K160 SWB (MQ) 4L P40 Petrol with Megasquirt fuel injection and EDIS ignition. Warn 8274 winch with Gigglepin head
macca81 wrote:just go spend some coin on a cpl of GOOD betteries, and be done with it
Don't you consider Odyssey batteries good?I wrote:My existing system with dud batteries - DEFINITELY NO. My new system with new Odyssey batteries - Better (I hope) but NO too
David
1982 Patrol K160 SWB (MQ) 4L P40 Petrol with Megasquirt fuel injection and EDIS ignition. Warn 8274 winch with Gigglepin head
Thought I would update this thread with what I finally did.
I installed 2 Odyssey PC1200 batteries (each 44AH) connected in parallel as my main batteries - for winch and lights
I also installed a third Odyssey PC 535 (14.8AH) battery (motorcycle size) to run the Megasquirt ecu, fuel pump, LC1 O2 controller and ignition. This was connected in parallel with the PC1200s but with a 50A diode ( actually a $15 bridge rectifier from Dick Smith) on the +ve connection to prevent backfeed from the PC535 to the PC1200s when they are drained during winching.
A 130A alternator feeds all batteries.
The system works as follows. The alternator charges all batteries but because of the forward voltage loss through the diode (approx 0.6V) the PC535 is charged to 0.6V less than the main batteries. When winching the alternator supplies its full amperage to the winch motors (twin 7.8HP) and the PC1200 batteries make up the difference with a corresponding voltage drop. The PC535 supplies current to the megasquirt ecu etc. On completion of winching the alternator recharges the winch batteries until their voltage rises to approx 0.6V above the ecu battery and then charges all batteries together.
We tried the system out for the first time over the weekend during a local winch challenge and it seemed to work well with no hiccups from the ignition or ecu and the winch pulling well all day.
The Delco Remy 21SI alternator originally caused us some concern as it's output was only 13.8V whereas the Odyssey batteries require some 14.5V for rapid charging from low voltage followed by a trickle charge of 13.8V. We managed to up the output voltage of the alternator to 14.6V by inserting a couple of diodes before the voltage regulator and we also put in a relay so that by the flick of a switch we could bypass the diodes and drop the output back to 13.8V for normal trickle charging. We installed a multimeter in the cab so we could monitor the voltage during the day.
This system is overkill for normal offroad work with only the occasional winching session and we will probably remove the PC535 for normal use as with the 0.6V drop over the diode the battery may never be fully charged which might damage it. We could just bypass the diode but I am not sure how the PC535 would like being connected permanently in parallel with the larger PC1200s. My other concern is whether the PC1200s are big enough for a prolonged winching session. At the weekends the winching sections were quite short with time for the alternator to recharge the batteries between sessions. I will have to test it on a long steep hill I know.
I know it would be nice to keep the winch batteries completely separate through the use of two alternators but I am not prepared to give up my air conditioning just to free up a crankshaft pulley
Any comments on the above system would be appreciated.
David
I installed 2 Odyssey PC1200 batteries (each 44AH) connected in parallel as my main batteries - for winch and lights
I also installed a third Odyssey PC 535 (14.8AH) battery (motorcycle size) to run the Megasquirt ecu, fuel pump, LC1 O2 controller and ignition. This was connected in parallel with the PC1200s but with a 50A diode ( actually a $15 bridge rectifier from Dick Smith) on the +ve connection to prevent backfeed from the PC535 to the PC1200s when they are drained during winching.
A 130A alternator feeds all batteries.
The system works as follows. The alternator charges all batteries but because of the forward voltage loss through the diode (approx 0.6V) the PC535 is charged to 0.6V less than the main batteries. When winching the alternator supplies its full amperage to the winch motors (twin 7.8HP) and the PC1200 batteries make up the difference with a corresponding voltage drop. The PC535 supplies current to the megasquirt ecu etc. On completion of winching the alternator recharges the winch batteries until their voltage rises to approx 0.6V above the ecu battery and then charges all batteries together.
We tried the system out for the first time over the weekend during a local winch challenge and it seemed to work well with no hiccups from the ignition or ecu and the winch pulling well all day.
