If you don't know what a rear main leak is or where to look for the leak - have a look in the gap between the rear of the sump and the gearbox.
Oil can be found leaking down the front of the rear plate or from the inside of the bellhousing. It's tempting to think it is the sump gasket leaking (as I did) but usually it will be the rear main seal.
The rear main on my LN106 was leaking from the time I bought it and I did have success in slowing the leak by using an oil additive that swells the seal called 'Rislone rear main seal repair' which cost $30. It only lasts as long as your oil change and I'm not sure of any long term effects of using it.
http://www.supercheapauto.com.au/online ... 950mL.aspx
Eventually, as expected, the leak got worse - much worse. The point at which I decided to fix it properly was when I found the entire underside of my Hilux coated in black engine oil after a trip on the highway after the most recent oil change.
I had oil being flung off the flywheel at such speed the oil was coming out the gap between the bell housing and cover plate spraying onto the passenger side chassis rail.
After a quote of $600 to replace the seal from a gearbox place I set about researching doing the repair at home in my shed with minimal tools.
My googling found plenty of forum treads with people asking how hard it was to do at home but I couldn't find any guide with pics. The video below is fairly good but it's for an '88 IFS 'Pickup' (Hilux in the US) with a petrol engine. Also this guy had a hoist and a transmission jack...
http://www.youtube.com/watch?v=CKonG0UVqYE
This is a generic video on rear main seal replacement that was also helpful
http://www.youtube.com/watch?v=TPskVbX6CIQ
Another invaluable site that any Toyota owner should bookmark is the ToyoDIY site as it shows the Toyota part numbers - very useful when ordering genuine parts. Below is the LN106 link but it covers all Toyota's.
http://www.toyodiy.com/parts/p_G_1994_T ... _1106.html
I ended up doing the repair over the Anzac long weekend and below are the steps I took with pics and any pitfalls that need to be watched for. Originally I intended to take more pics but it's a pretty messy job so I ended up taking less than expected.
Parts to get prior to the job:
1. 'Genuine' Toyota Rear main seal - part #90311-85007 $77 (quote from Toyota)
I got mine off a guy on ebay who bought the genuine seal but didn't do the install. It was actually an NOK AH3836P and the one that came out was also an NOK but it had a V at the end of the code rather than a P I think. I read plenty of treads saying only get genuine as cheaper seals leak. I also read that genuine toyota = NOK which is what I have found.
2. Oil seal retainer gasket - part #11383-54030 $12 from memory
Some people change the seal without removing the retainer but for my repair I decided to take it out.
3. 'Speedi Sleeve' 85mm - $40 from BSC or bearing shop
This is optional but considering the time this repair takes it would be advisable to get one in case you need it. I didn't get one and when I discovered that I could do with it the bearing places were closed and I had to get the car running by Monday. Read on to see why it could be needed and what I did to get around not having one.
4. Gear shift boot - part #33555-20060 $14
You may not need this but when you get to the point of removing the gear sticks this is the seal/boot that stops gear oil escaping out the top of the gearbox. Mine was perished and oil was leaking out. There is also one on the transfer but as that gets used a lot less mine was ok.
5. Some sort of silicone gasket maker
6. Impact wrench
Again probably not essential but a decent (500Nm +) impact will be helpful, especially for removing the flywheel. The cheap 300Nm impacts are virtually useless (as I found out).
7. Wobble extensions and 500mm extension bar
Stricktly speaking you could do this without the wobbles - probably - but they make it so much easier. I got three wobble extensions on ebay for $17 - shown all together below but when you actually use them only one or two are needed linked together. The 500mm extension was $15 at supercrapauto. You will need the 500 to get the top transmission bolts out and the exhaust off.
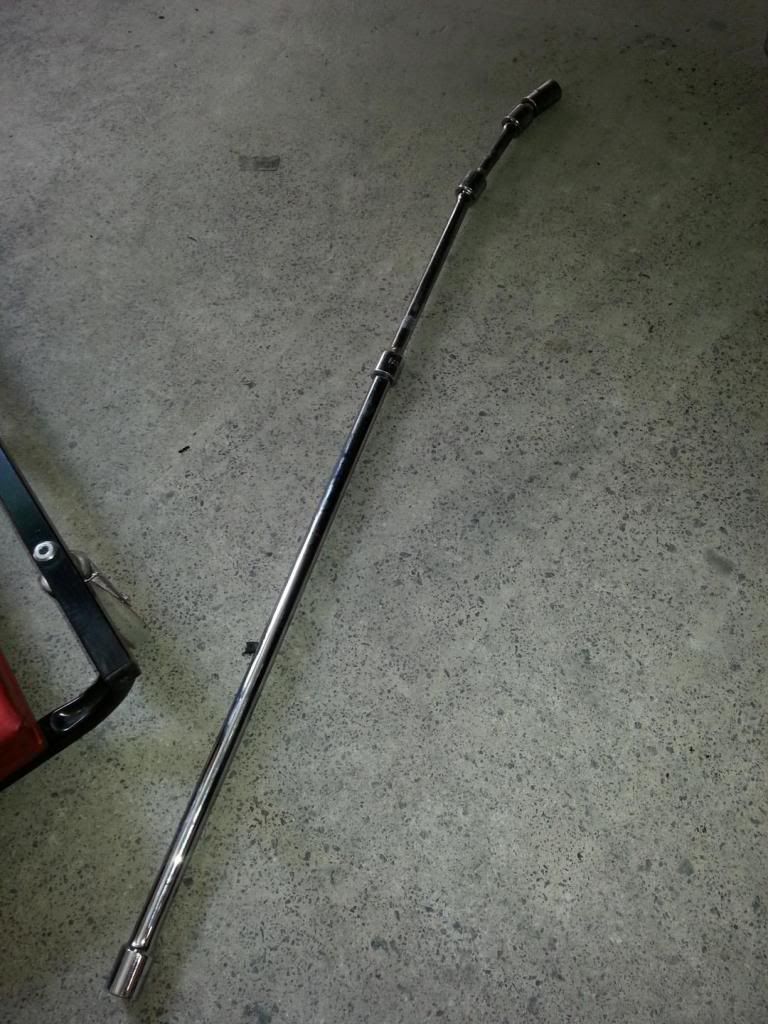
8. A transmission jack of some sort to hold the gearbox
I made my own transmission jack using a trolley jack with 500mm reach, some steel plates I had, scraps of wood and ratchet straps. The steel plate was bolted to the trolley via two tapped holes I made in the top of the jack.