The Delco Remy 21SI alternator originally caused us some concern as it's output was only 13.8V whereas the Odyssey batteries require some 14.5V for rapid charging from low voltage followed by a trickle charge of 13.8V. We managed to up the output voltage of the alternator to 14.6V by inserting a couple of diodes before the voltage regulator and we also put in a relay so that by the flick of a switch we could bypass the diodes and drop the output back to 13.8V for normal trickle charging. We installed a multimeter in the cab so we could monitor the voltage during the day.
This system is overkill for normal offroad work with only the occasional winching session and we will probably remove the PC535 for normal use as with the 0.6V drop over the diode the battery may never be fully charged which might damage it. We could just bypass the diode but I am not sure how the PC535 would like being connected permanently in parallel with the larger PC1200s. My other concern is whether the PC1200s are big enough for a prolonged winching session. At the weekends the winching sections were quite short with time for the alternator to recharge the batteries between sessions. I will have to test it on a long steep hill I know.
I know it would be nice to keep the winch batteries completely separate through the use of two alternators but I am not prepared to give up my air conditioning just to free up a crankshaft pulley

Any comments on the above system would be appreciated.
David
1982 Patrol K160 SWB (MQ) 4L P40 Petrol with Megasquirt fuel injection and EDIS ignition. Warn 8274 winch with Gigglepin head
It sounds like a well planned system.
Don't worry about connecting a small battery in parallel with two large batteries. If they're all the same chemistry and same nominal voltage, it doesn't make any difference. (If you're really concerned, search here for info on charging batteries in parallel - Paul posted some excellent info.) The only issue which would concern me (and I'm not sure it would concern me much) is the prospect of a heavy load on your main batteries attempting to draw from the small battery - but that's the point of your isolation.
In place of the diode, you could consider a solenoid switched by a voltage sensing relay (VSR) - do a search, Chimpboy found a nice LandRover (?) voltage sensing relay which will close when sensed voltage is above 12.x volts, and open below that. Use one of these (sensing direct from one of your big batteries) to energise the solenoid and join all three batteries together. When winching, the terminal voltage of the winch batteries will drop, causing the VSR to open and isolate your small battery. Once main battery voltage comes back up, batteries will be connected again.
Don't worry about connecting a small battery in parallel with two large batteries. If they're all the same chemistry and same nominal voltage, it doesn't make any difference. (If you're really concerned, search here for info on charging batteries in parallel - Paul posted some excellent info.) The only issue which would concern me (and I'm not sure it would concern me much) is the prospect of a heavy load on your main batteries attempting to draw from the small battery - but that's the point of your isolation.

In place of the diode, you could consider a solenoid switched by a voltage sensing relay (VSR) - do a search, Chimpboy found a nice LandRover (?) voltage sensing relay which will close when sensed voltage is above 12.x volts, and open below that. Use one of these (sensing direct from one of your big batteries) to energise the solenoid and join all three batteries together. When winching, the terminal voltage of the winch batteries will drop, causing the VSR to open and isolate your small battery. Once main battery voltage comes back up, batteries will be connected again.
You could put a switch in series with power to your winch solenoids (stops anyone using your winch whilst parked etc) and then use the down-stream side of the switch to call a NC relay between your main and ECU batteries.
Should be cheaper than a VSR, more reliable/easily repaired in the field, and give added winch-use protection.
ed
Should be cheaper than a VSR, more reliable/easily repaired in the field, and give added winch-use protection.
ed
We did consider this as it appears simple but rejected it asThylacine wrote:You could put a switch in series with power to your winch solenoids (stops anyone using your winch whilst parked etc) and then use the down-stream side of the switch to call a NC relay between your main and ECU batteries. Should be cheaper than a VSR, more reliable/easily repaired in the field, and give added winch-use protection.
1) Every time you stopped winching, even momentarily (and this happens many times during a typical winching session), the small battery at a high voltage would be connected to the main batteries at a lower voltage with a consequent high current flow from the small to the large. The resultant (rapid in this case) voltage drop in the small battery is what we are trying to avoid.
2) We wanted the alternator to put its maximum effort into recharging the winch batteries first to be ready for the next winching session. (The Odyssey batteries apparently can take a very high charging current)
3) We already have protection against misuse of the winch as the winch controls are all wired to the ignition switch (IGN and ACC) and not to the +ve feed to the winch motors as with the original solenoid pack. Both our Titan solenoid packs (working well Paul) are under the bonnet
Thanks Ed for your suggestion though. It is an interesting problem and there is always the nagging thought that there must be a simpler way or that you have overlooked something so it is good to have feedback. In fact apart from the forward voltage drop the diode is a pretty cheap and simple solution.
As for overlooking something a typical example occurred when isolating the ignition and LC-1 controller. We left the ignition switch connected to the main batteries and used a relay activated by the ignition switch to connect the coil and LC-1 to the small battery. When we tested it all went well till we switched off the ignition. The engine continued running!!!

David
1982 Patrol K160 SWB (MQ) 4L P40 Petrol with Megasquirt fuel injection and EDIS ignition. Warn 8274 winch with Gigglepin head
The relay would be closed (ie ECU battery connected to starter) until power was switched to the winch solenoids (that's supply to solenoids, not signal) at which point it would open, and remain that way 'til power to winch solenoids was switched off.
I suggested this method as it will cater to the issues mentioned in point one of your post better than a 'smart' relay, which would be constantly switching during intermittent short winching. Incorporating some form of filter (spike protection) is probably another area worth addressing.
Another issue is your diode in series, which I feel is unnecessary. I can see your thinking on this, but in the real world such 'backfeed' would be so minor (if any) as to do far less damage to your small battery than keeping it half-charged.
cheers,
ed
I suggested this method as it will cater to the issues mentioned in point one of your post better than a 'smart' relay, which would be constantly switching during intermittent short winching. Incorporating some form of filter (spike protection) is probably another area worth addressing.
Another issue is your diode in series, which I feel is unnecessary. I can see your thinking on this, but in the real world such 'backfeed' would be so minor (if any) as to do far less damage to your small battery than keeping it half-charged.
cheers,
ed
I thought the same but when I spoke to Odyssey about connecting a PC1500 in parallel with a PC1200 they advised against it. Not sure why.-Scott- wrote:Don't worry about connecting a small battery in parallel with two large batteries. If they're all the same chemistry and same nominal voltage, it doesn't make any difference.
We did consider this but most of the ones we found such as the Redarc and BEP were not suited to our application. They are designed to stop your starter battery discharging below its minimum cranking voltage when your engine is switched off and you are using your fridge etc. Typically they have a cut-in voltage of 13.8V and a cutout voltage of 12.8 (BEP) or 12.5V (Redarc). So when you stop and are relying on your batteries to supply the fridge etc both batteries will be discharged to 12.5V and then the starter battery will be disconnected. On starting the starter battery will be charged to 13.7 before the relay closes again to allow charging of the auxiliary. We did not want our small battery being discharged to 12.5V before being isolated. And the diode was a lot cheaperIn place of the diode, you could consider a solenoid switched by a voltage sensing relay (VSR)

But if you know of an adjustable voltage high amp VSR let us know as that would be better than the diode as there would be no forward voltage drop.
David
1982 Patrol K160 SWB (MQ) 4L P40 Petrol with Megasquirt fuel injection and EDIS ignition. Warn 8274 winch with Gigglepin head
Are they?David_S wrote:I thought the same but when I spoke to Odyssey about connecting a PC1500 in parallel with a PC1200 they advised against it. Not sure why.-Scott- wrote:Don't worry about connecting a small battery in parallel with two large batteries. If they're all the same chemistry and same nominal voltage, it doesn't make any difference.

It won't be. Check your winch battery terminal voltage the next time you winch under load.David_S wrote:We did not want our small battery being discharged to 12.5V before being isolated.In place of the diode, you could consider a solenoid switched by a voltage sensing relay (VSR)
By connecting the sense line to one of the winch batteries the relay will switch when the terminal voltage drops under load - that's not the same as discharging to the same voltage. I expect the winch battery terminal voltage will drop below 12V almost instantly, so you'll get very little discharge from your small battery before it's isolated.
The Rover VSR is described here. If you can find one from a wrecker it should be quite cheap.
Having said all this, I think Ed's idea is worth pursuing further.
Hi Scott and Ed - thanks for the time you have taken inputting to this thread.
Scott, you are quite right the voltage drops way below 12V immediately you start winching - somewhere around 9-10V in most cases - so a voltage sensitive relay system would probably work.