This allowed me to remove the gearbox and transfer as one. Without some sort of jack that you can hold the gearbox/transfer level (in both planes) on you will have to split them. The reason for this is the weight and the offset of the transfer will cause the whole thing to twist to the drivers side when split from the engine if it isn't secured to a sold platform.
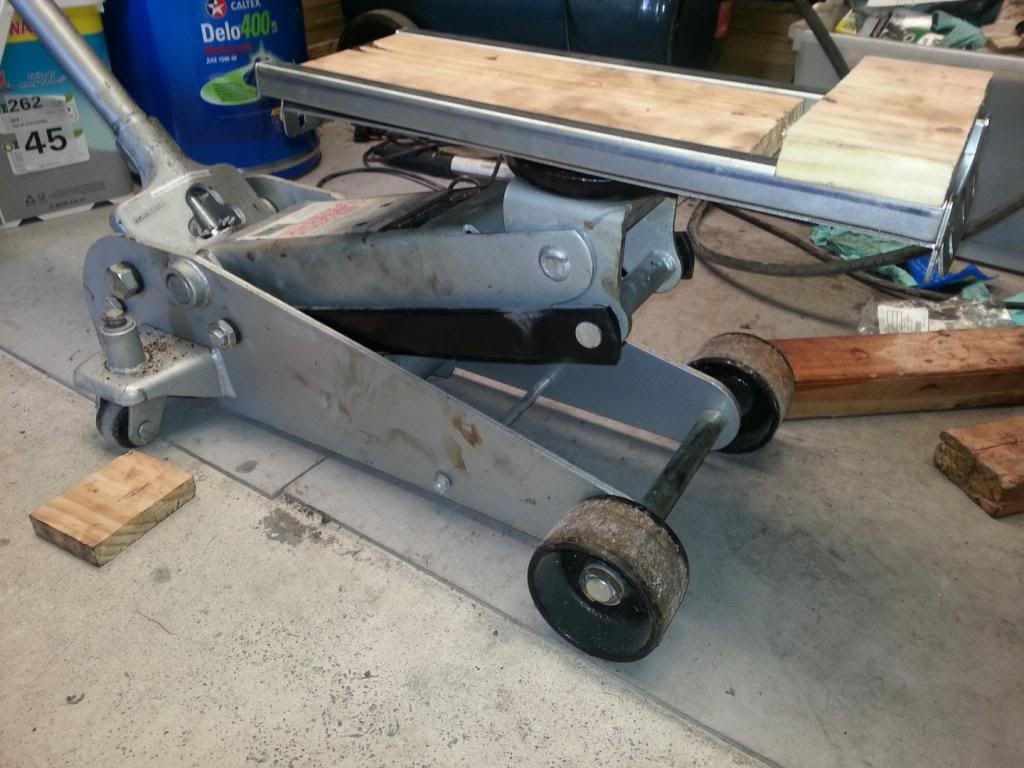

I used blocks of wood so the ridges on the cast alloy transmission would bite in rather than slide around.
The front of my Hilux had to be jacked down by removing the wheels and putting the axles onto stands. this was so the jack could reach the transmission but it also made the bottom of it level with my jack as it tends to slope when the car is at normal ride height.
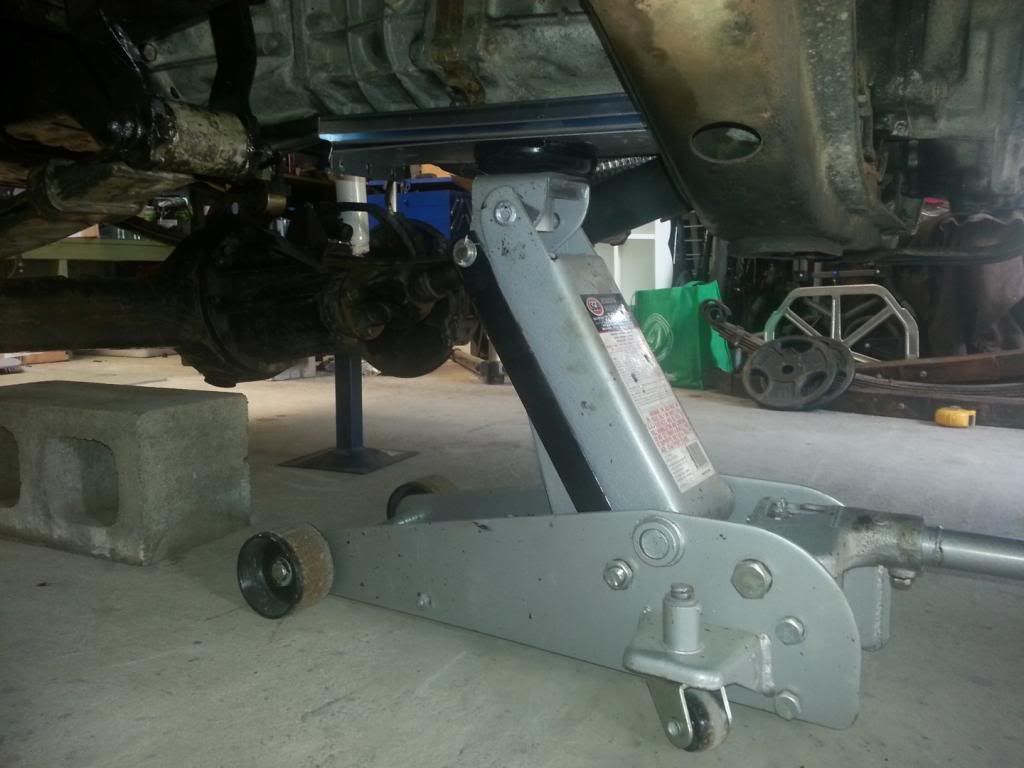
9. A clutch kit if you plan to do that at the same time - I didn't.
Now onto the repair..
I'm going on memory here so if I have left anything out that others pickup or another easier way to do somthing feel free to chime in.
I wanted to try and put all the info into a single thread for anyone else contemplating this repair.
First - disconnect the battery to avoid forgetting before you tackle the starter motor and get a surprise when you short it.
The gear and transfer sticks need to come out to allow the gearbox to move back and clear the input shaft. You might as well do this while still clean. Remove the trim and access the sticks. The gear stick is held in with a spring loaded clip that is pushed down and twisted to release. The transfer is held in with a circlip.
You can see one of the ratchet straps I used to strap the box to my jack. This is also when I discovered my gear stick boot was leaking - you can see the oil around the front hole.