And yes I did speak to Odyssey NZ about paralleling dissimilar batteries and they were quite clear that they did not advise it. I didn't ask them the reason as I could not really afford the PC1500 anyway. I will be calling them again about the charging requirements of the Odysseys as I don't want to stuff these batteries - they are not a throwaway item. Their recommendation against paralleling dissimilar batteries may be to do with the fact that these batteries will accept large charging currents but I am just guessing at the moment.
I may start a new thread on the subject of charging Odyssey and similar batteries but it seems that they require an initial charge of 14.2V to 14.8V followed by a trickle or float of 13.6V. The problem is how do you know when the batteries are charged and you need to switch to the lower charging voltage. To be on the safe side until I figure this out I will run my alternator at 14.6V during heavy winching sessions and 13.8V for normal driving and top up the batteries regularly with a proper charger. I will also probably remove the third battery for normal use keeping it just for events.
And let's not lose sight of the fact that the present isolating system worked well on the day I wanted it to and only cost $15.
And yes Ed I do have a 40A surge protector on my ecu circuit.
David
Scott, you are quite right the voltage drops way below 12V immediately you start winching - somewhere around 9-10V in most cases - so a voltage sensitive relay system would probably work.
And yes I did speak to Odyssey NZ about paralleling dissimilar batteries and they were quite clear that they did not advise it. I didn't ask them the reason as I could not really afford the PC1500 anyway. I will be calling them again about the charging requirements of the Odysseys as I don't want to stuff these batteries - they are not a throwaway item. Their recommendation against paralleling dissimilar batteries may be to do with the fact that these batteries will accept large charging currents but I am just guessing at the moment.
I may start a new thread on the subject of charging Odyssey and similar batteries but it seems that they require an initial charge of 14.2V to 14.8V followed by a trickle or float of 13.6V. The problem is how do you know when the batteries are charged and you need to switch to the lower charging voltage. To be on the safe side until I figure this out I will run my alternator at 14.6V during heavy winching sessions and 13.8V for normal driving and top up the batteries regularly with a proper charger. I will also probably remove the third battery for normal use keeping it just for events.
And let's not lose sight of the fact that the present isolating system worked well on the day I wanted it to and only cost $15.
And yes Ed I do have a 40A surge protector on my ecu circuit.
David
1982 Patrol K160 SWB (MQ) 4L P40 Petrol with Megasquirt fuel injection and EDIS ignition. Warn 8274 winch with Gigglepin head
Hi David, first off the is no reason why you can't parrallel dissimilar batteries, this is one of the many myths about automotive battery use that is based on nothing more than a missunderstanding of how batteries actually work.
For example, what is the difference between having two different types of batteries parralleled and the set you now have.
While the motor is running, all the batteries are fully charged from the alternator,. In your case you are going to pull a fair bit of power from the two crankers while both starting your motor and while winching, at which point you now have two dissimilar charged batteries.
The very same thing happens ( in reverse ) with any dual battery set up.
Just because you have identical batteries when you start out means nothing, they are still going to end up with different states of charge on a regular basis.
Next, the charging specs you have for your Odyssey batteries is base on a perfect charging system. This is NEVER going to be avilable in an vehicle charging system and you are far better off setting your alternator voltage up at 14.3 to 14.5 and leaving it there at all times.
This will give you near optimum charging time but means you can fit any type of automotive battery and not worry about it ever getting overcharged.
For example, what is the difference between having two different types of batteries parralleled and the set you now have.
While the motor is running, all the batteries are fully charged from the alternator,. In your case you are going to pull a fair bit of power from the two crankers while both starting your motor and while winching, at which point you now have two dissimilar charged batteries.
The very same thing happens ( in reverse ) with any dual battery set up.
Just because you have identical batteries when you start out means nothing, they are still going to end up with different states of charge on a regular basis.
Next, the charging specs you have for your Odyssey batteries is base on a perfect charging system. This is NEVER going to be avilable in an vehicle charging system and you are far better off setting your alternator voltage up at 14.3 to 14.5 and leaving it there at all times.
This will give you near optimum charging time but means you can fit any type of automotive battery and not worry about it ever getting overcharged.
2007 TDV8 Range Rover Lux
2009 2.7 Discovery 4
2009 2.7 Discovery 4
Thought I would update this thread as to what I am finally doing, but first thanks to all those who have contributed - gave me some ideas and helped me to clarify my thinking.