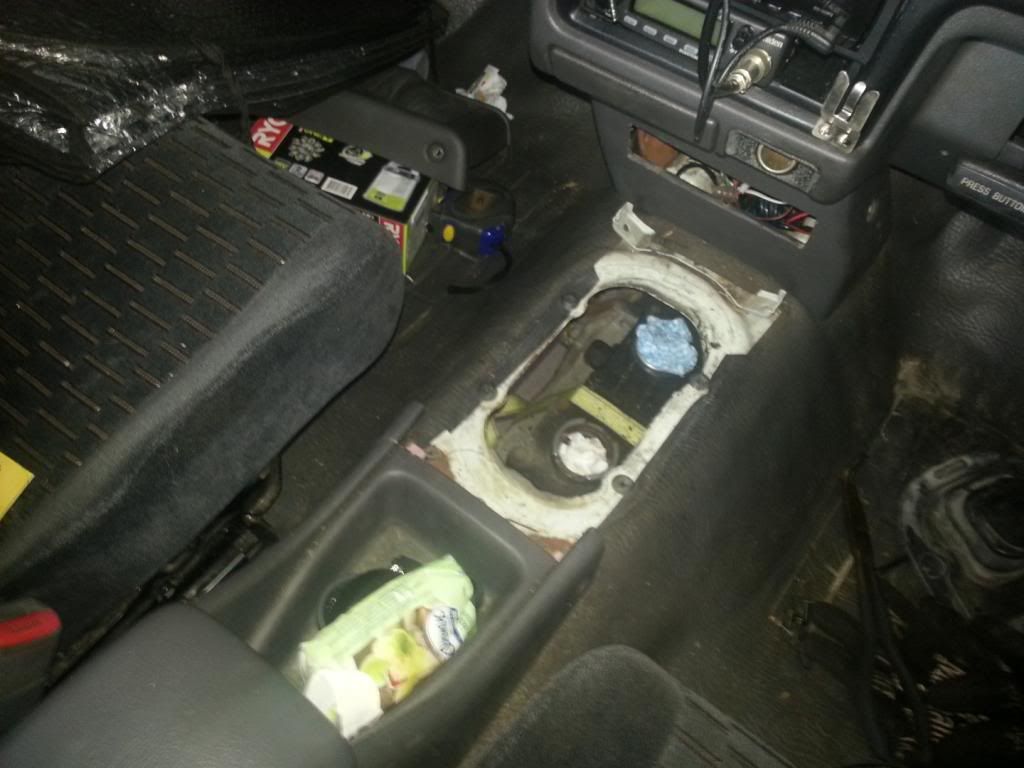
Get your jack under the gearbox and take the weight of the gearbox with the jack and strap it on tight.
Remove the crossmember - I had a bolt head snap off while doing this. I also found out at this point how useless a 300Nm impact is. There are eight obvious 17mm bolts that hold it to the chassis and 4 bolts accessed through the bottom of the crossmember that hold the transfer rubber mount to the crossmember.
Other things to remove to help with access and allow the gearbox to drop out:
Exhaust - this will vary depending on your setup.
Front and rear drive shafts - Mark the shafts/yolks for reassembly (to do with balance I think). Jack a rear tyre up so you can rotate the tail shaft for access to the bolts.
I removed the front drive shaft at the transfer case once the crossmember was out and slid it off the slip joint leaving the other end attached to the front diff.
Now that the access to the bellhousing is clear the real fun can begin.
Most of the bolts that hold the gearbox to the engine are fairly easy to access however the top three are more difficult.
Access to these bolts is made easier by lowering the gearbox and allowing the engine to twist on the mounts giving more room between the tunnel and gearbox. A body lift would help here too (I don't have bodylift).
BEFORE you go lowering the gearbox there are some things to be aware of:
The top radiator hose will be stretched as the motor move so undo the hose clamps to avoid any disasters. Mine moved a fair bit but just stayed on the pipes so no leaking coolant. If I left the the top hose clamped it would have broken something.
My heater piping fouled on the clutch slave so I had to loosen it from the firewall to let it move aside.
The radiator clutch fan could *possibly* puncture the radiator if left lower too far. Mine fouled the shroud before it got near the radiator but I'm mentioning it as it would really suck to hole a radiator in the middle of this.
Apparently the inlet pipe from air box can also be twisted/ broken but I have a Turbo with silicone joints so it wasn't a problem for me.
I found that I could actually get the top bolts on the passenger side out without tilting the engine back. My gearbox seemed to sit slightly off center to the drivers side in the tunnel. The arrows show the top bolts on the passenger side. The starter will come off once you have taken out all the upper passenger side bellhousing bolts.
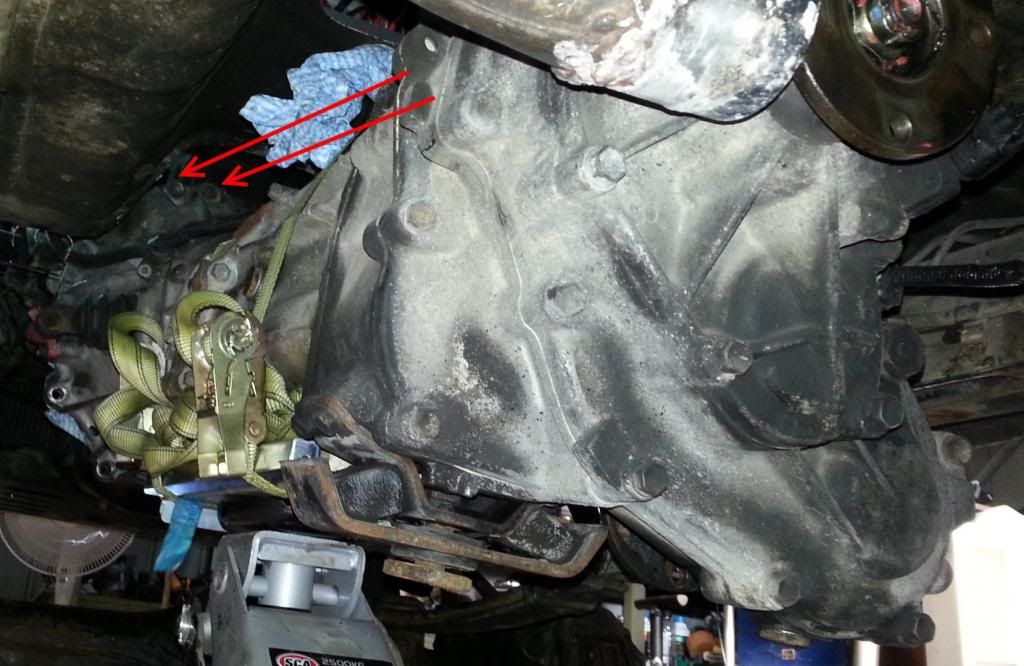
The single top bolt n the drivers side was another matter. The drivers side has less room between the gearbox and tunnel as well as having the exhaust and drive shaft (if not removed) in the way of your extensions.