First I contacted Odyssey NZ about charging their batteries. Again they stated that they did not recommend paralleling dissimilar sized batteries. I could not follow their exact reasoning (I have not got much past V=IR in the electrical world) but the upshot of it was that one or other of the batteries would never be fully charged and this would reduce its life. As I stated earlier, to fully charge Odyssey batteries requires an initial charging voltage of 14.6V to 14.8V followed by a float or pulse charge of 13.8 V. (This is not generally available in a typical 4wd truck as Drivesafe observes). Odyssey recommend the use of a smart charger such as EPS or Ctek and advise that such a wall charger be used periodically to charge each battery INDIVIDUALLY to ensure both are fully charged. Ctek chargers have a special charging mode for AGM batteries such as the Odyssey and Optima.
In the case of my battery/charging set-up where I have an alternator capable of being switched between 13.8V and 14.6V output they agreed with my proposal that I generally keep the output at 13.8V but switch to 14.6V during and immediately after winching. However they still recommended periodic individual charging of each battery, including my ecu battery, with a 2 stage wall charger. They also made the point that the only way to check the state of charge of the battery was to test it with a digital voltmeter after it had been at rest (neither charging nor discharging) for at least 6 hours. A fully discharged Odyssey battery will have an open circuit voltage of 11.6V or less and a fully charged battery 12.8V (over 12.64 OK).
This periodic wall charging may seem a bit of a hassle but well worth it if it prolongs the life of the batteries. These Odyssey batteries are NOT cheap so any means of keeping them in top condition is worth the effort. So far I have been very impressed by their performance with no sign of power loss even at the end of a day of numerous short but heavy winches. Because of their very low internal resistance they can be rapidly recharged at high amperages. My only concern is that the PC1200 is a 44AH battery and on a prolonged continuous winch might run out of puff. However I was fortunate, though I cursed at the time, in that Odyssey NZ could not deliver my two PC1200s as promised so lent me two equivalent Enersys batteries in the meantime - a great service and much appreciated. With the experience gained with these I opted to upgrade to the PC1500 which has a higher CCA (880 v 550) and a 68AH rating. When trying them out at the weekend the effect of the higher CCA was noticeable. For normal winching with a single motor winch set-up the PC1200s would be fine and a lot lighter than the PC1500s.
Back to the original thread topic. I intend to keep my third (ecu) battery (the PC 535) though it will have to be relocated to make room for the PC1500. I will stick with the diode for the time being as it is a simple system which worked, and periodically recharge the PC535 with a wall charger. I will not link it to a relay operated by power to the winch solenoids, as Thylacine suggests, as if the winch batteries are drained during winching I want my ecu battery to remain isolated from the winch batteries on completion of winching until they are recharged. With the low internal resistance of these batteries I am still concerned that there might be a rapid discharge of the PC535 if connected to the PC1500s when they are at a low state of charge.
And a picture of my setup with the PC1200s installed.
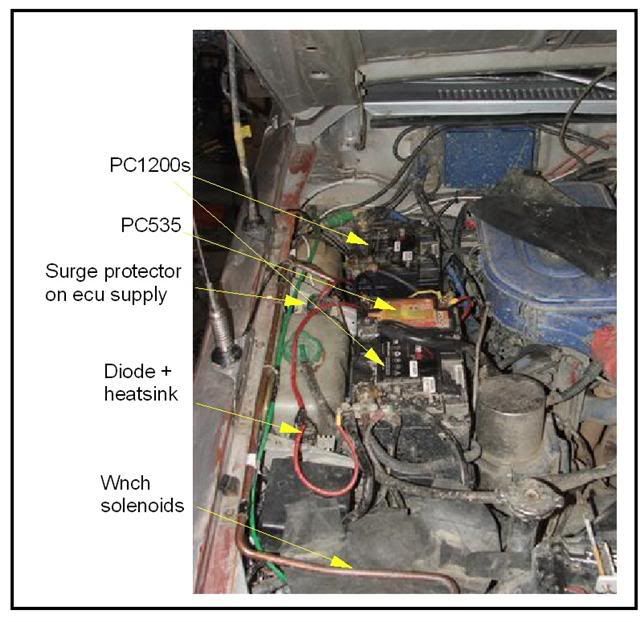
David
First I contacted Odyssey NZ about charging their batteries. Again they stated that they did not recommend paralleling dissimilar sized batteries. I could not follow their exact reasoning (I have not got much past V=IR in the electrical world) but the upshot of it was that one or other of the batteries would never be fully charged and this would reduce its life. As I stated earlier, to fully charge Odyssey batteries requires an initial charging voltage of 14.6V to 14.8V followed by a float or pulse charge of 13.8 V. (This is not generally available in a typical 4wd truck as Drivesafe observes). Odyssey recommend the use of a smart charger such as EPS or Ctek and advise that such a wall charger be used periodically to charge each battery INDIVIDUALLY to ensure both are fully charged. Ctek chargers have a special charging mode for AGM batteries such as the Odyssey and Optima.