This was probably the only real problem I encountered in the whole process. Basically I tried to get it out without lowering the gearbox and the extensions, even with the wobble, couldn't get a good angle on the bolt which meant the socket wasn't square on the bolt. I almost rounded the bolt head until I lowered the engine to get a straight angle on the bolt.
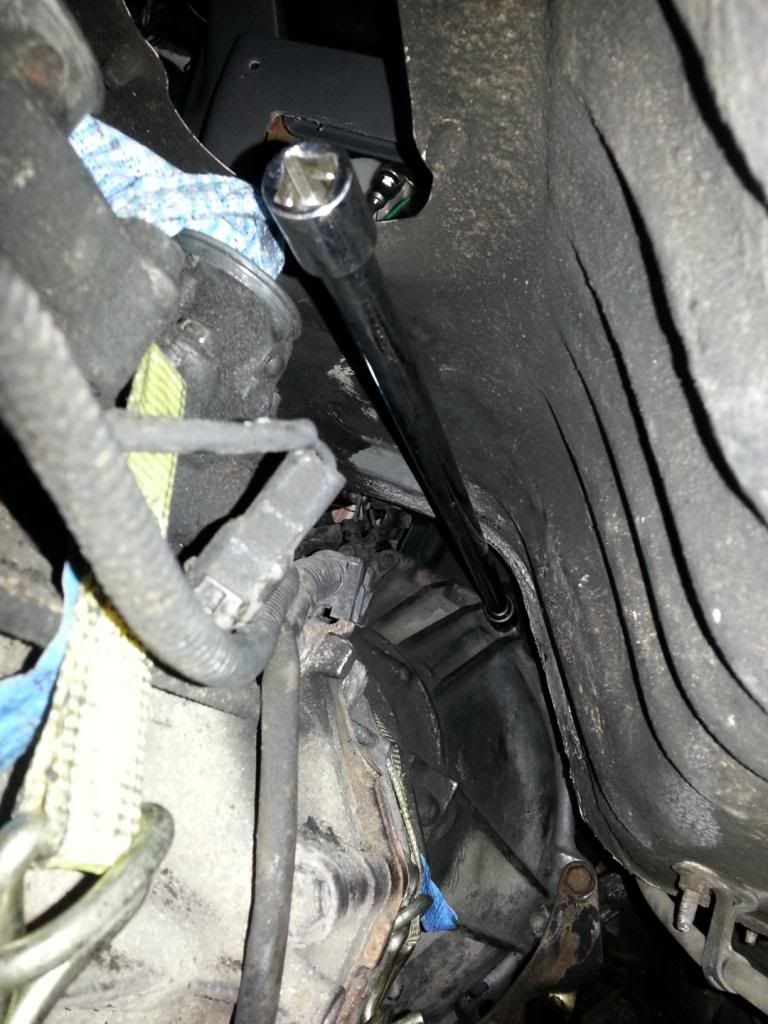
There is a wiring harness of sorts attached to the gearbox that runs to the starter motor for reverse light, speedo and 4wd indicator. Remove the three connectors and the clips that hold the harness to the box and pull it up to sit with the starter motor.
Time to split the gearbox from the motor.
It won't just slide apart - I found I had to get a pry bar between the engine block and the rear engine plate to lever the two apart. Once apart lower it and move it out of the way.
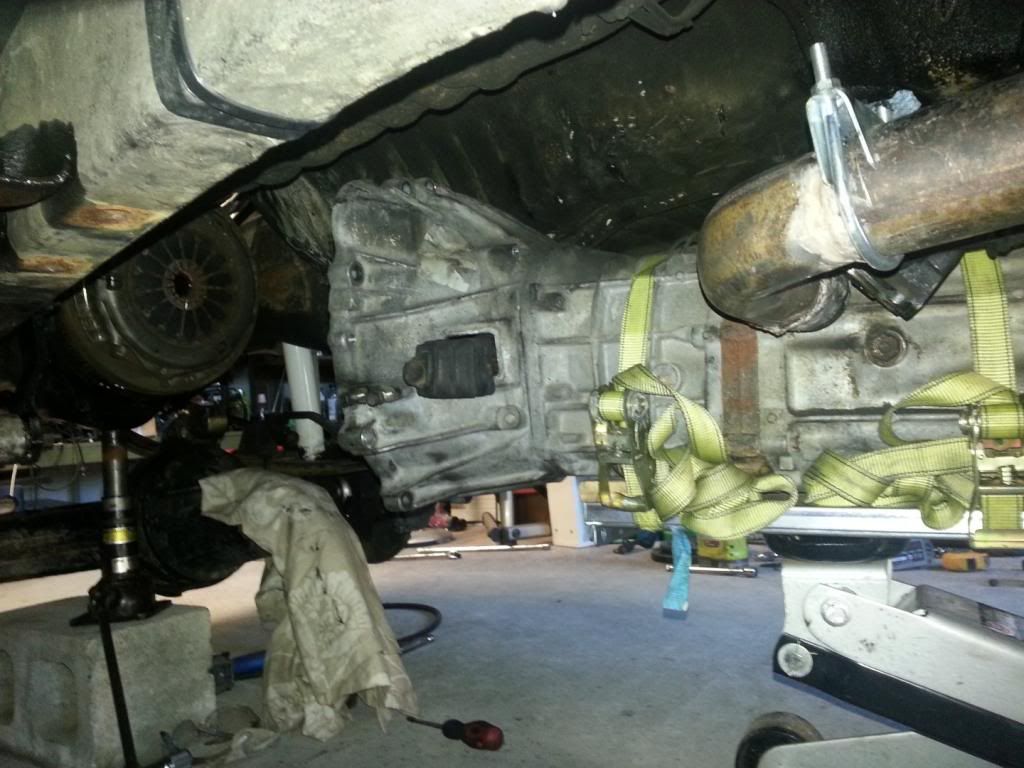
Next to come off is the clutch.
Mine was still in good condition but many other treads I read suggested changing the clutch at the same time as you have access to do it. I was also surprised to find a genuine Toyota clutch in it.
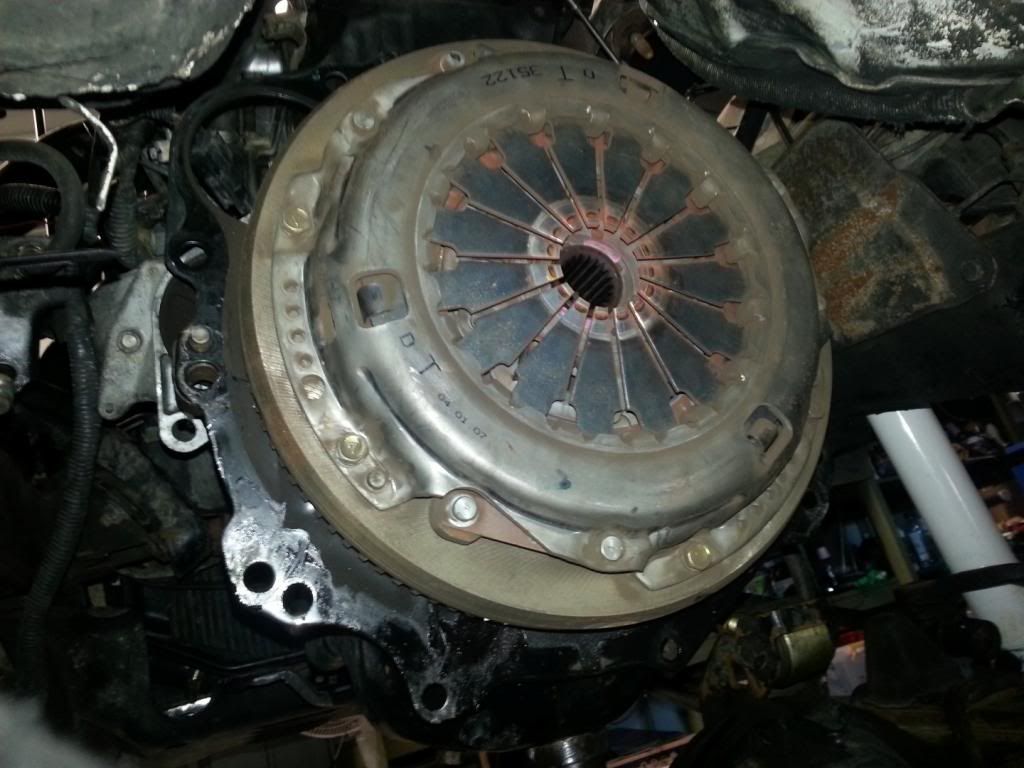
Once the clutch is off the flywheel bolts and rear engine plate bolts are accessible. I didn't get any pics of these still installed. An impact wrench is a real help for the flywheel bolts as they are on TIGHT and the flywheel will rotate if you try to use hand tools which means you need to hold it with some steel angle.
Be prepare for the weight of the flywheel when removing it - it's heavy.
Once the flywheel and end plate are removed you get your first look at the rear main seal.
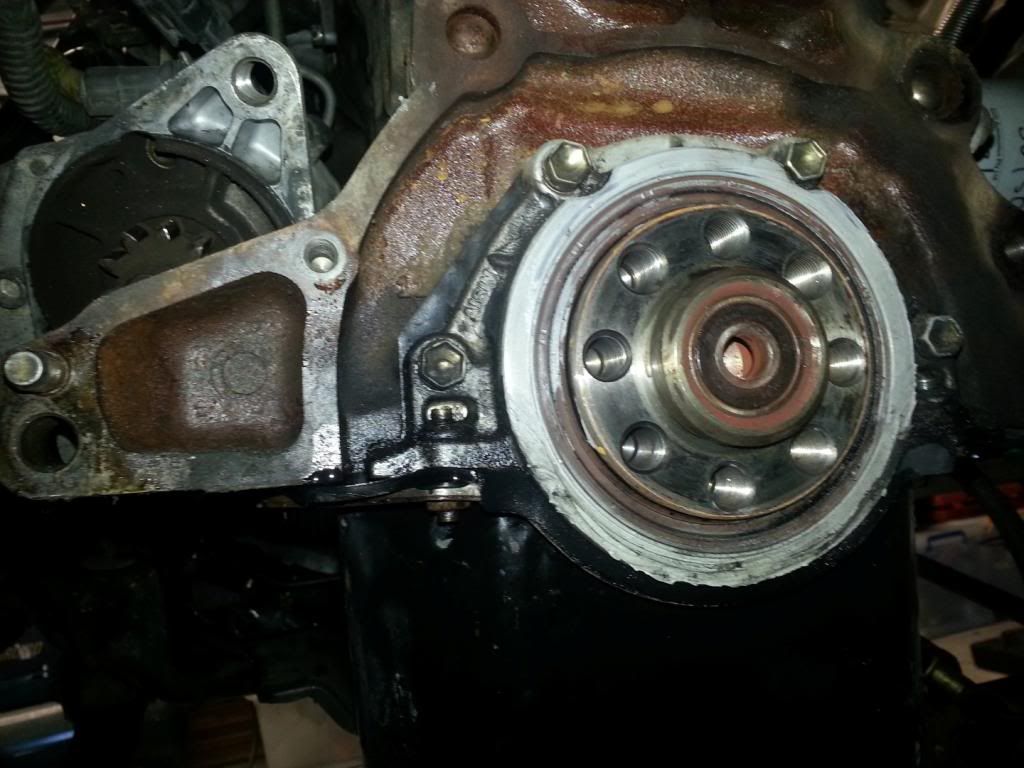
I chose to replace the seal with the seal housing removed from the engine. To do this the two studs in the sump pan directly either side of the rear main seal need to come out as well as the bolts that hold it to the engine block.
The pic below shows the hosuing removed and the diameter of the crank - 85mm.