In the case of my battery/charging set-up where I have an alternator capable of being switched between 13.8V and 14.6V output they agreed with my proposal that I generally keep the output at 13.8V but switch to 14.6V during and immediately after winching. However they still recommended periodic individual charging of each battery, including my ecu battery, with a 2 stage wall charger. They also made the point that the only way to check the state of charge of the battery was to test it with a digital voltmeter after it had been at rest (neither charging nor discharging) for at least 6 hours. A fully discharged Odyssey battery will have an open circuit voltage of 11.6V or less and a fully charged battery 12.8V (over 12.64 OK).
This periodic wall charging may seem a bit of a hassle but well worth it if it prolongs the life of the batteries. These Odyssey batteries are NOT cheap so any means of keeping them in top condition is worth the effort. So far I have been very impressed by their performance with no sign of power loss even at the end of a day of numerous short but heavy winches. Because of their very low internal resistance they can be rapidly recharged at high amperages. My only concern is that the PC1200 is a 44AH battery and on a prolonged continuous winch might run out of puff. However I was fortunate, though I cursed at the time, in that Odyssey NZ could not deliver my two PC1200s as promised so lent me two equivalent Enersys batteries in the meantime - a great service and much appreciated. With the experience gained with these I opted to upgrade to the PC1500 which has a higher CCA (880 v 550) and a 68AH rating. When trying them out at the weekend the effect of the higher CCA was noticeable. For normal winching with a single motor winch set-up the PC1200s would be fine and a lot lighter than the PC1500s.
Back to the original thread topic. I intend to keep my third (ecu) battery (the PC 535) though it will have to be relocated to make room for the PC1500. I will stick with the diode for the time being as it is a simple system which worked, and periodically recharge the PC535 with a wall charger. I will not link it to a relay operated by power to the winch solenoids, as Thylacine suggests, as if the winch batteries are drained during winching I want my ecu battery to remain isolated from the winch batteries on completion of winching until they are recharged. With the low internal resistance of these batteries I am still concerned that there might be a rapid discharge of the PC535 if connected to the PC1500s when they are at a low state of charge.
And a picture of my setup with the PC1200s installed.
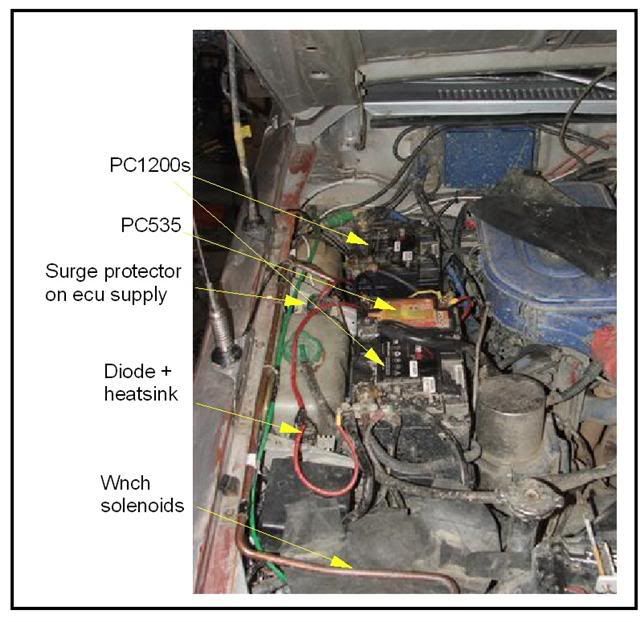
David
1982 Patrol K160 SWB (MQ) 4L P40 Petrol with Megasquirt fuel injection and EDIS ignition. Warn 8274 winch with Gigglepin head
Who is online
Users browsing this forum: No registered users and 1 guest