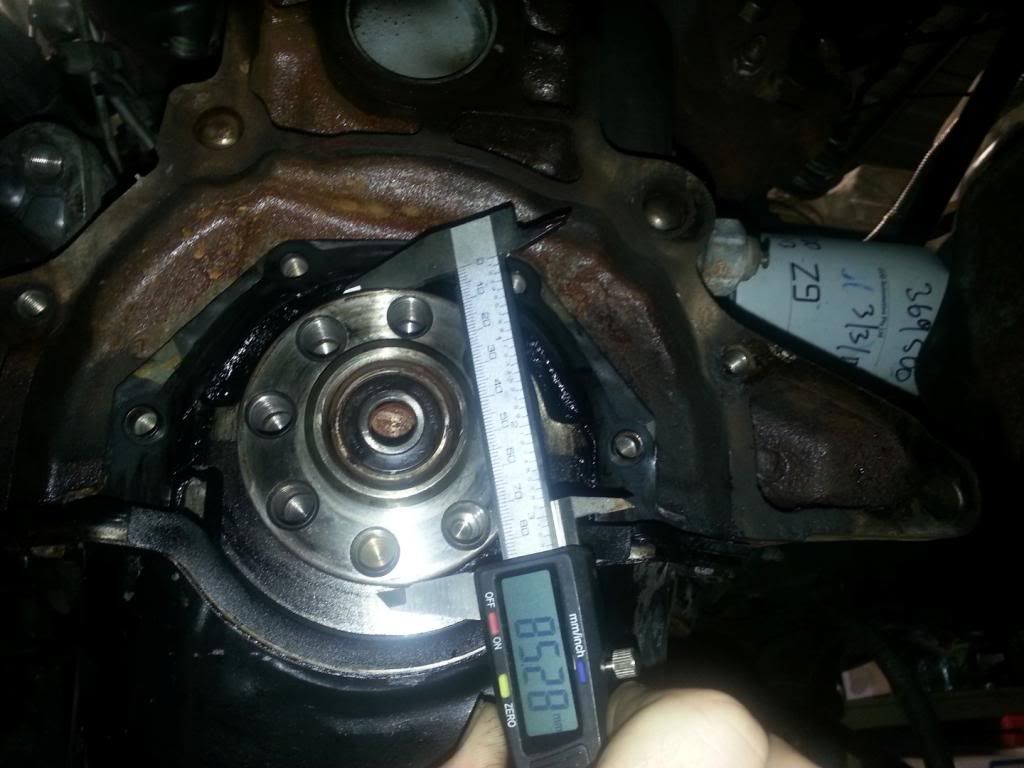
It's apparently fairly common for the seal to wear grooves into the crank where the lips run against it. This is where a speedi sleeve comes into play as it goes over the crank to give a new surface for the seal to run on.
Mine certainly had wear on the crank.
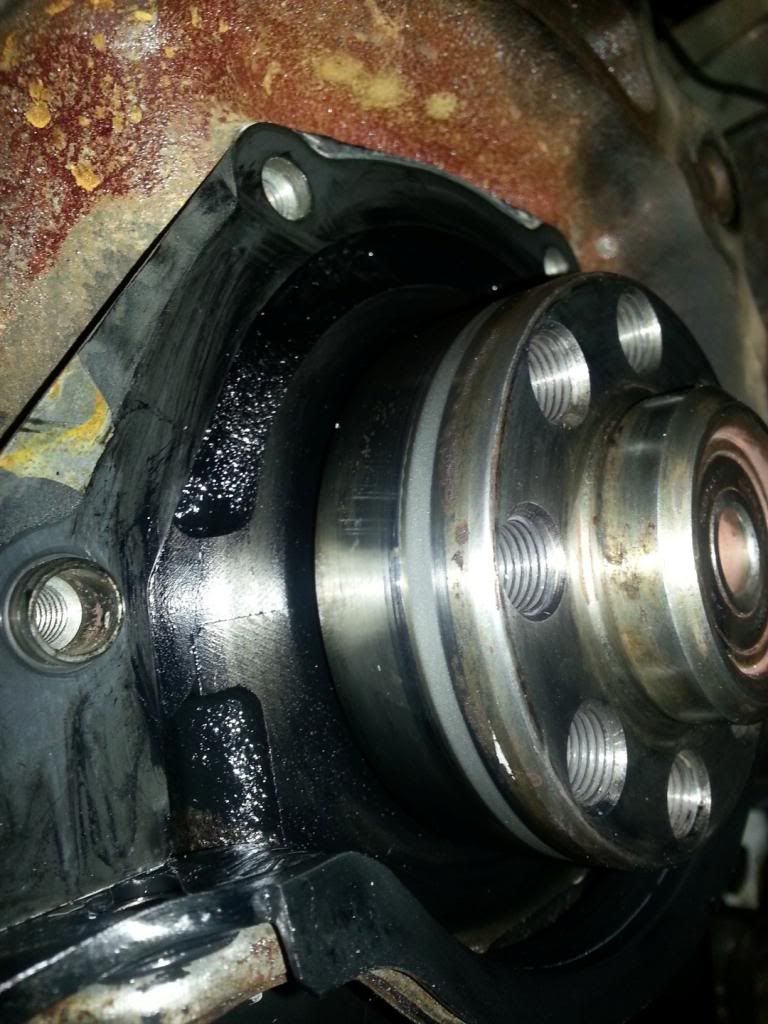
If I did it again I would probably have used a speedi sleeve. However as I didn't have one, and needed the car running again by Monday, I decided to mount the new seal further back in the housing so it would not be running in the groove worn by the old seal.
Usually the seal is aligned flush with the front of the housing. I decided to align the rear of the seal with anther groove in the housing as shown below.
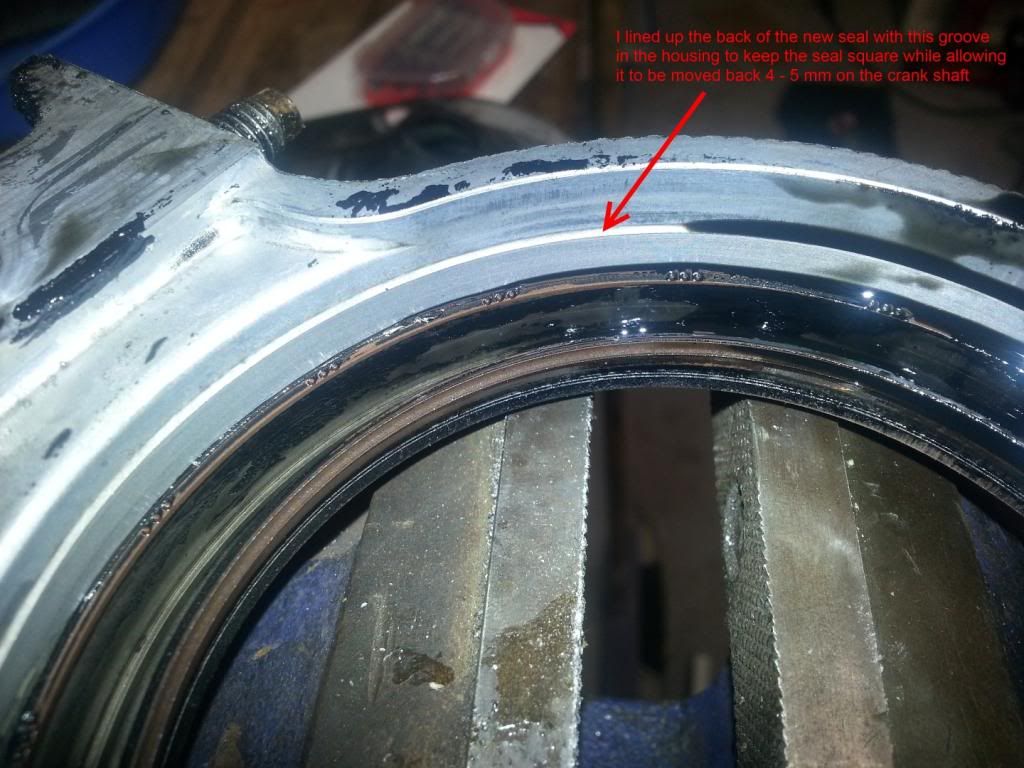
This resulted in the seal moving back 4-5mm on the crankshaft so avoiding the wear marks on the crank.

Remove the old seal by putting a screw driver into the back of the seal and tapping it out with a hammer. You can then use the old seal to drive the new one in. Make sure the seal goes in square. I lubed the new seal with some grease prior to re-installing.
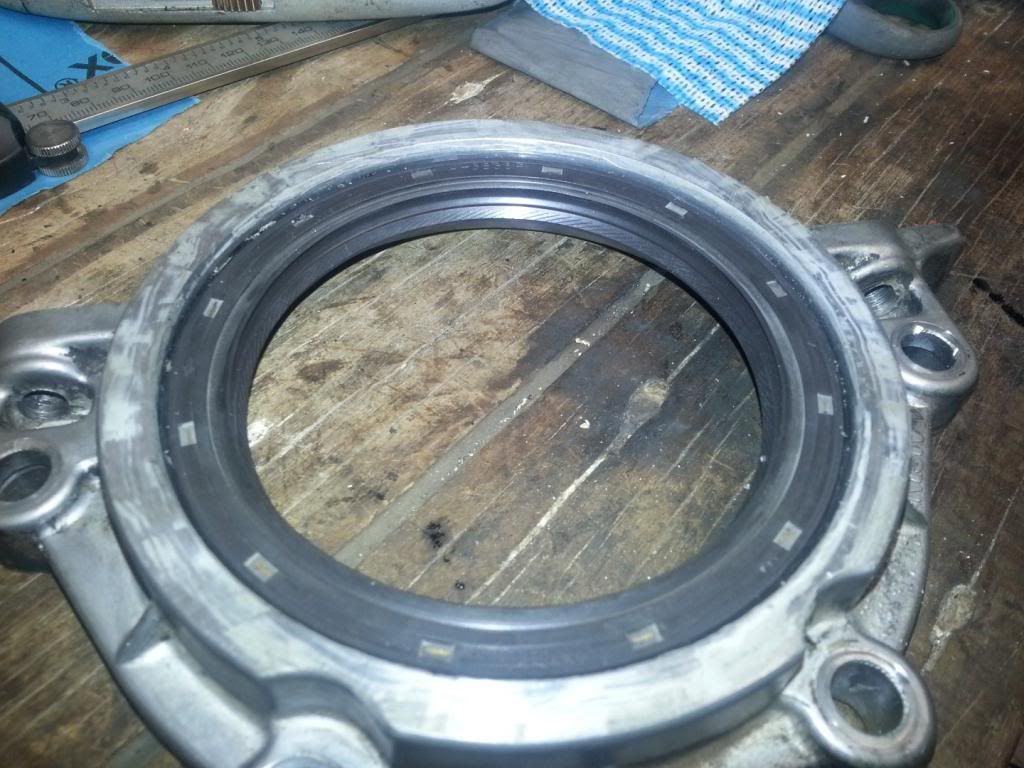
Clean the crank with some very fine sandpaper to get any rust or gunk off then wipe it up with brake clean to get a clean surface.
I also decided to use some silicone gasket maker on my new gasket and between my sump gasket as extra insurance against any leaks. There wasn't any on the original gasket I took out.
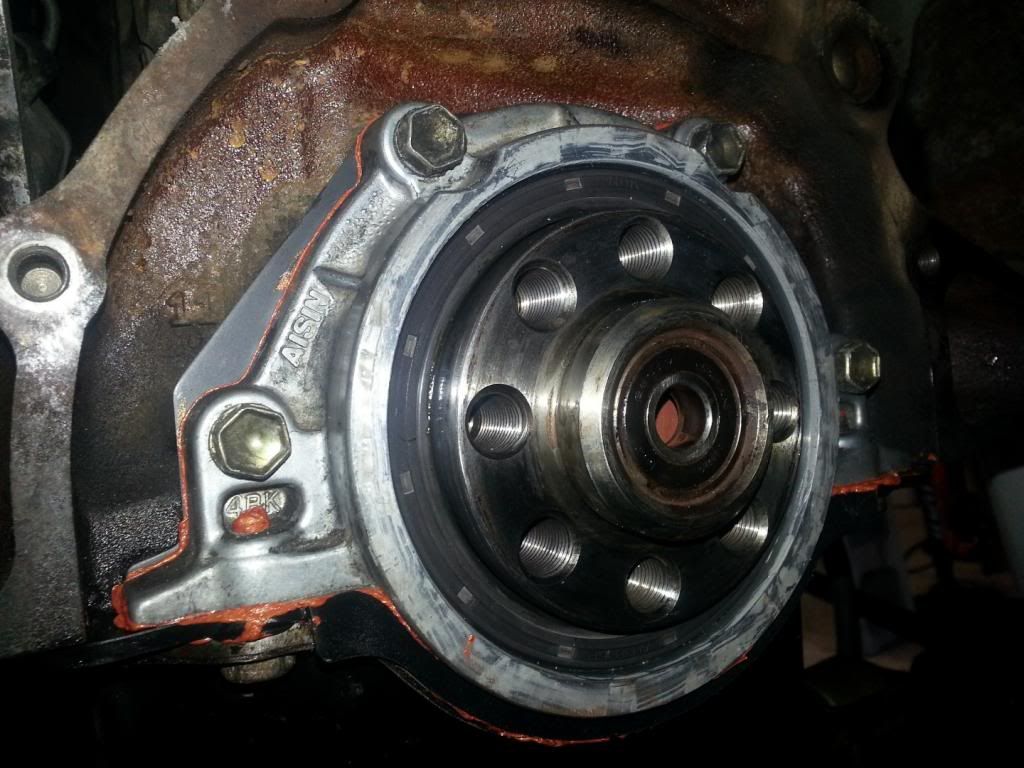
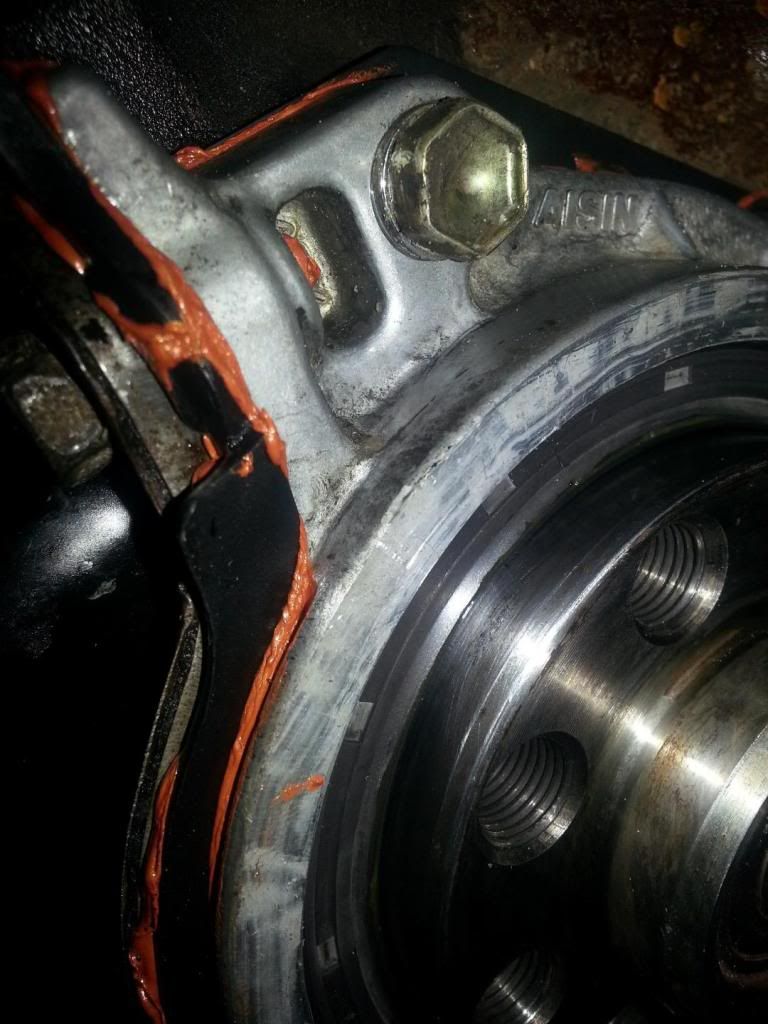
Once the seal is in it's time to re-install everything.
I'll only add notes on anything unusual as re-install is really just the reverse of what you did earlier.
The flywheel will need to be held with some metal angle so you can torque the flywheel bolts back down. Get a download of the service manual for the specs but I think it was 90 or 120 ft-lbs. It's tempting to use the impact but i read online of someone that caused cracks in the crank shaft by doing that.
Getting the gearbox back onto the engine was made easier by using a jack under the sump to align the engine and gearbox.
It went back together much easier than it came apart for me.
I realise the sump is thin walled but it isn't the whole weight of the engine on it. You're really just moving it on the engine mounts.
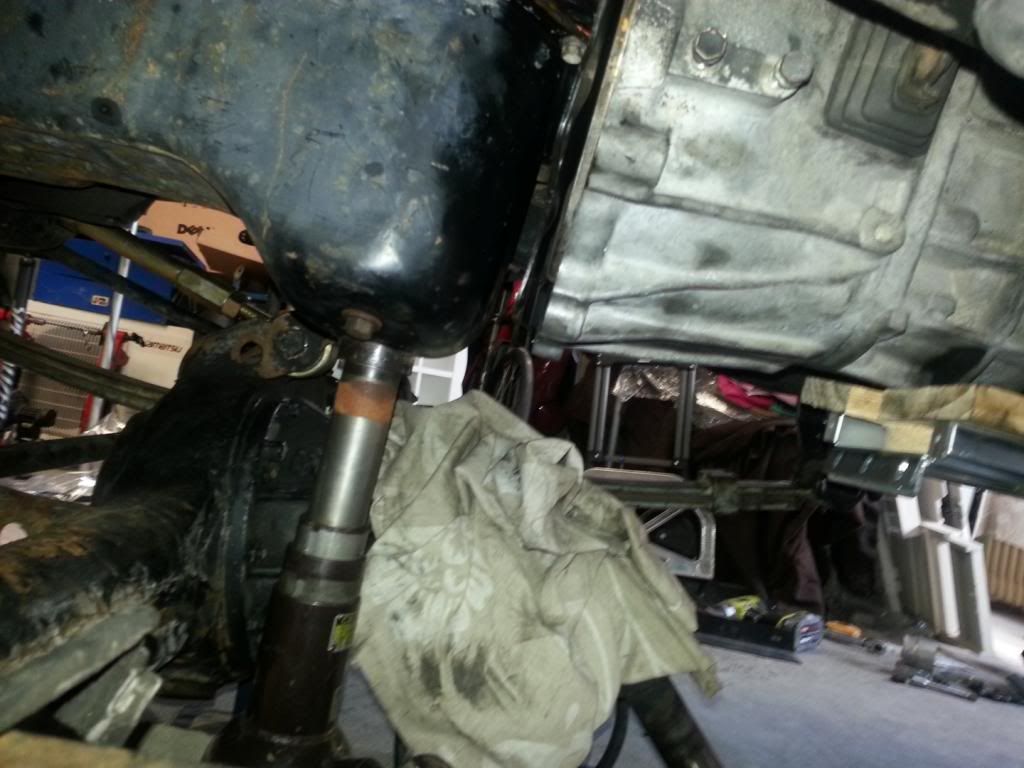
Re-install the front drive shaft before the gearbox crossmember as access is restricted with it on.
Don't forget to tighten up your radiator hose or anything else (eg clutch master) that you had to undo to lower the gearbox.
That's all that I can remember worth noting on re-install.
Overall the repair was time consuming - mainly due to getting old bolts undone and figuring out how to get to the drive side top bellhousing bolt. Doing it a second time would be much quicker.